#pathtozerocarbon, #sustainability
11 – Structure: Steel, Concrete + Wood
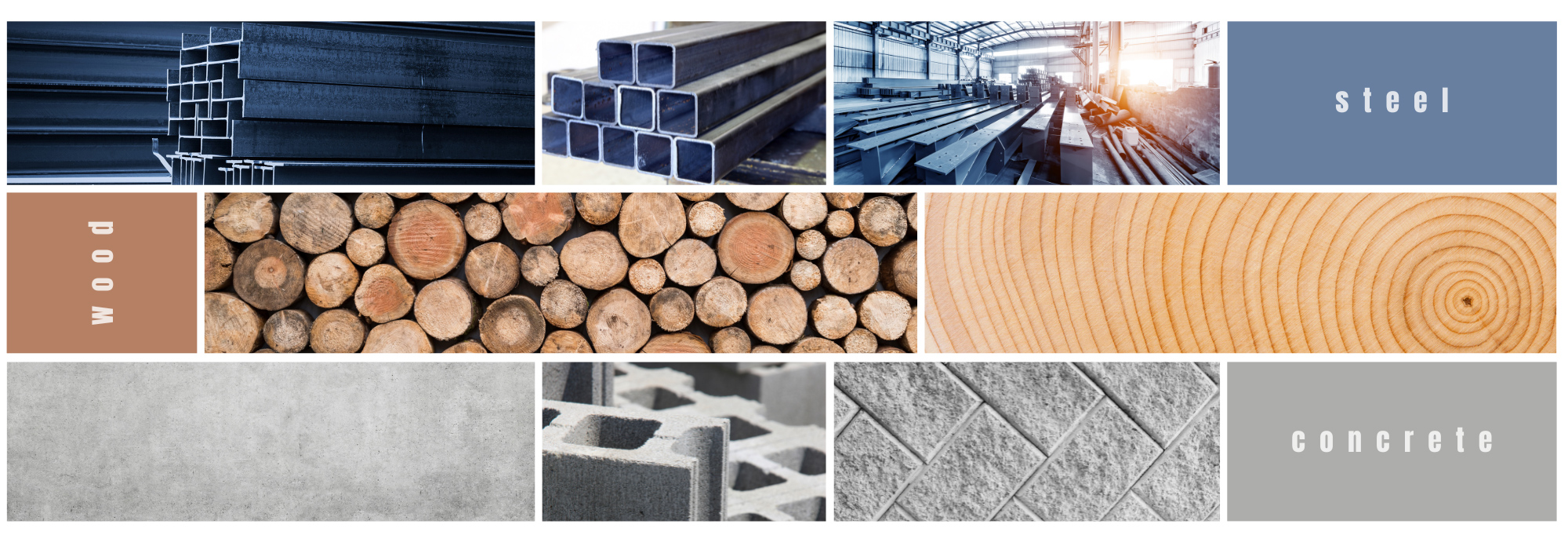
Concrete, steel, and wood are by far the most common building structural materials. Concrete and steel use accounts for roughly 21% of global carbon pollution (about half of which is from the built environment). Wood structures often have significantly lower emissions than steel or concrete, but forests worldwide do not contain enough timber to construct all buildings out of wood, and clear cutting all forests would have significant environmental and ecological damage even if it was possible. Responsibly sourced wood structures, however, are an important strategy on the path to zero carbon.
Our best future requires rapid reductions in structural embodied carbon across all three main structural materials. There are easy wins for all projects right now (see below). The path to decarbonize steel and concrete will be a longer process, requiring rapid research and development of carbon-efficient manufacturing, encouraged by demand from developers and design teams for these materials, and increasingly required by low-carbon policies. Wood has a very different challenge: we don’t have good data yet on the comprehensive impact of forestry, so carbon calculations may be under- or overstating the impact of a given product.
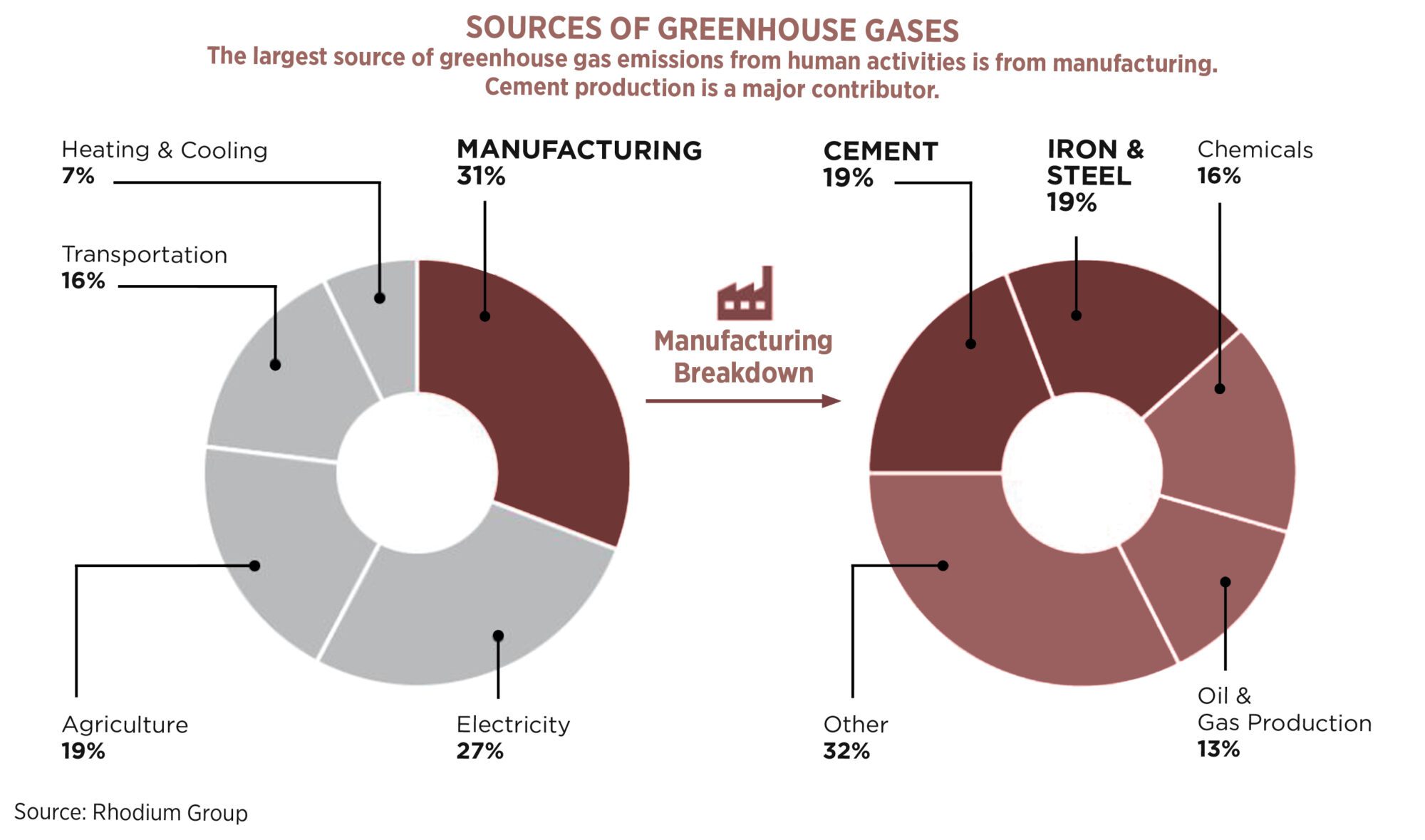
Cement (aka Portland cement, the primary ingredient in concrete), and iron/steel account for a significant percentage of manufacturing emissions worldwide. Since much of this production occurs outside of the US, our national greenhouse gas accounting doesn’t include these emissions even when we use the products. Demanding low-carbon construction products will drive up demand for best practices in the manufacturing industry worldwide. Read more. Note that the overall categories are different than this Post 01 chart, while Post 06 additionally includes land use.
The Basics
The SE 2050 (Structural Engineers 2050, created by the Carbon Leadership Forum) is helping lead the industry, developing many resources on embodied carbon, including case studies, rating system applicability, reductions, a page on getting started with embodied carbon, a soon-to-be-released SE 2050 LCA Methodology Guide and more. The SE 2050 also has a quick calculator to estimate embodied carbon from structural materials. A growing list of resources including strategies and timing to reduce embodied carbon.
From an embodied carbon accounting perspective we know more about structure than any other building system. This is because a building’s structure is primarily composed of a relatively few materials that are often the largest single-material purchases on a project: steel, concrete, and wood. Plant and vendor-specific embodied carbon data is available for many concrete mixes (though primarily in urban areas) and steel products, but we have minimal embodied carbon data from specific wood suppliers yet.
Most analyses of whole buildings over-represent the embodied carbon impacts of structure, because most so-called Whole-Building Life Cycle Assessment (WBLCA) are limited to include only structure and envelope; this creates industry confusion and results in structure commonly understood as the largest source of emissions. When including other emissions (Post 02), structure often accounts for between a quarter and a half of the total carbon emissions.
As the longest-lived component of a building (Post 09), the most important carbon consideration in structure is that it provides a long service life for a building. Building Reuse (Post 10) depends on adequate structure that anticipates future needs, and structural failure can lead to an entire building being demolished, causing substantial emissions for demolition and rebuilding.
General strategies:
- Look for low-carbon structural materials, including responsibly sourced wood structure.
- Material Efficiency: Minimize material use by avoiding transfers, heroic cantilevers, and excessive building modulation
- Ask for EPDs for all major structural materials
- Require steel and concrete products to meet performance criteria for being lower than the estimates from the latest CLF Material Baseline Report. The baselines can be chosen for ‘High’ (80% of products are lower), ‘Typical’ (50% of products are lower), or ‘Low’ (only 20% of products have lower embodied carbon). Require wood to have sourcing traceability through the supply chain, showing it comes from well-managed forests that avoid harvesting from prime or previously unlogged forests that are not part of a restorative management plan.
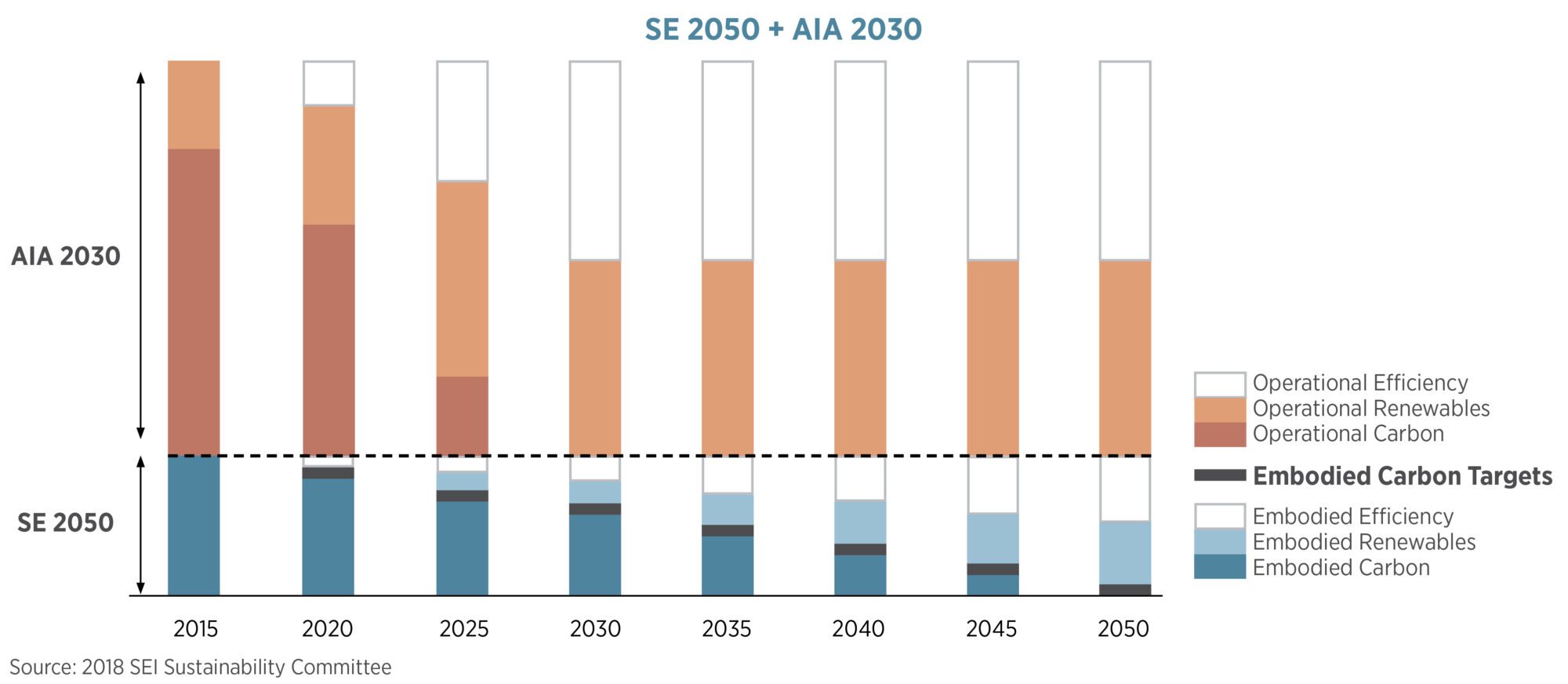
This chart overlays the goals of the American Institute of Architects AIA 2030 Commitment for operational carbon intensity (based on the 2030 Challenge) and the Structural Engineers SE 2050 for structural embodied carbon, showing the relative magnitudes and reductions through 2050.
Steel
The age of modern steel introduced the skyscraper, built with slender structural beams and unprecedented cantilevers. Steel is highly recyclable, a great circular economy material in buildings despite a wide variety of alloys. Even in timber structures, steel connectors are often critical for joining structural members; steel reinforcing bar is part of all modern concrete structures as well.
Steel’s embodied carbon comes primarily from converting raw iron into steel, and the two major methods of producing steel have a significant effect on resulting embodied carbon. A blast furnace within an integrated mill uses a high content of virgin material and produces first generation steel that is often higher quality, but it requires extensive use of carbon emitting fuel sources to reach the high temperatures required. Electric arc furnaces operate at lower temperatures, and primarily utilize high recycled content inputs, removing substantial carbon impacts associated with the mining of raw iron. Since Electric Arc Furnaces use electricity, as the grid trends toward more renewable energy, high recycled content steel gets close to being a zero-carbon material. Since building stock is expected to double by 2060, however, there is not enough scrap for all new construction so some new steel needs to be produced.
Data on steel is becoming widely available in Environmental Product Declarations (EPDs), but some caveats need to be mentioned. In most EPDs:
- A1 includes raw material extraction or recycled content through the steel mill production
- A2 includes transportation to the fabrication shop
- A3 includes work at the fabrication shop (but excludes coatings). EPDs often include an industry average for A3 and, for certain custom shapes, this will underreport embodied carbon. Some EPDs exclude fabrication, making comparisons more challenging.
- A4 and A5 are typically excluded from the EPDs: A4 is straightforward (transportation to site), but A5 installation includes on-site welding (tied to local electricity carbon intensity) and very little data exists on energy use and carbon emissions.
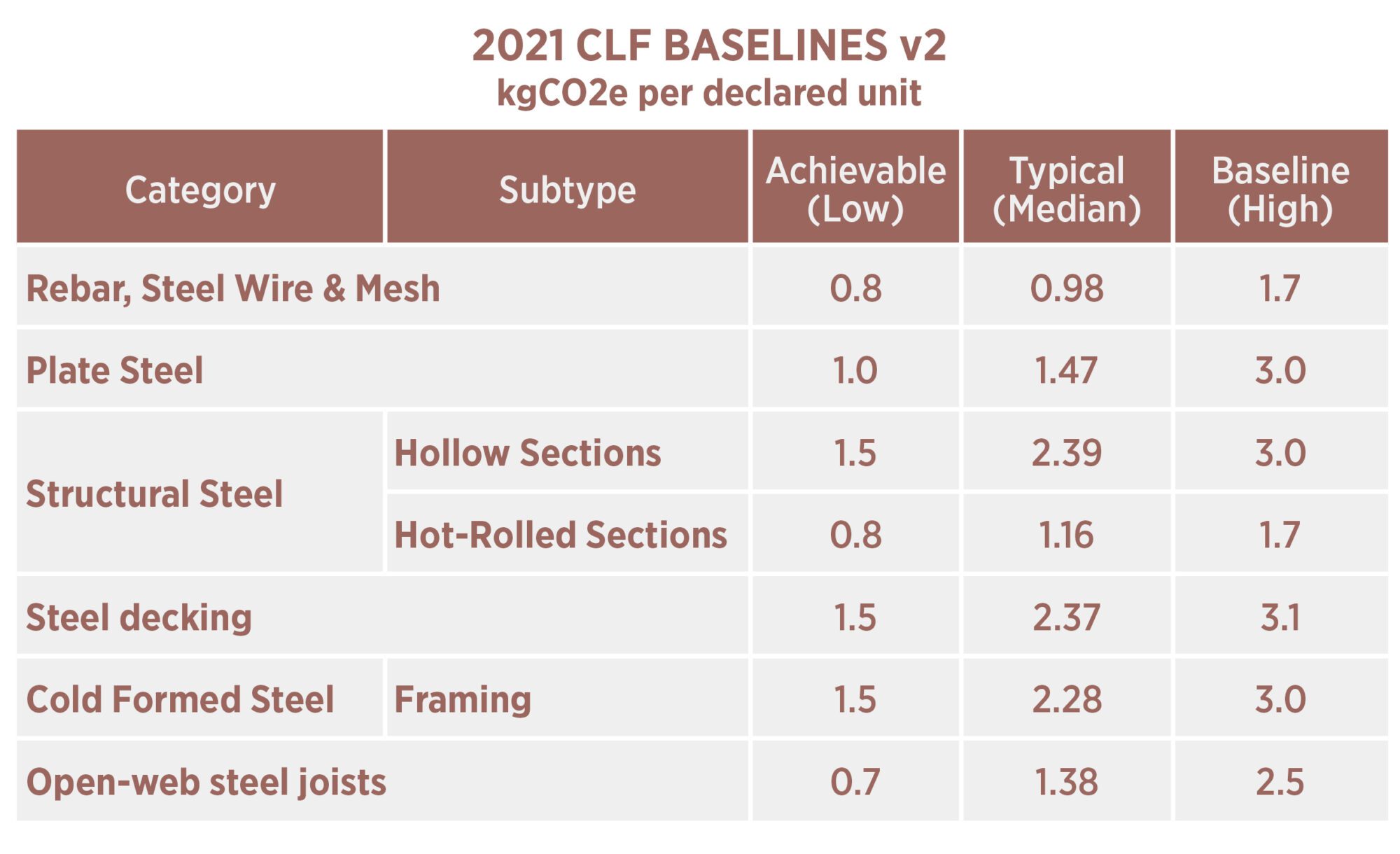
Steel embodied carbon baselines from the CLF 2021 Baselines, including modules A1-A3.
Steel Strategies:
- Reduce the weight of the building. Cantilevers and column transfers can significantly increase the total weight of steel required (and add to foundation concrete embodied carbon as well). Castellated beams, asymmetrical beams, and trusses can reduce total steel weight while carrying the same loads.
- Minimize site fabrication and on-site welding.
- Using higher strength steel (65 ksi or more) may reduce total embodied carbon by reducing total steel weight when strength (not stiffness) sets performance requirements.
- Use procurement weight for estimating embodied carbon for steel; this is often around 10% higher than the steel weight within a building model.
- Require EPDs from steel manufacturers.
- Procure low-carbon steel. Establishing a cost of carbon with each client ahead of time allows emissions (submitted as EPDs) to be compared at procurement time. Applying a carbon price can then be used to level bids toward meeting low-carbon goals. Newer technology is lowering the embodied carbon of steel.
- Specify that relevant steel products comply with Buy Clean California’s maximum GWP limits or CLF’s baseline or typical GWP limits (chart).
- Steel fireproofing has a noticeable impact, lower-carbon options are available and should be considered.
- Other strategies are in Architecture 2030’s Materials Palette.
Concrete
Concrete is one of the most useful, durable construction materials on the planet. When water is mixed with Portland cement and aggregates, a chemical reaction occurs (hydration) that binds the mix together to form concrete. The proportions of Portland cement, water, aggregates, and any admixtures determines the strength, cure time, workability, and other concrete properties.
The creation of Portland cement itself results in around 8% of global carbon emissions. Roughly half of the emissions from Portland cement are from energy use (heating to 1,450°C) and the other half from the chemical reaction that creates it (CaCO3 converted to CaO and CO2), resulting in 8 or 9 tons of COCO2 for every ton of cement.
Cement is responsible for 80-90% of the emissions from concrete. For this reason, improving the embodied carbon of concrete starts with reducing the amount of Portland cement, often using supplementary cementitious materials (SCMs) that have similar properties. Fly ash (a byproduct from burning coal), blast furnace slag (from virgin steel production), and other pozzolans (such as ground glass) can be substituted for a significant amount of cement. Some SCMs are less expensive than cement, resulting in cost-neutral embodied carbon reductions. The free, online EC3 tool has thousands of concrete mix EPDs in the database to help compare mixes, suppliers, and regional impacts.
Concrete strategies:
- Design to reduce building weight. This strategy is effective for all structure types since concrete foundations support most buildings. Reducing column transfers and utilizing lighter and more efficient structural systems, like post-tensioned slabs. Instead of thickening slabs for transfers, using a ribbed or waffle slab can also be effective.
- Allow Type 1L cement (incorporates more raw limestone to replace cement clinker) and consider emerging cements like limestone calcined clay cement.
- Consider different aggregates that allow for better mix consistency and performance, which requires less cement (as long as transportation carbon is also considered). Since hydration is a chemical reaction, nuances in aggregates can require more or less cement to be used.
- Maximize use of supplementary cementitious materials (fly ash, slag, pozzolans) and carbon sequestering additives like CarbonCure or Zeolite.
- Use performance based concrete specifications instead of prescriptive – instead of specifying a minimum cement content for each mix, specify the performance parameters such as strength and shrinkage, and allow the concrete suppliers to build mixes to meet performance criteria with lower carbon mixes.
- Set total global warming potential (GWP) targets for concrete mixes by strength lower than the National Ready-Mix Concrete Association 2022 baselines , Carbon Leadership Forum baseline or typical GWP limits.
- Don’t limit SCM content beyond code requirements. The concrete building code, ACI318, only limits the quantity of SCMs for concrete exposed to de-icing chemicals.
- Other strategies in the Rocky Mountain Institute’s Concrete Solutions Guide and Architecture 2030’s Materials Palette.
Design-phase discussions between architect, structural engineer, contractor, and potential concrete suppliers are essential to establish project goals. Type 1L cement is increasingly standard in many states, the importation of better aggregates is common in some areas while the availability of SCMs varies. In some locations innovative technologies are available or in development to reduce the embodied carbon of concrete: CarbonCure, Carbicrete, Solidia, Fortera, Brimstone, Bubbledeck, limestone calcined clay cement, and others. Beware of marketing claims – use verified EPDs to assist in determining actual GWP reductions from innovative products.
LMN has found that we can reach 30% below the National Ready Mix Concrete Association baselines (2019) on nearly all projects across the US, reaching better reductions on many. This is accomplished by reviewing all mix types and the reasonable upper limit of SCMs for each mix. Many SCMs increase concrete workability, but can take longer to come up to strength, and at higher levels can be more difficult to finish. For mat slabs, shear walls, some floors, and other elements that will not need full strength at 28 days, allowing a longer cure time increases the potential upper limit of SCM use and the final strength of the concrete.
Reinforcing bar (rebar) is also a noticeable portion of concrete embodied carbon. For our models we often ask the structural engineer for the rebar weight per volume of concrete, since they can estimate that fairly early in design.
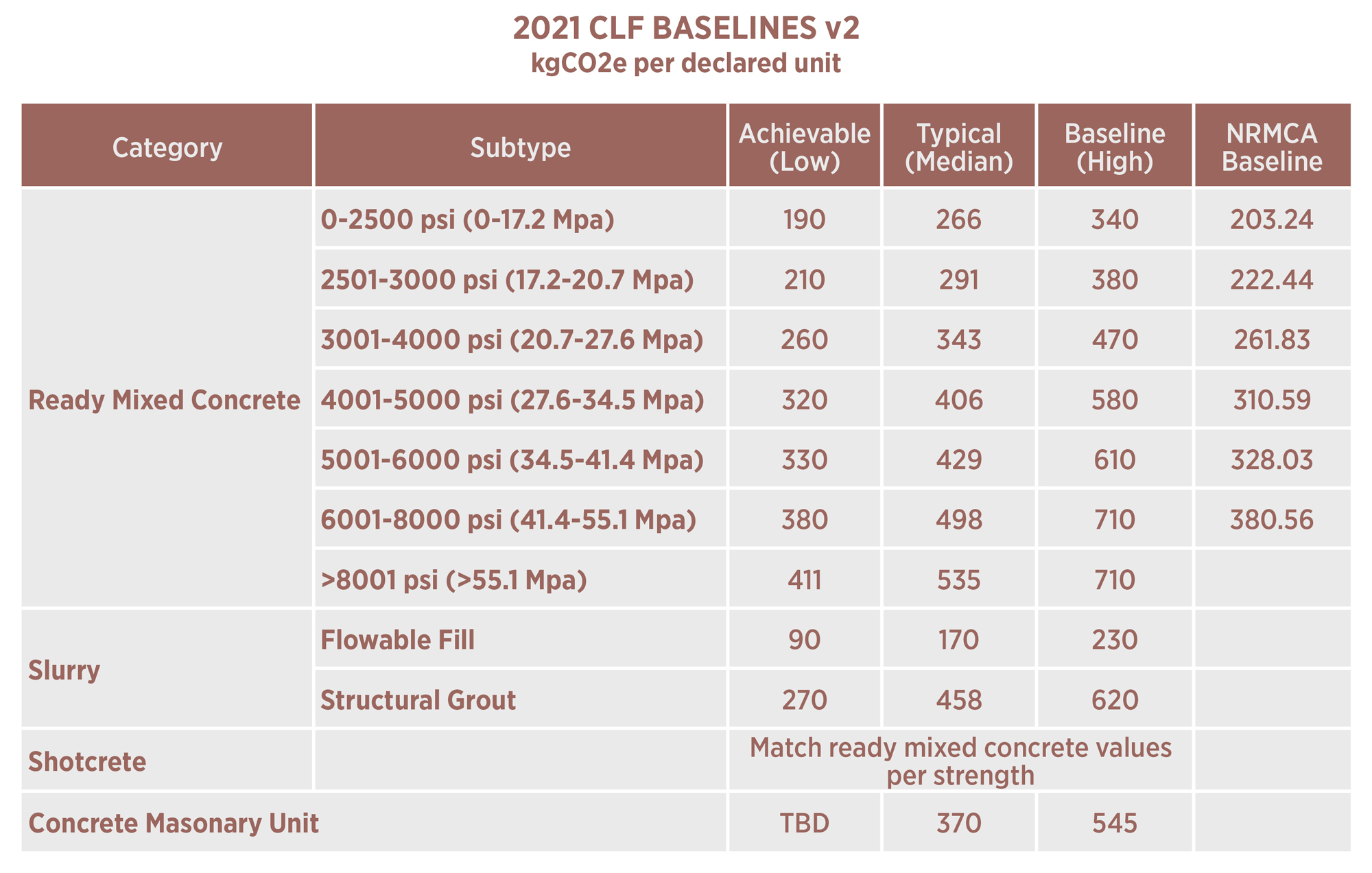
The Carbon Leadership Forum established 2021 CLF Baselines for concrete mixes. The National Ready Mix Concrete Association (NRMCA) also published a benchmark report and EPDs here.
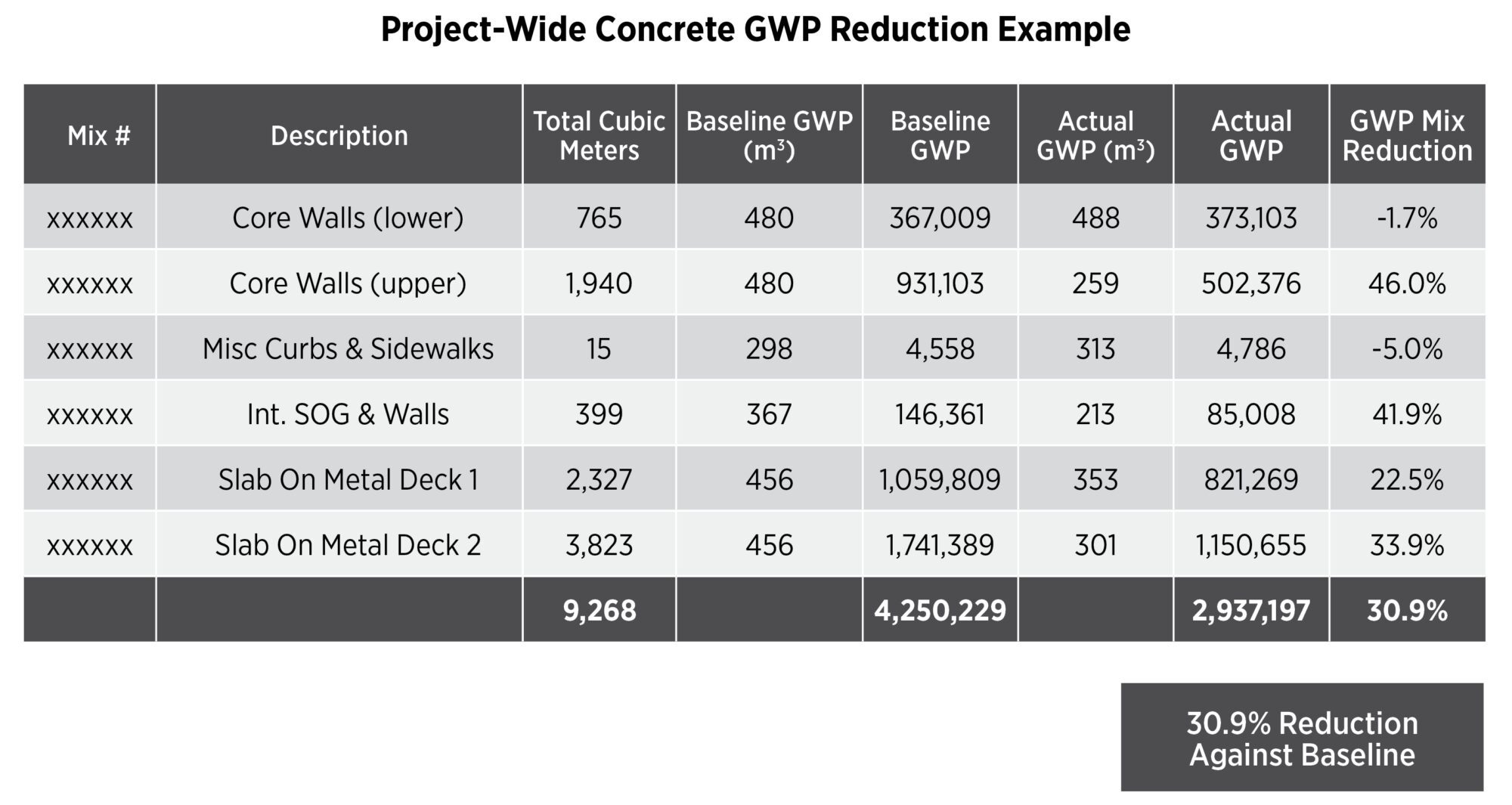
Setting a project-wide concrete Global Warming Potential (GWP) maximum is an effective tool to control total emissions. This project, for example, included a minimum 30% GWP reduction from the National Ready Mix Concrete Association (NRMCA) 2019 regional baseline. This form shows how the concrete supplier calculated the reduction across multiple mixes, optimizing for cost and other project requirements.
Note that many supplementary cementitious materials (SCMs) are waste products from coal burning and iron production. As we reduce coal burning for electricity (Post 06) and virgin iron production as part of the Circular economy (Post 09), we will need to find others. Research is ongoing into alternatives, including alternative cement production and new SCMS like recycled ground glass pozzolans.
Wood / Mass Timber
Wood is a beautiful, biophilic material and is often used in buildings for those reasons. It also naturally removes carbon dioxide from the atmosphere as it grows and stores it as carbon within wood fibers and soil.
Many smaller buildings and most residential structures use wood studs and trusses, made of small members like 2x4s and 2x6s. These smaller members can be laminated together to create mass timber structure, which allow the aesthetics and carbon sequestration of wood to be used as a structural system for large buildings. Since mass timber is built up of small lumber members, it provides a market for small-diameter trees from tree farms and forest thinning to prevent wildfires.
Mass timber is now allowed as the structural material for buildings up to 18 stories or 270’ tall in the 2021 International Building Code, so nearly all new buildings have the potential to be timber buildings. While there is not enough timber in US forests to build every building out of wood, storing significant amounts of forest-sequestered carbon in building is an important strategy towards a built environment carbon neutrality.
Wood structures were discouraged in building codes after great fires destroyed many cities around the beginning of the 20th century, but modern testing indicates they can meet life safety requirements. Mass timber members are sized to provide a sacrificial char layer on the outside that may burn in a fire, but protects the structural portion of the timber beneath it. With modern sprinkler systems required in tall buildings, it’s unlikely the entire char layer will ever be needed.
Vertical mass timber structure is primarily glulams, while floors and roofs (and sometimes exterior wall panels) are primarily Cross Laminated Timber (CLT) or Dowel-Laminated Timber (DLT), but other products such as Nail-Laminated Timber (NLT), Glue-laminated Timber (Glulam), and Mass Plywood Panels (MPP) are also used.
Mass timber structure can be designed in many ways, including hybrid structures(that combine timber with concrete or steel) to get the best out of each material while reducing and storing embodied carbon. Currently most mass timber buildings include steel or concrete cores for earthquake and wind lateral support and many mass timber floors also use a concrete topping slab to provide leveling and acoustic deadening for the space below.
Costing mass timber is also more complicated: timber columns and ceilings are often exposed, providing more volume and apparent height within each space compared to buildings with dropped ceilings to hide ductwork and other services. This can reduce the number of additional finishes a project needs (reducing embodied carbon in the process), but also requires designers to be cognizant of ductwork, plumbing, and electrical runs that are now visible. Most mass timber buildings also have different optimal column spacing and spans compared to steel and concrete, which requires early consideration by design teams. Thankfully, bay sizing tools can aid in initial design decisions.
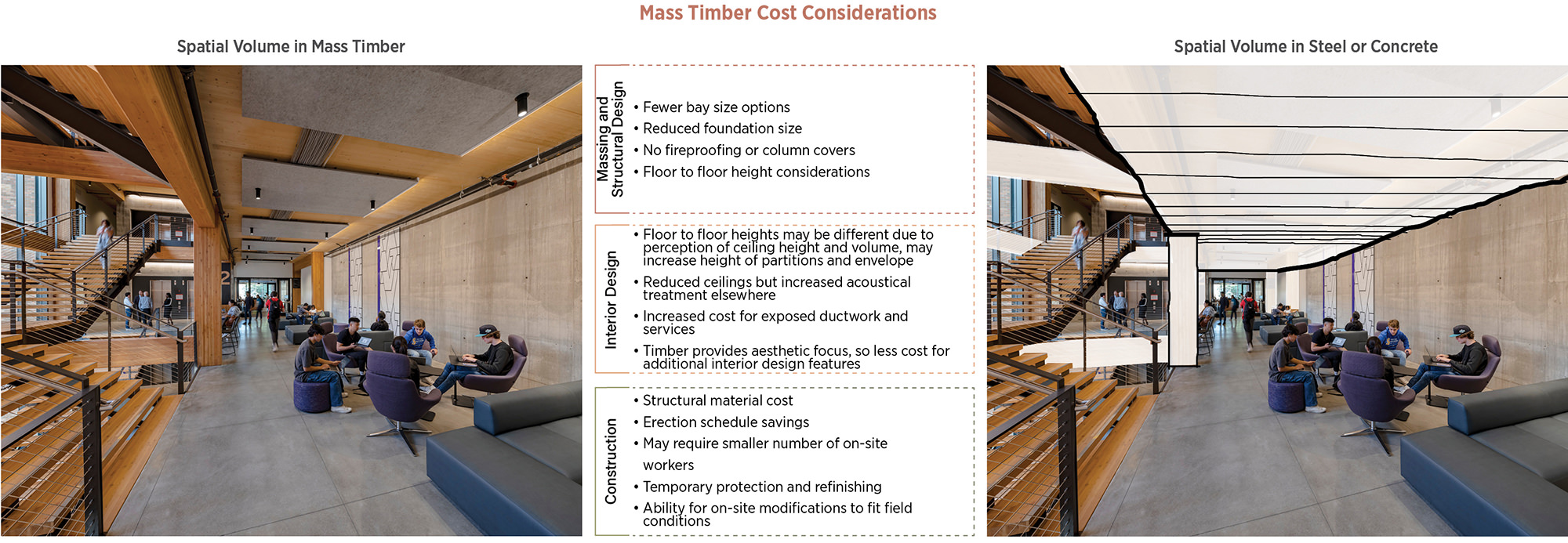
Comparing mass timber costs to steel and concrete structure is complicated, requiring consideration of interior design, mechanical systems, bay sizing and finishes. Comparing floor to floor heights is not straightforward: while most buildings have ceilings below steel and concrete structure and ductwork, mass timber invites an expression where ductwork and structure are exposed, meaning that the apparent height of a space is taller than otherwise would be possible, while beams may be lower than normally acceptable.
Wood’s Carbon Footprint
Trees naturally sequester carbon, and can have lower embodied carbon emissions that steel or concrete structures even without considering carbon sequestration. Globally forests currently store roughly 400 Gigatons of elemental carbon, which corresponds to nearly 1,500 Gigatons of CO2 (CO2 weight 3.7x more than C). Recall that our remaining carbon budget to stay below 1.5C is 340 to 400 Gigatons of CO2. Using some of this carbon stock within buildings while growing more presents an amazing opportunity. However, removing trees also releases some of the carbon from soils, and we don’t have a clear picture yet on these net impacts. While the US grows more timber than is harvested each year, each acre’s health is based on local forestry practice. The diagram below shows the significant carbon stored in soils across the globe; if forestry practice is not careful, harvesting timber can emit much more carbon than it sequesters by releasing below-ground carbon. Modern mapping tools can help, with the goal of having forest-specific data on carbon emitted and sequestered based on forestry practices. The Biomass Carbon Monitor uses satellite data (GEDI is one example) to understand net above-ground stock in forests over time, but below ground carbon flux is still not monitored rigorously.
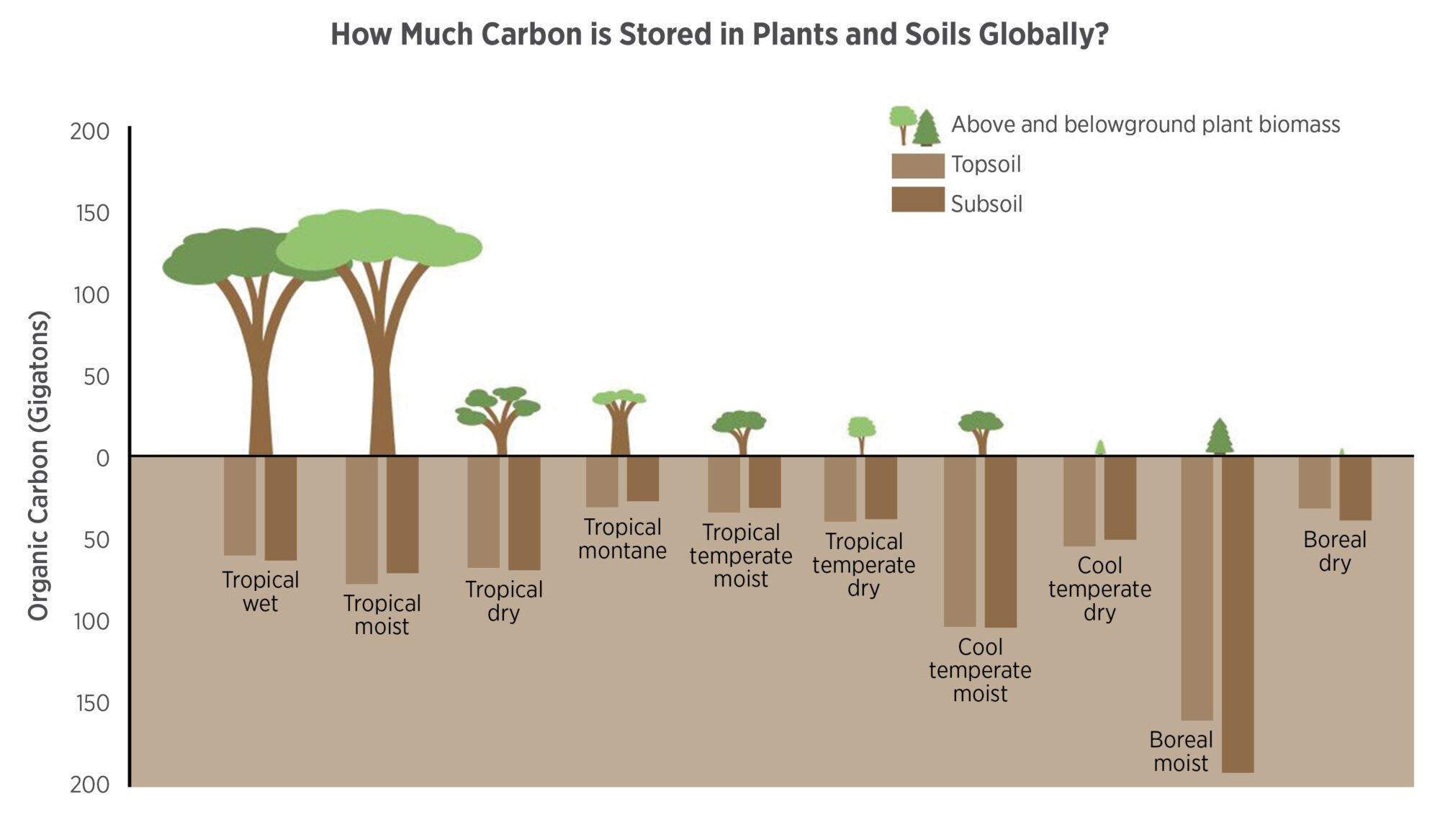
While tropical areas retain most of their carbon stocks above ground, most other regions store more of their carbon within the topsoil and subsoil, especially the Boreal moist zone. This means that harvesting trees can emit much more carbon than is stored in the timber products if soil carbon stocks are disturbed and not maintained. USDA Forest Service
As mentioned in Post 07, understanding the carbon emissions from bio-based materials like wood are less straightforward than other materials like steel or concrete. There are three ways that timber can help with embodied carbon:
- A1-A3 Reduction: Mass timber forestry activities, harvesting, and manufacturing can emit less carbon than comparable steel or concrete buildings, but improper harvesting may result in larger impacts. This will be difficult to show until more forest- and mill-specific wood EPDs become available.
- Carbon storage: Mass timber always stores sequestered carbon in the fibers, which can be included in the A1 module. While carbon storage varies by species, 1 ton of mass timber product has sequestered 1.84 tons of carbon dioxide when the dried carbon weight is around 50% of the product as discussed in Post 08. Per ISO 21930, biogenic carbon must sum to zero in cradle to gate LCA, but LMN’s viewpoint is that if the structure is designed to remaining 100 years or longer, it provides carbon storage service; the Moura Costa method provides one way to account for long term but impermanent carbon storage.
- Forest carbon: carbon sequestration occurs in forests, beyond the harvested tree. Soil, roots, and other plants store carbon. They can be significantly impacted by forest management. EPD accounting omits the forest carbon flux, so the Upstream Tool helps create an A0 module to understand the impacts of procuring from different forests. More research and data is needed to understand how this A0 module can inform decision-making when comparing wood structure to other materials and comparing forest practices.
In order to realize carbon sequestration at scale, our industry will need to demand wood for sustainably managed forests and take care not to use illegally cut wood or forced/coerced labor; Buildings As a Carbon Sink and an important rebuttal discuss the supply issues.
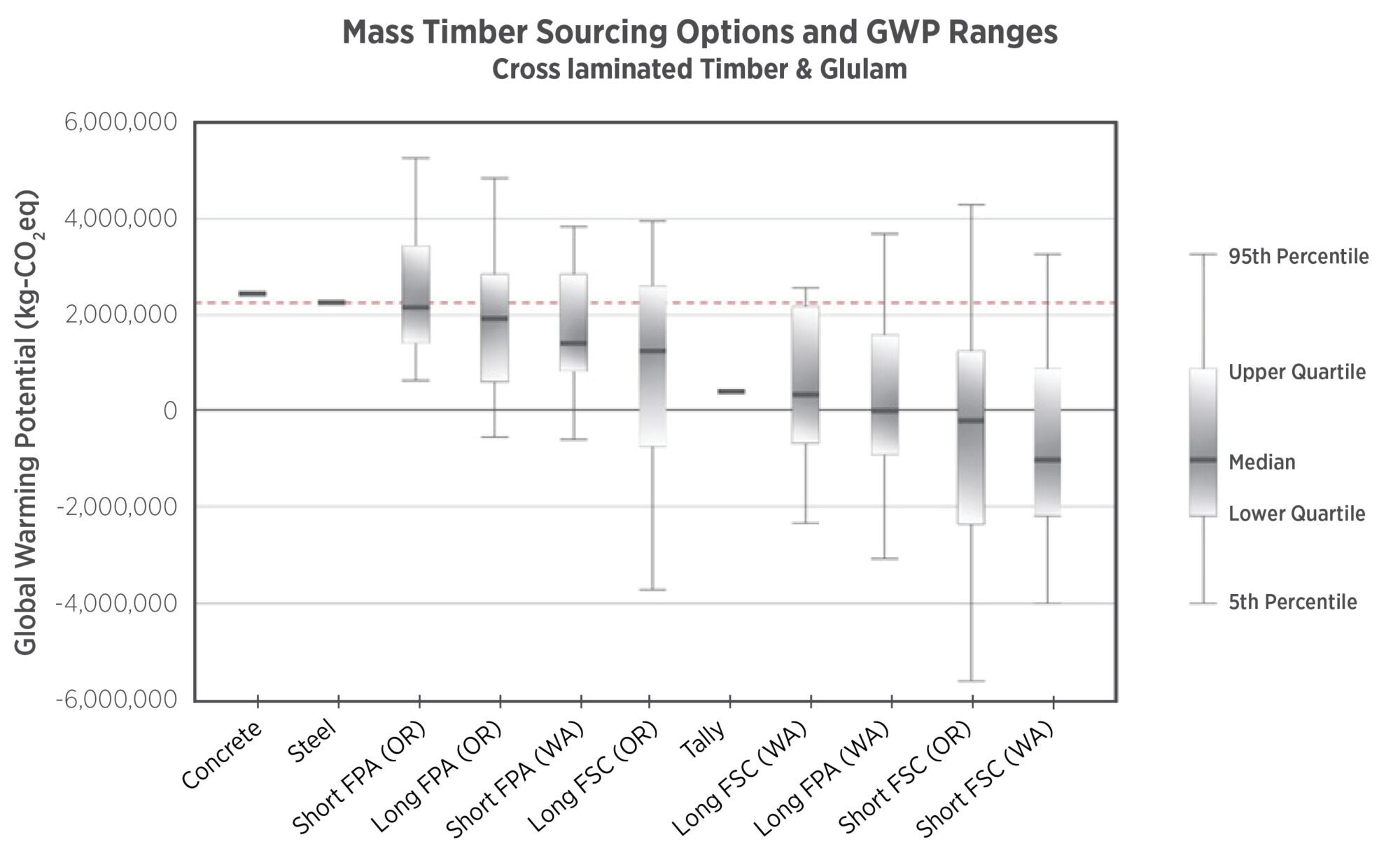
An estimation of the effect of forestry practices on the embodied carbon of forest products in Oregon and Washington. FSC = Forest Stewardship Council, FPA = Forest Practices Act, Short refers to short-cycle harvesting, maximizing net present value of timber (roughly 40 year rotation), Long refers to long-cycle harvesting (Long-FSC is roughly 75 year rotation with thinning).
Conclusions/Remaining Questions
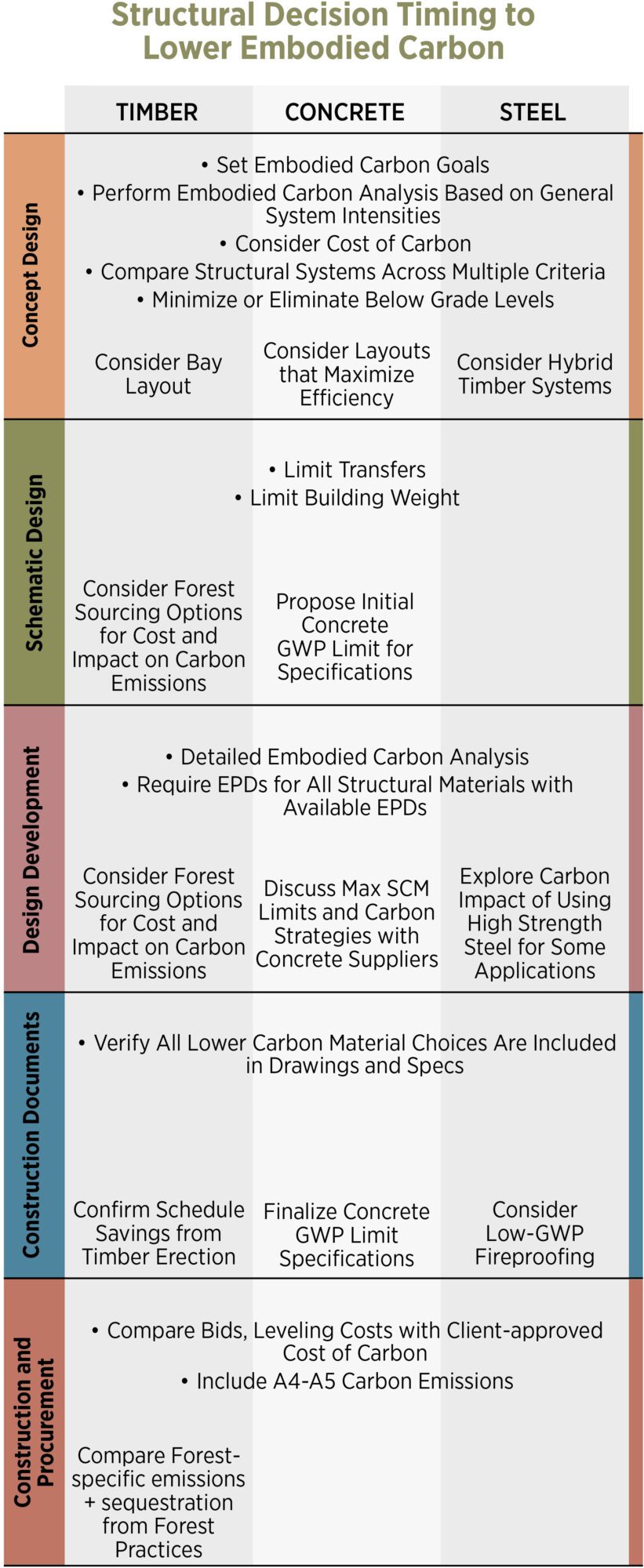
Embodied carbon decisions in structural materials occur throughout the life of a project, with different opportunities occurring at each phase. Any of these can be considered earlier to reduce embodied carbon and risk.
Structural design is one of the important and straightforward ways to reduce the carbon emissions of new buildings, with decision points occurring from early system selection through procurement. Wood can remove carbon emissions from the atmosphere, sometimes resulting in a carbon-negative structural system, and comes with aesthetic benefits as well. Research into steel and concrete show promise for drastically reducing impacts over the next decade or two; they are part of nearly all wood-structured buildings.
Thanks to our external collaborators and peer reviewers
Erica Weeks, Hastings; Jacob Dunn, ZGF; Laura Lindeman, CPL; Dave Walsh, Dave Walsh Consulting; Shana Kelly, KPFF Consulting Engineers; Don Davies, MKA; Catherine Cai, MKA; Isabella Stahl, MKA
LMN Architects Team
Huma Timurbanga, Justin Schwartzhoff, Jenn Chen, Chris Savage, Kjell Anderson, Jeremy Schoenfeld
Posted: 02/08/2023
The text, images and graphics published here should be credited to LMN Architects unless stated otherwise. Permission to distribute, remix, adapt, and build upon the material in any medium or format for noncommercial purposes is granted as long as attribution is given to LMN Architects.