#pathtozerocarbon, #sustainability
10 – Existing Building Reuse
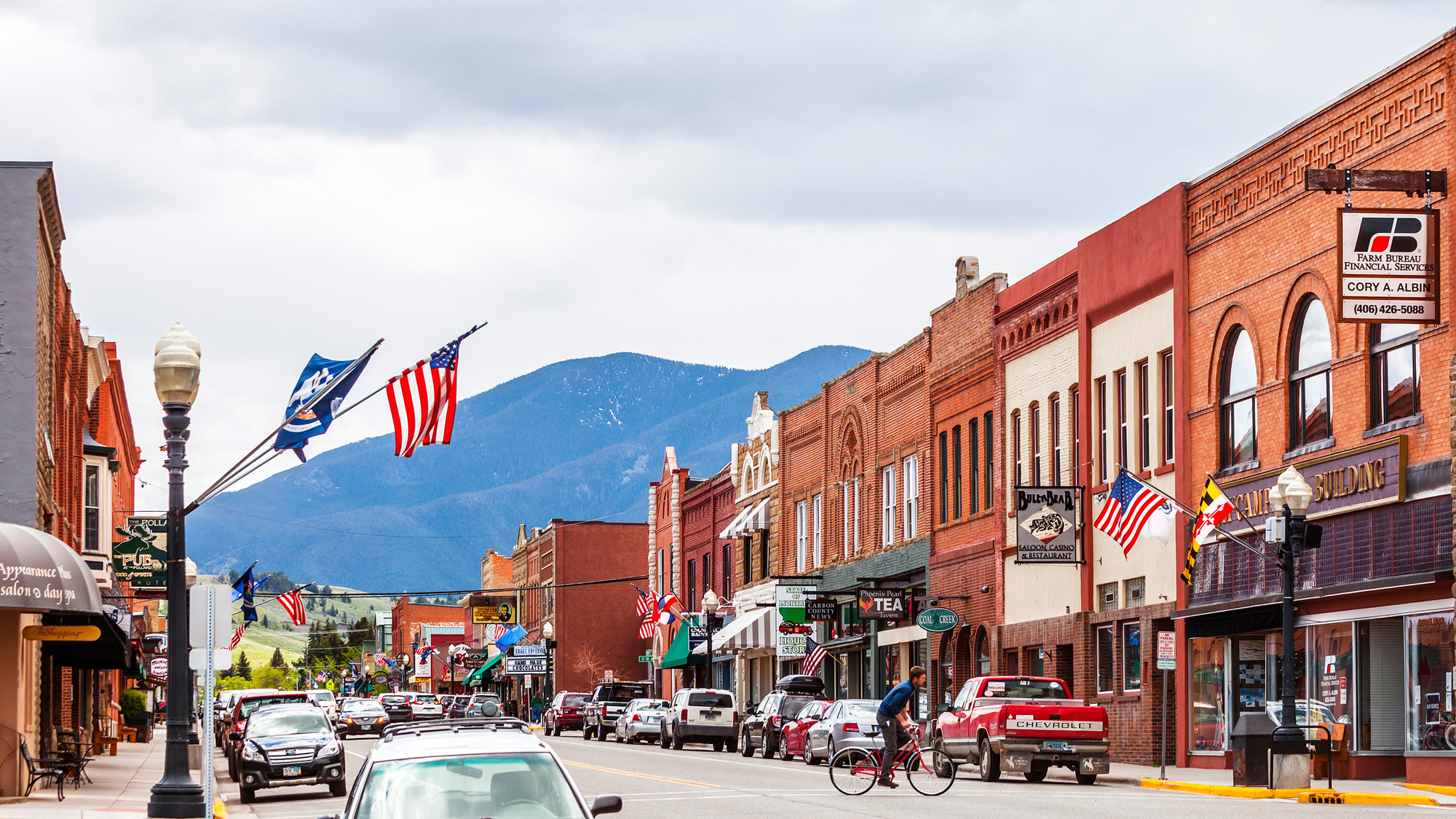
86% of US Commercial Building Stock and nearly all residential buildings are less than 25,000 sf. Deeply decarbonizing these buildings while retaining their embodied carbon will require significant effort across the buildings industry.
Decarbonizing existing buildings is the paramount climate challenge of architects this century: building operational energy use is responsible for over 25% of human-caused global carbon pollution. Addressing this challenge includes determining the most carbon smart decision: to rebuild or renovate for deep decarbonization? New buildings require a significant embodied carbon investment but are increasingly all-electric and operationally low-carbon. Reusing existing buildings can substantially reduce embodied carbon, but creativity is required to cost-effectively decarbonize operational energy use.
This is a continuation of the Circular Economy + Products from the last post, now focusing on the buildings scale.
To Rebuild or Renovate?
The decision to demolish and rebuild or renovate an existing building is a complicated undertaking, based on the intersection of finances, policy, location, economic context, zoning height and floor area allowances, historic designations, multiple competing incentives, potential tenants, existing floor to floor height, deferred maintenance, building codes, compliance with ADA, hurricane and seismic risk and rules, local displacement and disruption, climate change adaptation and resilience, flood plain mapping, and much more. It is this complexity that makes renovations so challenging, demanding creativity and flexibility.
Several resources have been created to help think through renovations: the AIA Deep Energy Retrofit RFP Guide, existing building framework, existing building decarbonization policies, US Existing Buildings Resources, and a Decarbonization Guide with sections on existing buildings.
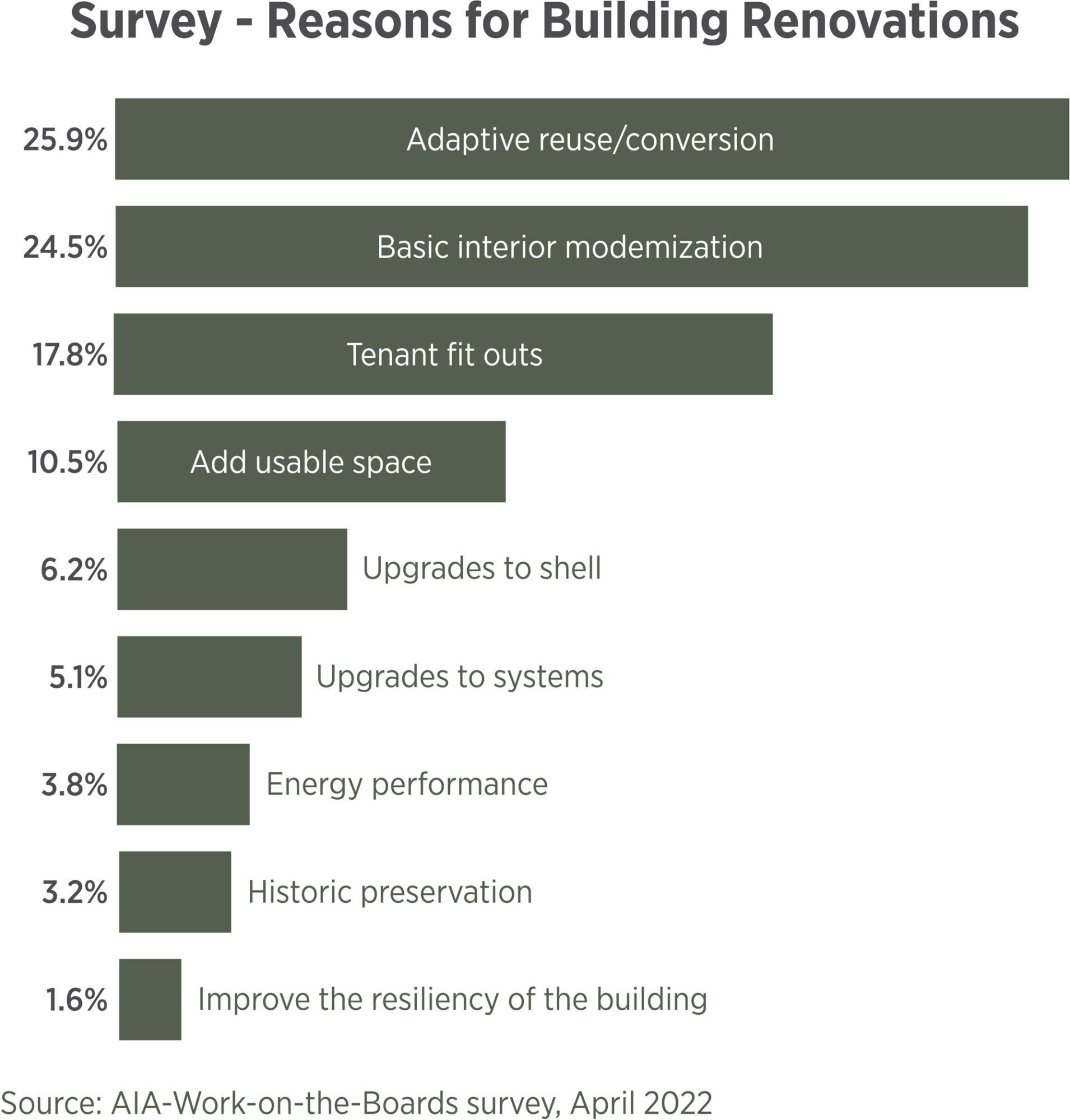
AIA Work-on-the-Boards survey, April 2022 shows the primary reason for each reconstruction project. While only 3.8% are primarily for energy performance, most upgrades improve energy performance. Image credit: AIA
These resources support a longer term trend, as billings for renovations now eclipse those for new construction. Successful examples abound: thoughtful major renovations make up more than a quarter of the AIA COTE Top 10 winners from 2018-2022. This includes Lick-Wilmerding High School, 663 South Cooper, ASU Hayden Library, Market One, Ford Foundation Center, Keller Center, Upcycle, Etsy Headquarters, Daniels Building, St Patrick’s Cathedral, Ortlieb’s Bottling House, Smithsonian’s Renwick Gallery, and the San Francisco Art Institute. Several taller buildings like the Empire State Building, others in New York, the Quay Quarter Tower, and the Edith Green Wendell Wyatt have undergone major energy retrofits as well.
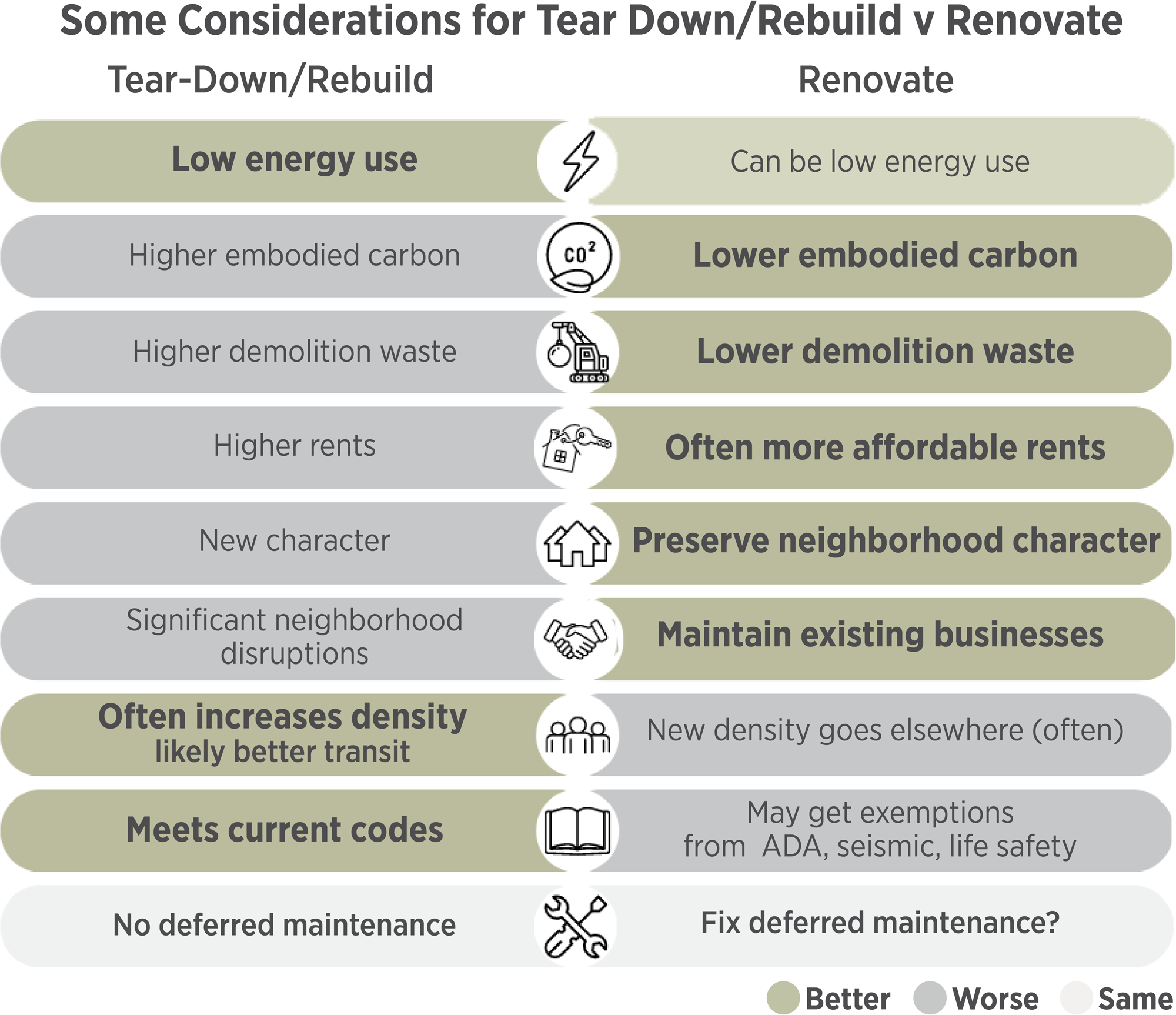
While each project is unique, some generalizations about major pros and cons of building renovations. While renovating to net-zero energy has been done successfully, energy codes and building performance standards (covered later) are typically less stringent for renovations than for new buildings.
Reuse usually has many benefits to society, including much lower total carbon emissions if the building can be energy efficient and electrified, even if it doesn’t fully meet the energy performance of a new building. Many older buildings also have character that add value to a neighborhood, often including smaller storefronts that support local businesses that may not survive displacement during demolition and deconstruction of a new building. Since initial construction costs have been paid off, older buildings are often more affordable as housing, retail and office as well.
Older buildings also have some resilience and passive survivability benefits: heavier facades that provide thermal mass, operable windows to provide cooling and fresh air without energy use, and a reasonable window to wall ratio that limit heating and cooling energy. Older buildings, however, may also be more vulnerable to life safety and seismic risks since they were built under outdated codes.
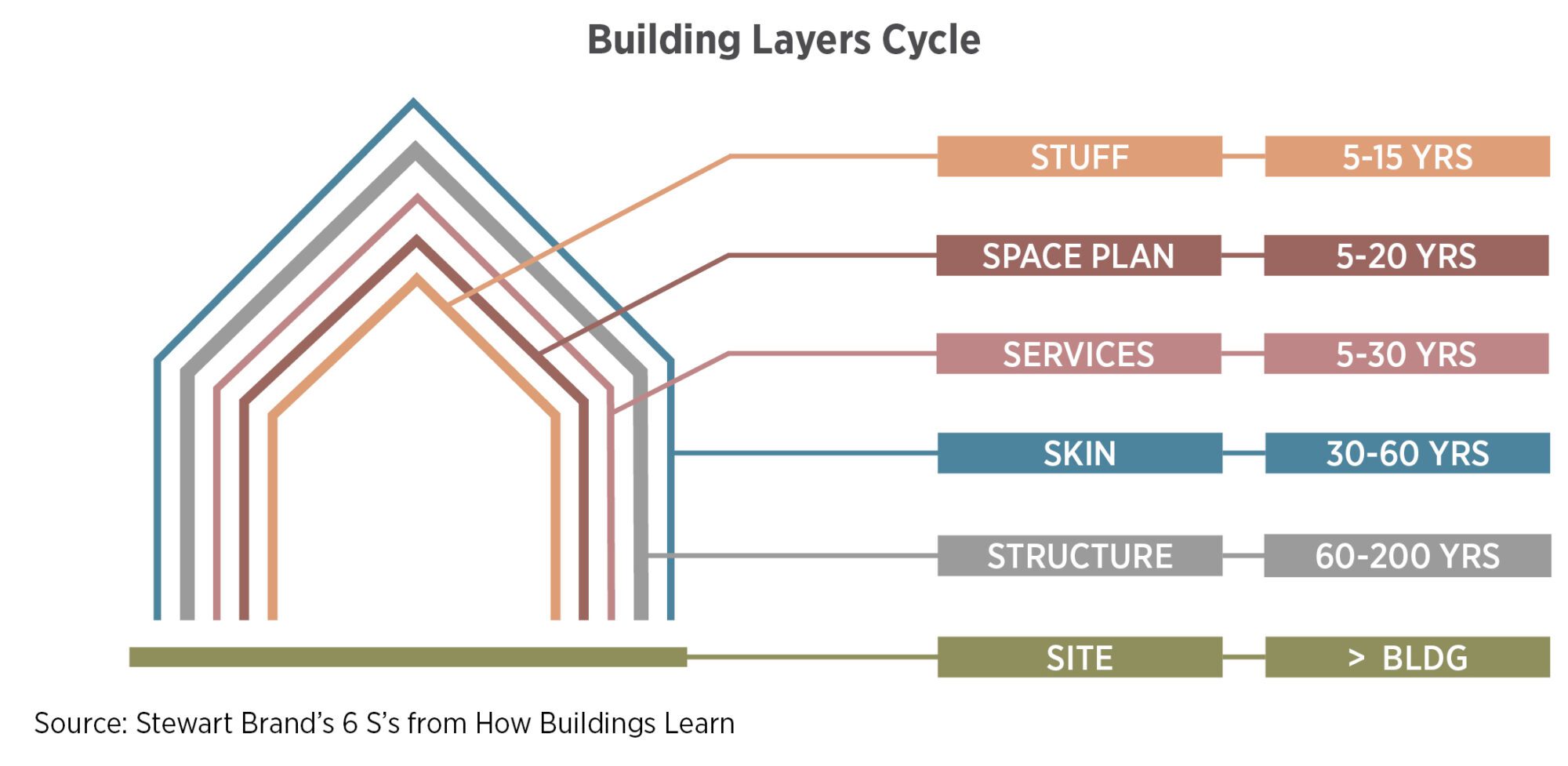
Stewart Brand’s diagram in How Buildings Learn (with added the replacement cycles) for the many layers of a building, showing that a variety of nuanced renovations can extend the life of a building.
Lastly, decisions are often not as binary as ‘rebuild or reuse.’ Stewart Brand’s insightful diagram from How Buildings Learn shows many layers of a building that have differing timeframes for renovation. Each of these layers can independently be considered for deconstruction or extending useful life. Since structure contains a large fraction of a building’s total embodied carbon, retaining only structure instead of demolishing an entire building can be a carbon-smart decision.
Comparing the Carbon Impact of Rebuild v Reuse
With the immediacy of embodied carbon emissions and time-critical nature of climate change action, the carbon benefit of building reuse has a unique answer for each project. Compounding this, we don’t yet have good data on the embodied carbon of some systems (MEP systems, equipment, and furniture especially) but we have enough information to make directional estimates to inform decision-making. Some purpose-built tools can help inform these early decisions.
CARE (Carbon Avoided, Retrofit Estimator) is a free, online early estimator for carbon emissions, comparing a baseline building to a new building, with several generalized options for the percentage of original structure and other systems that are preserved. It takes perhaps 5 minutes to set up a model and then allows many iterations to understand outcomes.
EPIC (Early Phase Integrated Carbon Assessment) is also a free, online tool to compare new building options as well as renovation options. EPIC starts with a base case being a new building necessary for the entire specified program, with conservative assumptions for replacement and specifications. Building reuse can be modeled with various systems maintained, as well as a proportion of each.
EC3 (Embodied Carbon in Construction Calculator) or your favorite embodied carbon calculator, along with energy modeling, can also inform early decisions.
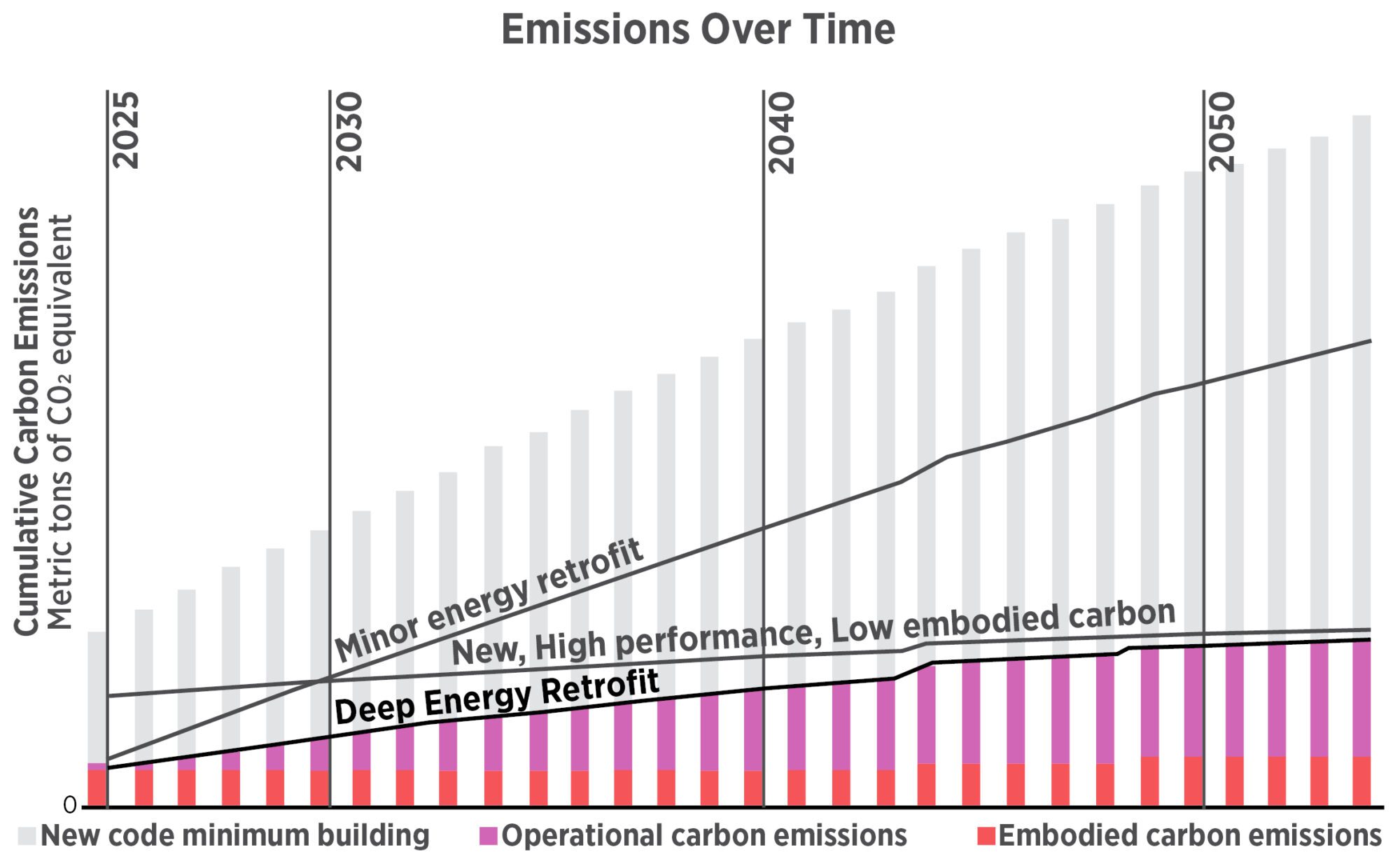
Composite image from EPIC, comparing a baseline new building scenario against a new high performance, low carbon building and an existing building with minor or major energy upgrades.
Unfortunately, it is not very helpful to generalize about the carbon emissions of rebuilding versus reuse – use the tools outlined above! Renovations requires extra creativity and coordination from architects, engineers, contractors, and building owners. An informed decision requires simultaneous design and modeling of operational carbon, embodied carbon, and cost. This is especially true for envelope upgrades since they increase comfort and decrease mechanical sizing a cost, any energy and cost modeling need to be integrated as covered later and in Post 12.
Energy Retrofits Toward Zero Carbon
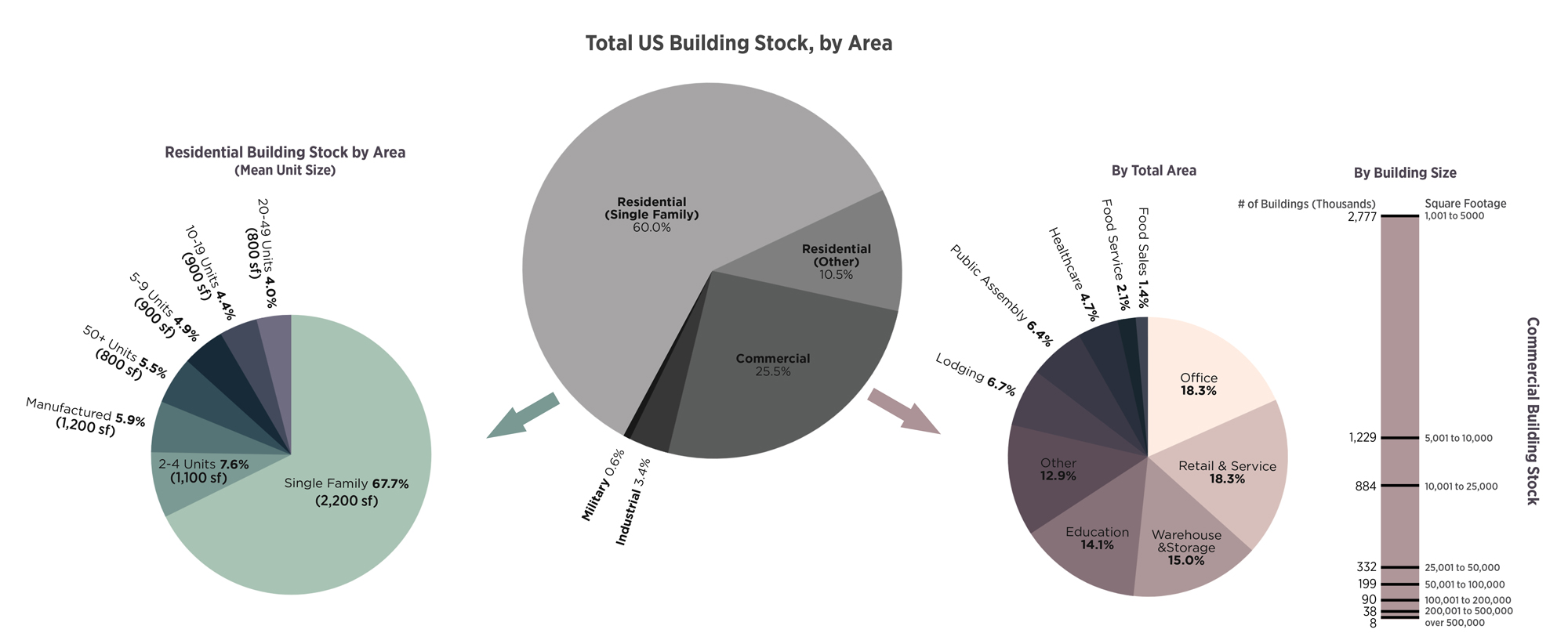
A vast majority of the existing US building stock is single family residential. About a quarter is commercial, which is split among several distinct categories. Decarbonizing all of these building types requires thoughtful practice and policy. Data from multiple sources aggregates by the Construction Physics blog.
Existing building reuse is often the low-carbon option (compared to a new building) when an energy retrofit is applied. While the implementation is complex, existing buildings can be decarbonized with just two general principles:
- Envelope improvements enhance human thermal comfort and reduce the size, cost and embodied carbon of updating mechanical systems. Going to double- or triple-pane windows, adding insulation, and reducing air infiltration can all be cost-effective when they are due to be replaced. Some evidence suggests that envelope improvement embodied carbon is more than offset by reduced mechanical system carbon (of course, with many caveats). More on this in Post 12.
- Use electric heat pumps for heating and cooling, or a small amount of electric resistance. Fossil fuel combustion and electric resistance heating are not efficient enough technologies to meet zero carbon goals (heat pumps are generally at least 3 times more efficient) and the electricity grid is rapidly trending toward 100% renewables (Post 06) within the lifetime of any retrofit. Heat pump systems should use only small quantities of refrigerant, ideally low-global-warming-potential refrigerants in compliance with the Kigali Amendment.
Beyond the two above, making the building electricity grid-friendly (Post 06) and procuring renewable energy (Post 08) are next most important.
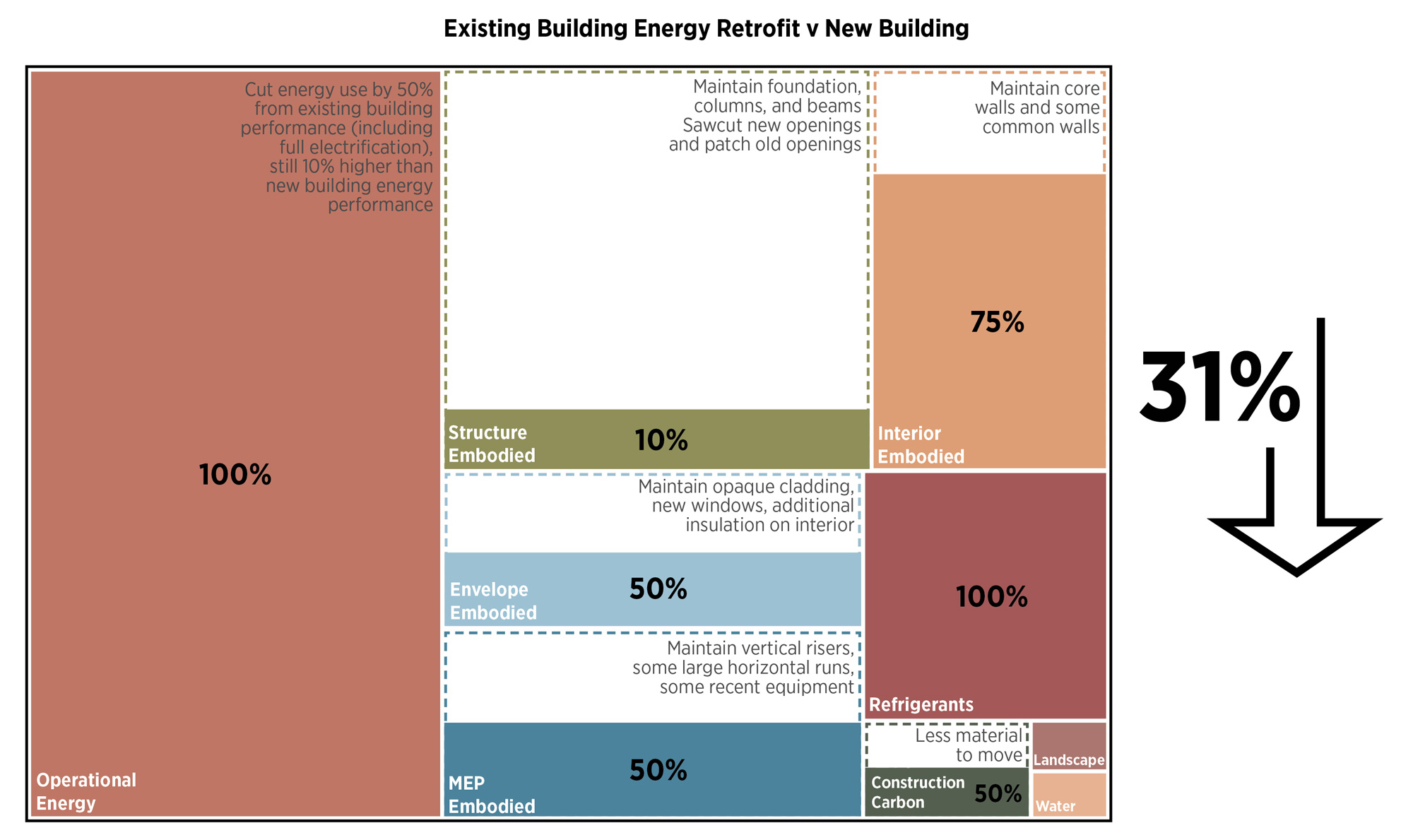
Existing building reuse can significantly reduce carbon emissions compared to a new buildings, but this depends on what is being saved. For a major renovation where structure, cladding, and some MEP infrastructure is maintained, the 60-year carbon savings can be well beyond the 31% shown in this example. Saving just the façade preserves character, but it’s not a carbon-reducing strategy.
Every building is unique when it comes to applying these principles, however, especially when looking for cost-effective solutions that work with the maintenance cycle of a building. The most effective first energy use reduction strategy for most existing buildings is retro-commissioning: onsite verification that all systems work as intended, fixing or upgrading those that don’t.
Electrical Upgrades
Decarbonizing existing buildings can require upgraded electrical service when moving away from gas or modernizing systems. This can be very expensive, and since many appliances are replaced when they fail, there is often no time to design, permit, and complete electrical upgrades to support electrification. However, the market is beginning to see products designed for retrofits to eliminate this cost. In residential construction, water heaters and induction stoves that plug into a typical outlet are now on the market for products that used to require 40 or 50 Amp circuits. Since modern LED lights require much less power than incandescent lighting, in many cases lighting circuits can be combined to free up panel space for other electrification projects like heat pump heating or electrical vehicle charging. Electrical load management systems, perhaps paired with batteries or thermal storage, can be designed to fully electrify a building without requiring an electrical service size upgrade.
Envelope Upgrades
In general, envelope upgrades are major investments that are only financially feasible when capital funding is already allocated for replacing windows or cladding, perhaps when issues appear or at the end of expected service life. If a major renovation is envisioned that replaces a mechanical system, envelope upgrades completed first may reduce the size and cost of the new mechanical system or allow higher performing mechanical systems (like chilled beams) to be used. Unlike new buildings, where high performance wall and window assemblies are required, sometimes the optimized solution includes getting to R-8 walls, double glazing, great airtightness, and a low-carbon mechanical system and advanced controls. Iterative cost and energy modeling can help the design team find the right solutions to meet long-term goals.
Other Considerations
What are renovation implications for the users of the building – can occupants be relocated while work is being completed, or is work needed off-hours? Financing availability, ownership models, the cost of energy and who pays the bills also greatly affect what can be done. The guides listed above include the types of questions design teams should ask.
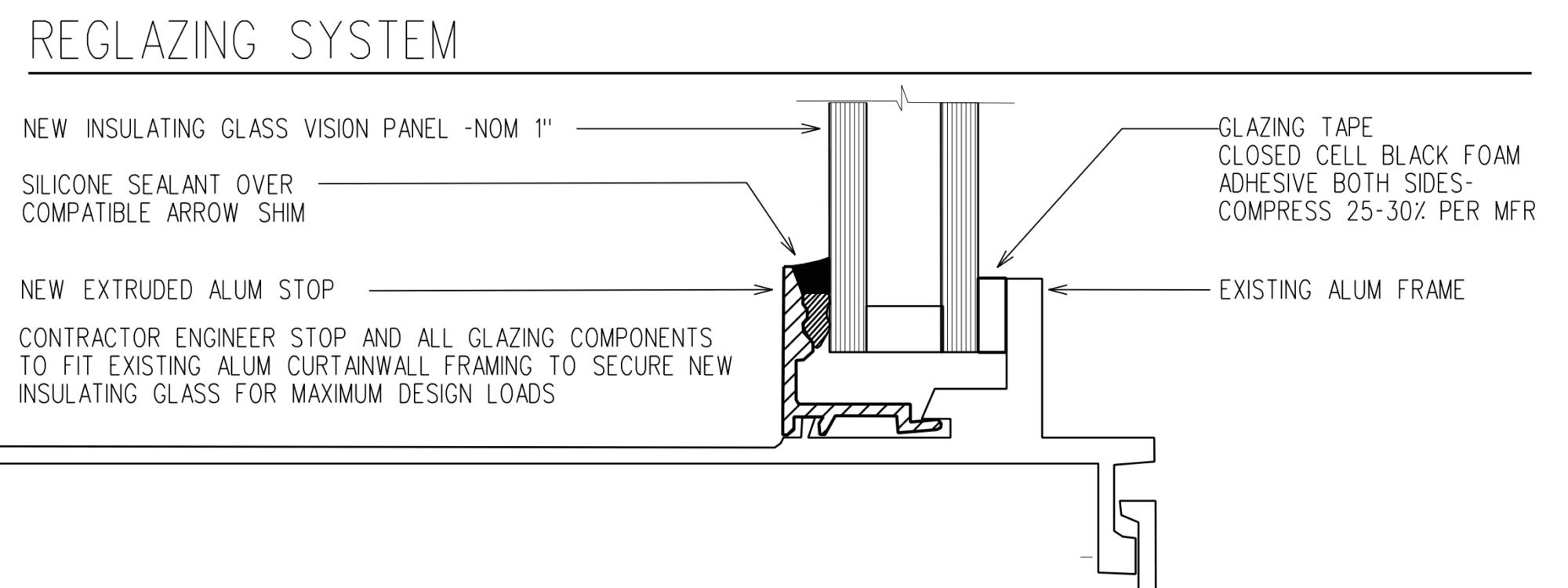
An example of accommodating double glazing within an existing single-glazing mullion system. Retaining the existing mullion by creating a new stop reduced embodied carbon and the cost of the retrofit.
Rethinking Building Reuse Carbon
Life Cycle Analysis practice and most sustainability rating systems currently exclude existing portions of buildings from embodied carbon calculations. This means they report that there is no carbon value in what exists on site and provide no incentive to consider retaining existing buildings from a carbon standpoint. A method is outlined below to include the value of existing structures as well as a value for the remaining service life of a product: for instance, ceiling tiles expected to last 20 years that were installed 5 years ago have 15 years of service life remaining.
With our work on a small but thoughtful renovation, we faced the challenge of quantifying the value of existing materials’ remaining service life. Although a design team inherits these materials, we have agency over their end of life: they can be recycled, landfilled, or reused in some form. This led use to include the end of life for existing materials as described in Post 09 in LCA calculations, similar to conclusions reached in this paper.
Taking this one step farther, LMN believes that the materials in a building have a value for continued service life or reuse, by being retained in place, or salvaged for use elsewhere. This method is supported by some research into LCA methods, though certainly not industry standard yet. The remaining value can be approximated by taking the expected service life of a product, subtracting the age of the product, and then prorating this against the embodied carbon invested in the product through A1-A3 stages. For example, a double-glazed window unit has an expected life of 40 years. After 10 years, 75% of the A1-A3 value remains and could be retained in place or reused off site. (This could be similar to the remaining useful life metric for equipment.)
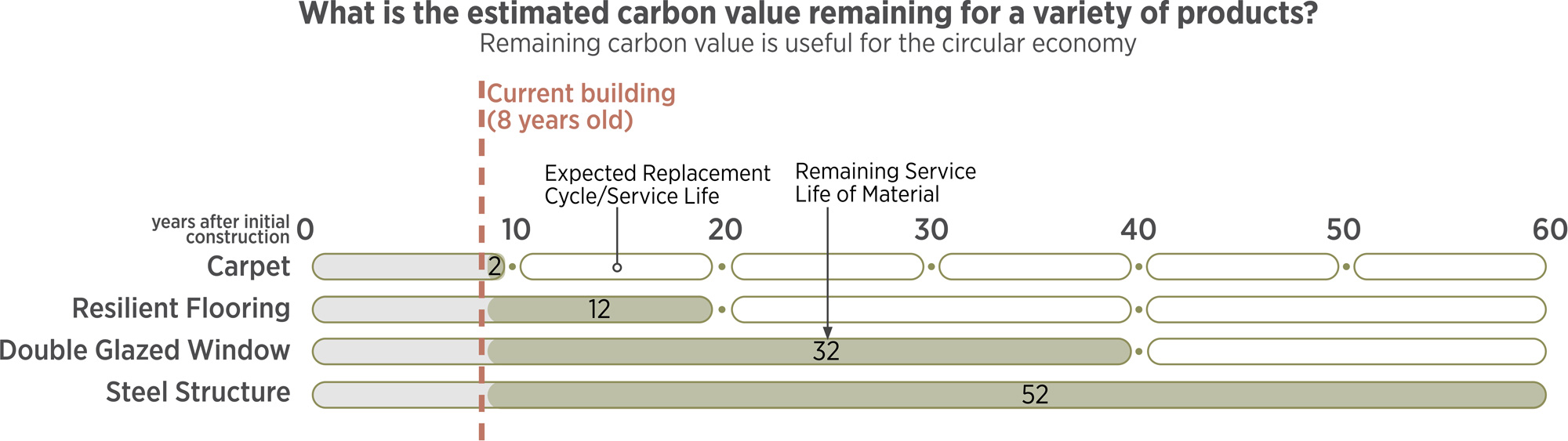
The diagram shows some common materials along with their typical replacement phases within Tally. Carbon analyses typically exclude value remaining in an existing building, products, and materials; we believe this value should be reflected in embodied carbon calculations. The remaining value can be calculated by multiplying the remaining service life fraction by the A1-A3 of each product. While this is a blunt way of estimating remain service life, it indicates some of the potential for each product to be reused – for instance, carpet tile or windows that have significant service life remaining can be reused in a new building as part of the circular economy.
To this end we suggest that a second metric accompanies any embodied carbon reductions: the ratio of carbon value kept in the circular economy divided by the total remaining carbon value in the existing building. This metric conveys the carbon that is kept in the circular economy, whether used on-site of off-site. We believe that this metric should exclude uses that do not contribute to a circular economy and is different from the diversion rate commonly used in Construction and Demolition (C+D) reports. In some cases waste diversion includes alternative daily cover, waste to energy, and downcycling that allows only a second use. Module D within an EPD also sometimes includes carbon benefits that are not part of a circular economy, such as waste to energy. However, we recommend only including materials kept in the circular economy (reused as a product, recycled as a material) or given a long-lasting second use (40 years+).
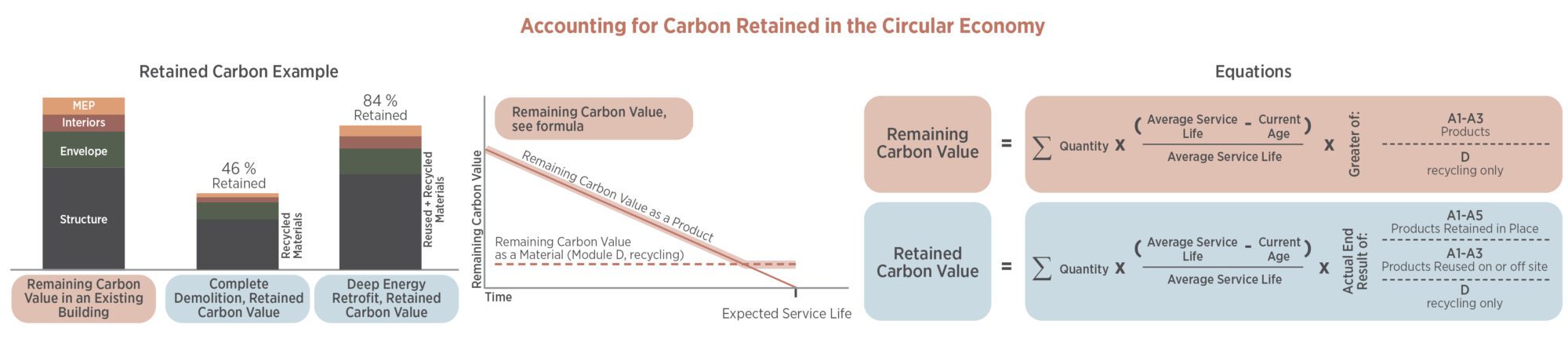
Existing products and materials have value that is not captured in Life Cycle Analysis, but by keeping it within the circular economy these products and materials can displace carbon emissions spent for new products and materials. Along with the modifications proposed in Post 09 to include existing materials in LCA, LMN proposes this second calculation to show the percentage of carbon that is retained within the circular economy. LMN’s view is that non-failing structure does not have a service life.
This aligns with the idea of a building as a material bank – there is useful value in products that have not yet reached the end of their service life. Products with remaining service life have carbon value in displacing the need for a new product on site or elsewhere, and the fate of these products are at least somewhat controlled by design and construction teams. From a carbon perspective, this addresses how reuse, deconstruction and salvage reduces global carbon emissions: each product displaces the need for new extraction and manufacturing embodied carbon for a different project. This also reflects the reality that buildings properly designed for deconstruction contain saleable assets that can be retained or refurbished and reused.
There are No Carbon Smart Policies… Yet
While design teams have agency as the trusted advisor of a building owner about decisions to rebuild or renovate, (as well as how to do so), the decision is sometimes made before the design architect is hired. For this reason, master planning efforts to reuse structures as well as advocacy for public policy and zoning are important in driving carbon savings through building reuse.
A variety of policies exist, including required energy retrofits, low-carbon materials procurement, historic preservation, and some emerging policies. None of these are comprehensive, however. Building energy codes so far are the most impactful building decarbonization policy but they exclude embodied carbon and sometimes disincentivize building reuse. An ideal carbon policy would provide a flexible site carbon budget that includes operational and embodied carbon, a bonus for increasing density that encourages greater mass transit service (to lower transportation emissions) and incentivize building reuse, but this ideal doesn’t yet exist.
New York City, Washington State and other US jurisdictions require existing buildings to meet operational carbon or energy targets, referred to as Building Performance Standards (BPS). A Building Performance Standards coalition was recently formed with 33 jurisdictions to share practices, case studies and promote ideas. Europe has a variety of carbon regulations as well.
Buy Clean policies developed by the Carbon Leadership Forum and others from the Carbon Neutral Cities Alliance target embodied carbon (map here), but do not directly address the question of rebuild or reuse. While not embodied-carbon specific, a variety of policies shown in city-specific studies incentivize building reuse. The American Planning Association also outlines the need for more expansive zoning and building codes for adaptive reuse to be successful. The Climate Heritage Network is a leading international organization that provides policies as well.
Historic Preservation is the primary concept in favor of preserving buildings, although it has not been seen widely as an embodied carbon policy. Preservation is supported by many policies and programs that provide a variety of designations for buildings or places across multiple scales. Designations often make a complete tear-down and rebuild impossible, preserving character, existing fabric, and some measure of embodied carbon. Even when no historic designation or preservation requirements exist, existing buildings may be treated with preservation approaches in response to their historic significance and architectural character.
Preservation policies that restrict or incentive what is done on a given site are an embodied carbon win when they preserve more than just the façade of a building. Designations can also, unfortunately, be used as a cover to restrict additional density, meaning new office, retail, and housing must be built elsewhere. As our cities and towns become denser to promote walkability and reduce auto dependence, the question of whether to rebuild or renovate is also influenced by preservation policies and practices
Another type of policy helps create the Circular Economy (Post 09), since even complete demolition can include carbon-smart practices and deconstruction: salvage and repurposing of materials reduce carbon emissions and drive a local, circular economy. Deconstruction is construction in reverse: dismantling a building for salvage, recycling, and waste management. In some cases, this means the smartest, low-carbon option may be deconstruction and salvage.
Policies are increasingly addressing salvage, since more than 90% of total Construction and Demolition (C+D) debris is from demolition and 30% of C+D waste is from buildings. While much of the total C+D waste is recycled into aggregate because it is overwhelmingly concrete, buildings are constructed with a wide variety of materials; keeping these materials within a circular economy requires deconstruction, salvage, and separation at the job site.
Conclusions and Remaining Questions
Deep decarbonization of existing building stock is central to any built environment climate action, but each one is complicated, most buildings in the US are relatively small, and often there is not a direct, short-term financial payback. A variety of resources highlighted in this post have been created to help design and construction teams wrangle these issues. While preserving existing building stock is a significant embodied carbon win, new tools CARE and EPIC can help with early estimates comparing the embodied an operational carbon of renovations to new buildings.
A variety of policies exist, and many more are planned, to help decarbonize the existing buildings sector, but none yet thoughtfully include embodied and operational carbon.
As we design new buildings, we can give future design and construction teams the ability to reuse or successfully deconstruct, keeping spent carbon within a circular economy. This includes the idea of not overoptimizing program, floor to floor heights, irregular window spacing, and column layouts, since these can detract from future reuse potential. As we renovate spaces, we need to reuse products and recycle materials, allowing time for deconstruction so this can happen.
Accounting for this circular carbon, however, is not part of current practice; we are proposing some modifications to include these missing pieces.
Remaining questions
How best can we include circular economy and building reuse into our carbon accounting, to inform more informed decision-making?
Please email any questions or comments to Kjell Anderson, kanderson@lmnarchitects.com
Thanks to our external collaborators and peer reviewers
Erin Mcdade, Arch 2030; Lori Ferriss, Goody Clancy; Larry Strain, Siegel & Strain; Don Davies, MKA; Kristian Kicinski, Bassetti Architects; Alexandra Ramsden, Brightworks Sustainability; Erica Weeks, Hastings; Kristen Fritsch, Elkus Manfredi Architects; Jay Hindmarsh, Miller Hull
LMN Architects Team
Huma Timurbanga, Justin Schwartzhoff, Jenn Chen, Chris Savage, Kjell Anderson
Posted: 01/26/2023
Edited: 10/11/2023
The text, images and graphics published here should be credited to LMN Architects unless stated otherwise. Permission to distribute, remix, adapt, and build upon the material in any medium or format for noncommercial purposes is granted as long as attribution is given to LMN Architects.