#pathtozerocarbon, #sustainability
09 – Circular Economy + Products
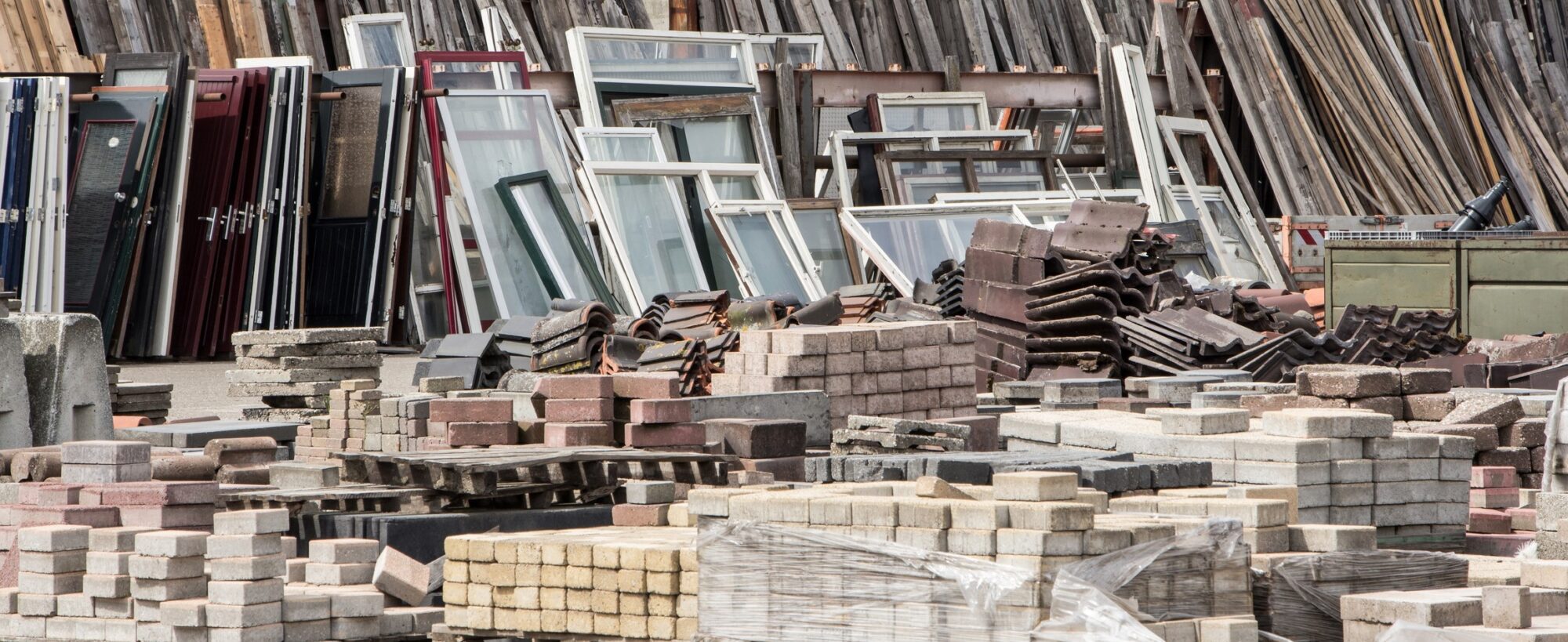
Credit: Sakorn Sukkasemsakorn
“If it can’t be reduced, reused, repaired, rebuilt, refurbished, refinished, resold, recycled, or composted, then it should be restricted, redesigned, or removed from production.”
Pete Seeger
The Circular Economy
Sustainability, in general terms, is about finding useful, looping processes are repeatable without depleting nonrenewable resources or destroying environmental systems like forests, grasslands, and water bodies. Straight to landfill designs such as single-use plastics, most kinds of packaging, unrepairable products such as cheap furniture, and most electronics waste carbon and resources and pollute our environment.
Reduce, reuse, and recycle are still the best tips for the use of materials. The majority of construction products are landfilled (or worse) long before they live out their useful lives, and the carbon emitted to create these materials will continue to exist in the atmosphere for 100 years or longer. Since most embodied carbon comes from raw materials extraction through manufacturing (called cradle to gate, Life Cycle Analysis stages A1-A3), using salvaging materials is the biggest lever we have to reduce the embodied carbon of buildings (Post 07).
The circular economy is an economic model where materials and products retain their value through their useful service life, being refurbished or remade into equal or higher quality products after their service life. This is an emerging field; few design teams actively seek reused and refurbished products and few of these products are (currently) available for purchase. However, new systems are being developed to bridge the gap for designers seeking re-use materials. Non-profit Building Reuse is leading some efforts and the All for Reuse map includes many of these current efforts. Some tools for assessing circularity are emerging. The AIA also developed a guide for Adaptability, Deconstruction, and Reuse. A common database for materials + health criteria is here (Materials Pledge db) and some funding is available (REMade Institute).
Just as building-scale embodied carbon analysis begins at the product level with Environmental Product Declarations, building reuse begins at the material and product scales, this post focuses on the circular economy of materials and products while the next post focuses on whole building reuse with an eye toward decarbonization.
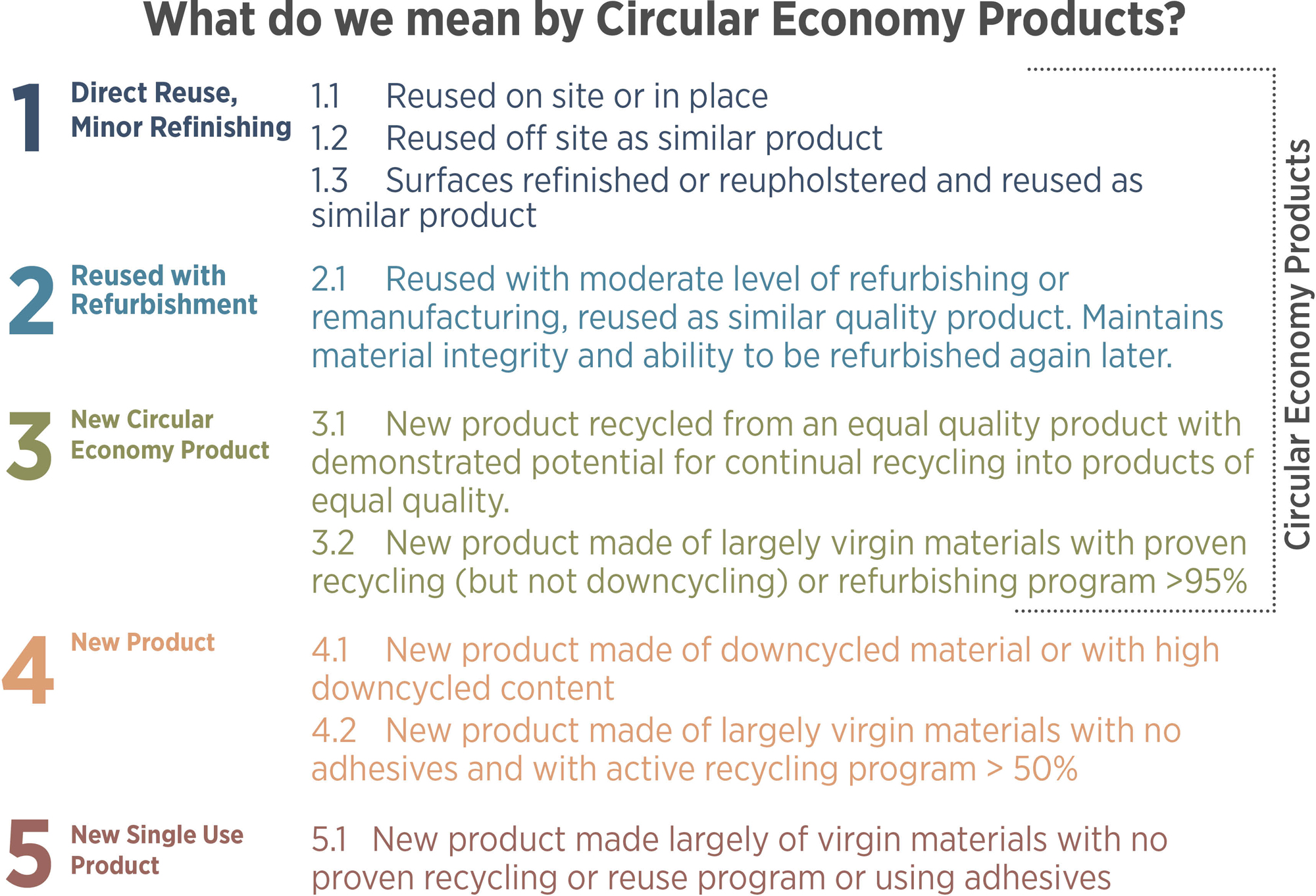
The circular economy incentivizes products to move up the chain towards levels 1-3, while most construction products today are single use, level 5 products.
Designing for the Dump?
Tenants generally renovate their commercial office spaces about once every 10 years. Trends toward 3 to 5 year commercial office space leases in recent years mean that tenants are leaving behind nearly new materials that often end up in the landfill at the end of their lease so the new tenant starts with an empty shell: walls, floors, ceilings, furniture, fixtures, and equipment. In the hospitality and retail sectors, the churn is happening at an even higher frequency to keep up with market and consumer trends (“finishes ugly out before they wear out”), with retail lease terms as short as 2 years. This churn results in an exponential growth in the waste output from the building industry. An LMN research study estimated that the cumulative embodied carbon from 60 years of cyclical renovations were likely greater than the embodied carbon from the building’s structure and envelope. While some innovative materials are now available (carbon sequestering, reduced manufacturing energy use, or produced using recycled content), focusing only on new products destined for the landfill will not get to net zero carbon.
Most products in the current economic model follow a linear process: raw resources are extracted, manufactured, distributed, used (often briefly), and then sent to a landfill or discarded into nature. Even many products advertised or labeled as recyclable like plastics end up disposed in landfills or in the oceans. The next time the same material is needed, more raw resources are extracted, resulting in an accumulation of wasted materials and carbon associated with the materials each cycle.
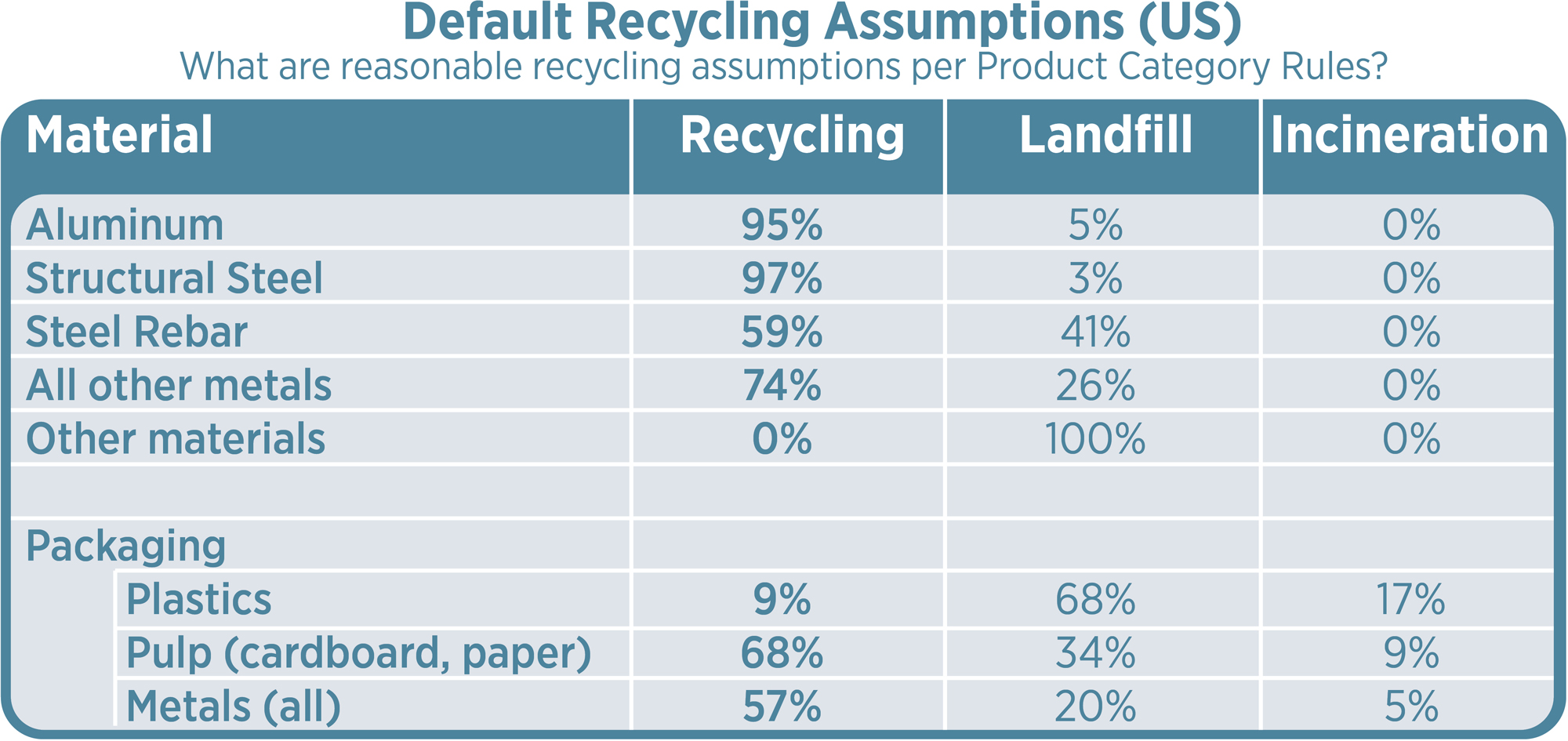
End of Life Assumptions from the Part A Product Category Rules for Building and Construction Products and Services (2024), based on research. While metals are generally recyclable and recycled it varies by type; plastics in packaging are not commonly recycled.
The industry standard metric for end-of-life material success is waste diversion, referring to the percent (usually by weight) that is kept out of the landfill. Waste diversion, however, includes many things that are not circular:
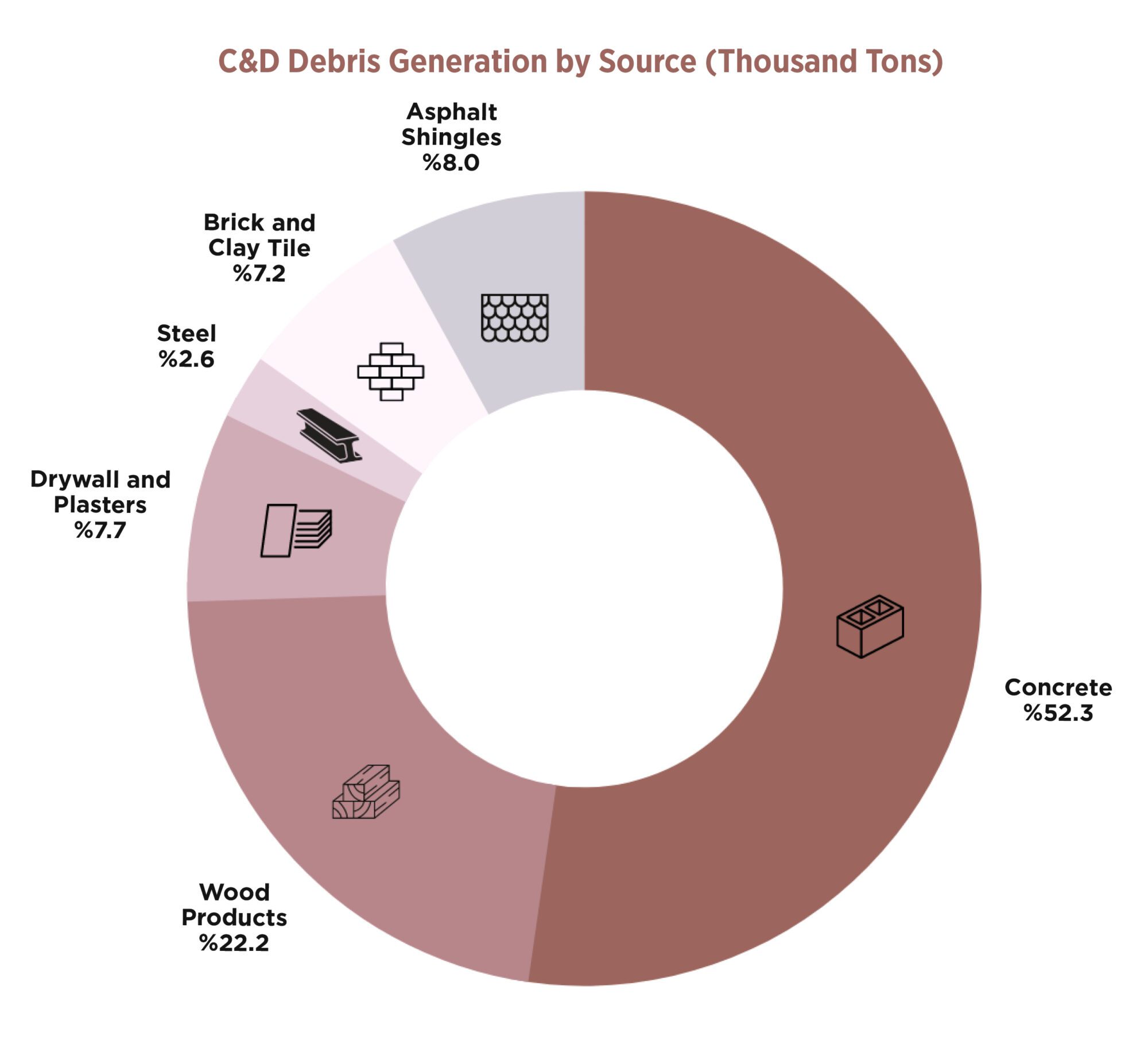
Proportional landfill percentages from some of the top categories in A majority of construction and demolition waste includes just a few categories of building products for the circular economy to initially focus on.
- 14% of US Municipal solid waste is incinerated, sometimes considered diversion even though it releases carbon stored in the material and pollutes air
- Selling waste to a third party to recycle can be considered diversion even if this material ultimately ends up in a landfill or incinerated
- Material is sometimes ground up and used as alternative daily cover at landfills or crushed and used in roadways
Many forms of waste diversion and so-called recycling provide a beneficial second use by downcycling the material. However, the circular economy for materials is based on recycling (resulting in a near-equal quality material as the original) or upcycling materials, which requires materials transparency.
Instead of waste diversion, we should focus on the percentage of material that is beneficially reused. This can include materials that are recycled, products that are refurbished and reused, and parts of buildings that remain in place.
In absolute terms, LEED v4.1 suggests good C+D waste practices are generally less than 10-15 lbs of total waste (including diverted material) per ft2 of building area, which reinforces front-end source reduction.
Organic materials will biodegrade in landfills (included in EPD module C), releasing around 15% of US methane emissions, which are sometimes captured or burned off. Aerobic composting of organics offers a better alternative, producing lower emissions than landfilling. Some ideas around storing biogenic materials long-term are being studied.
In a reuse model, carbon reductions are realized by keeping products and materials in the economy. This requires that products be designed with long-lasting parts, finishes that can be maintained or refurbished, and are easy to be disassembled and repaired. The circular economy goes one step further and includes that each component of a product has an end of life (a better term would be end of use) that becomes the raw material for another product.
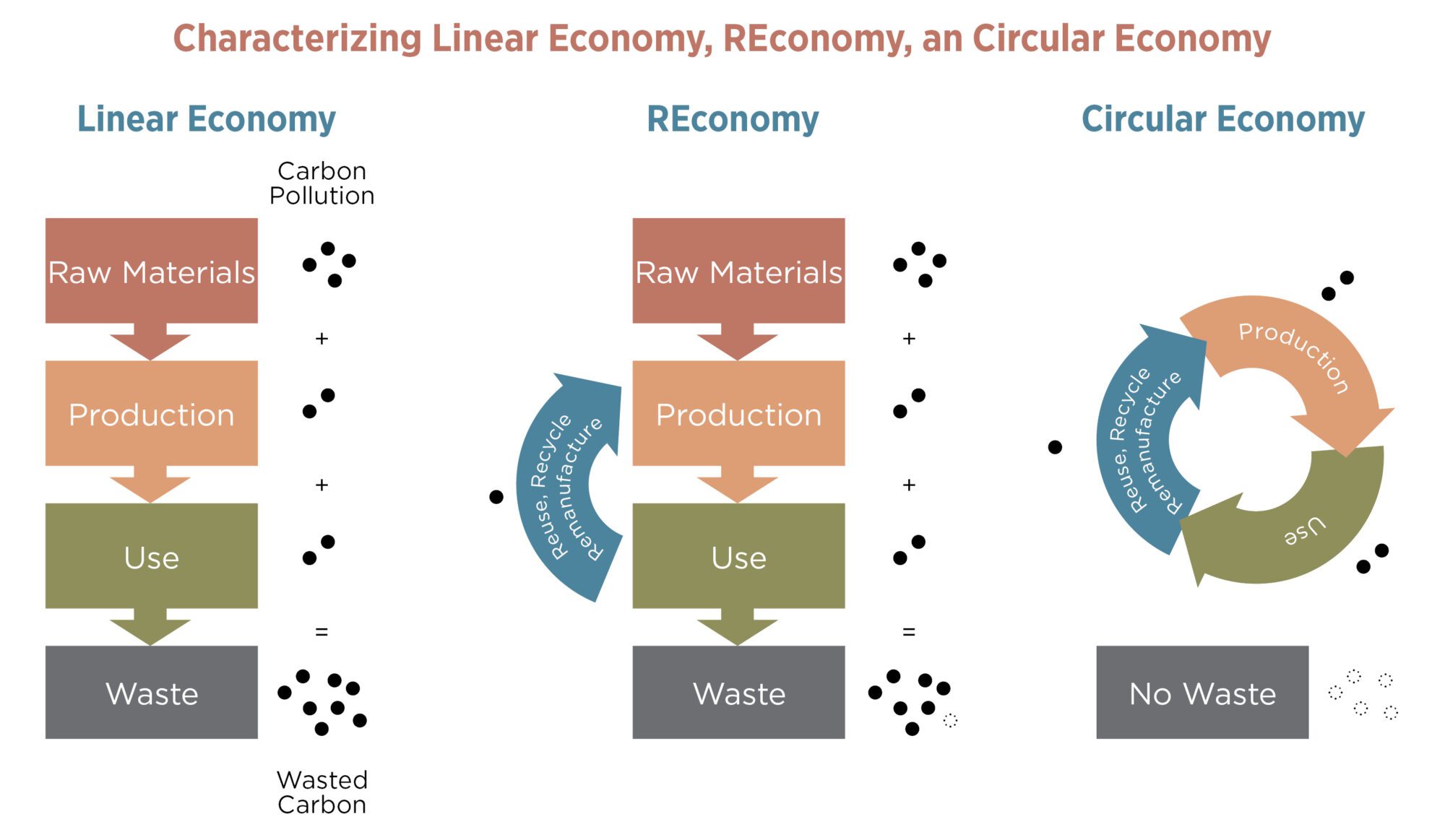
Most products are current designed for a single use, sending the embodied carbon to the landfill. A Reuse economy (think Goodwill, BuyNothing, and craigslist) gets a second, and perhaps third use out of materials, although they are still likely to end up in a landfill. The circular economy uses the end of life materials as the inputs for another product of the same quality, preserving nearly all of the carbon embodied in the manufacturing process.
What is a Circular Economy?
The circular economy is based on materials, products, and buildings being able to maintain value throughout their life. Materials that are designed to be part a product need to be recyclable or compostable and not contain harmful chemicals such as PFAS. Product designers need to combine these materials in a way that they can be detached for recycling or composting, ensuring that products are also repairable and able to accept a new finish so they can be refurbished and used for many years. And buildings need to be designed with long life in mind, using products that can be detached and reused. Large buildings have already been deconstructed, but to do this requires additional time for disassembly toward reuse, and warehousing of products.
There are some standards being developed for the Circular Economy:
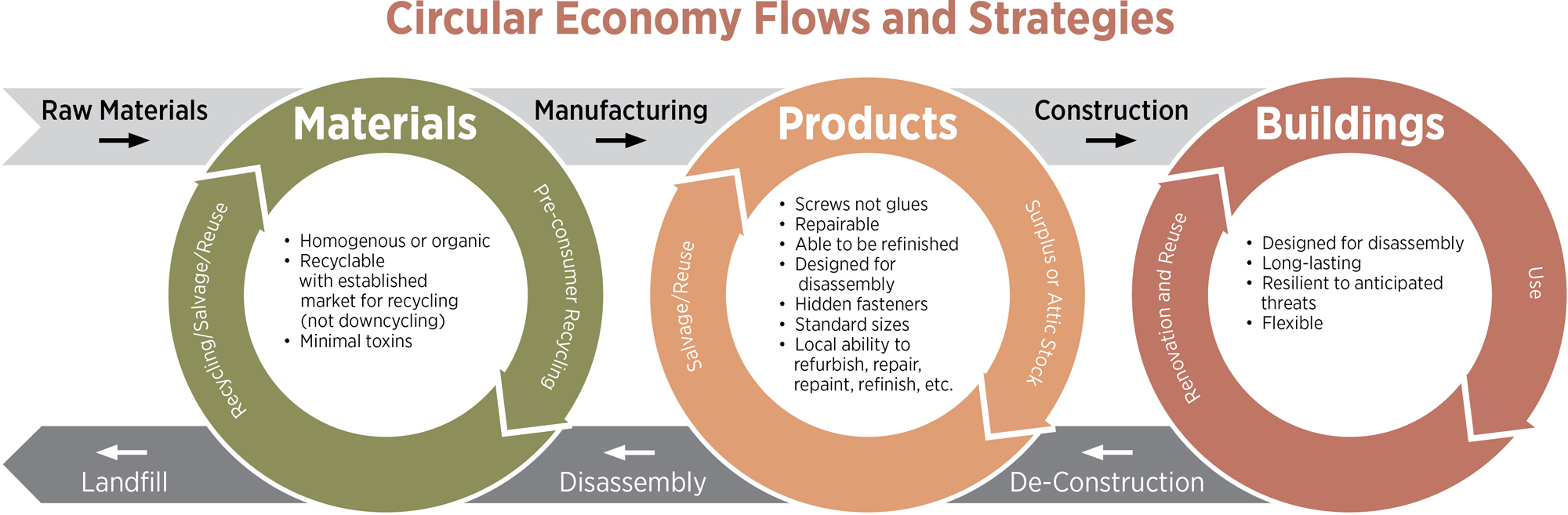
Carbon pollution is released during extraction and manufacturing that turns raw materials into products and then into buildings. The circular economy maintains or recovers the value as buildings, products, and materials reach the end of their service life.
The circular economy includes buildings, materials and products that have been designed to retain value even after many years of use. Flexible buildings can be repurposed if needed, demountable materials can be refurbished and reused when their initial location is renovated; if these don’t work, recycling is the last option and far preferable to landfilling materials and extracting and processing new materials from an environmental viewpoint.
The circular economy is expanding as more products are designed this way. Aluminum is a great example of a circular economy material. It can be cost-effectively recycled because producing new aluminum is more expensive (needing 20x the energy of recycled material), which has created an incentive for the manufacturing industry to set up recycling programs to capture material at the end of its first use. Most aluminum products (beverage cans, window mullions) are almost entirely made of aluminum, which is a huge advantage because there are few toxins or impurities added. It does not need a coating for many applications, making material separation for recycling easier. However, even with these advantages, recycling different alloys of aluminum is complicated, and more transparency is needed within other metals as well
Most materials, however, are not recycled. This includes most plastics, even if they have a recycling label on them. Product designers often do not start with materials that can easily be recycled, or they may specify glues, with the result that materials cannot be taken apart to be recycled at the end of the product’s life.
Some materials already have markets in some areas for reuse. Old timbers are often salvaged and reused whole to add character; other wood from scraps and fallen trees are given new life by Cambium Carbon. Other examples include doors unhinged, with refurbished doors sold with increasing scale, Davies furniture, the All for Reuse map and the Rheaply marketplace for salvaged and reused goods. As embodied carbon awareness and action become a priority, more product types are entering this space. Cradle to Cradle is the primary certification for circular economy products and is worth checking out as a primer on setting good criteria. Several HVAC equipment manufacturers in Europe refurbish equipment and parts as well.
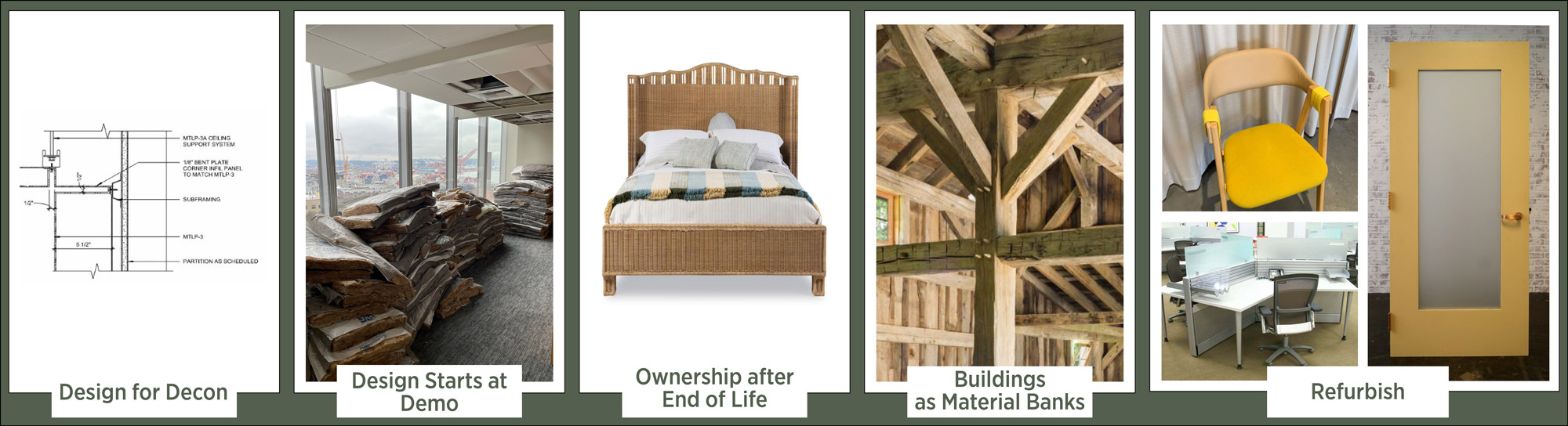
Circular economy principles and examples: Design for deconstruction allows later material recovery; Design starts at demo shows acoustic insulation salvaged for off-site reuse; Ownership after end of life, Heirloom; Buildings as material banks, New Old Barn; Refurbished, Doors Unhinged, Reseat, Davies Office
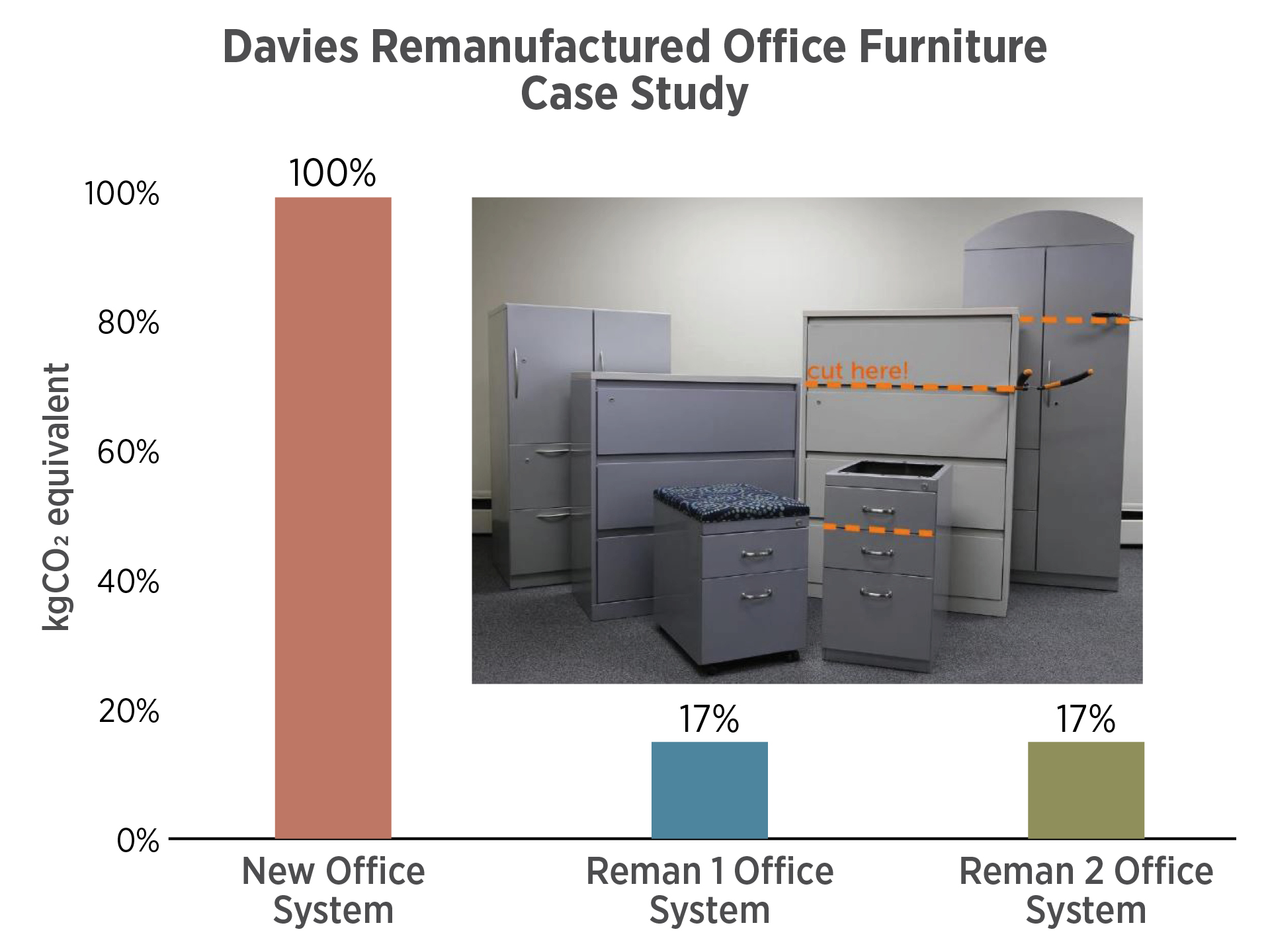
One study by Davies suggests that their remanufactured furniture reduces embodied carbon by over 80% compared to new office furniture.
There is currently little short-term financial incentive for building owners to invest in a circular economy product or deconstruction since careful deconstruction adds cost, landfilling is cheap, and we don’t yet have the infrastructure to properly value used products and materials. However, if a building owner leases a product, such as a table or chair or HVAC equipment, there a profit motive for circular economy properties with the manufacturer who maintains ownership: the long term owner has interest in taking the product back at some point to lease it again, so durable materials that can be repaired or refurbished are more profitable. This is a subscription business model, selling the use of a product instead of the product itself. Subscription models exist, for example, exist in the fashion industry, offering a slightly used higher end or vintage piece that is more financially accessible in its subsequent lives.
For circular economy to be possible, offering services, leasing components, and taking back materials need to become profitable activities. The cost of these activities and the market value of the components and materials involved needs to be identified. Product reuse potential and transformation capacity data needs to be captured and supplied by the product manufacturers so that suppliers, designers, and users can make decisions based on circular economy potential.
Benefits of a Circular Economy
A circular economy has other advantages beyond those described above.
Investors (and regulating bodies) are increasingly looking at Environmental, Social, and Governance (ESG) reporting to determine future business viability and there is an increase in market demand for circular products to help support zero carbon emissions. In addition, there are increasing legislative pressures and costs associated with carbon emissions, as well as extraction of virgin resources. Cities are also looking to the circular economy as a new engine for economic development and job growth.
Resource scarcity and supply chain issues are becoming more prevalent, meaning materials that we already have on hand that can be reused or recirculated with minimal alterations have increased in value. We’ve seen that reclaimed and salvaged materials have been more readily available than new, low embodied carbon materials coming from elsewhere during the pandemic. In addition to the environmental values of lowered carbon emissions, building owners can see economic and social benefits associated with a circularly designed project: costs savings from less new materials purchased, avoided waste disposal costs, and local economic benefits from product repair and refurbishment.
While many new materials are manufactured centrally and shipped worldwide, repair and refurbishment often occurs locally and requires local labor, creating green jobs. These jobs may be in deconstruction, sorting of salvageable materials, source separation, refinishing, and other areas.
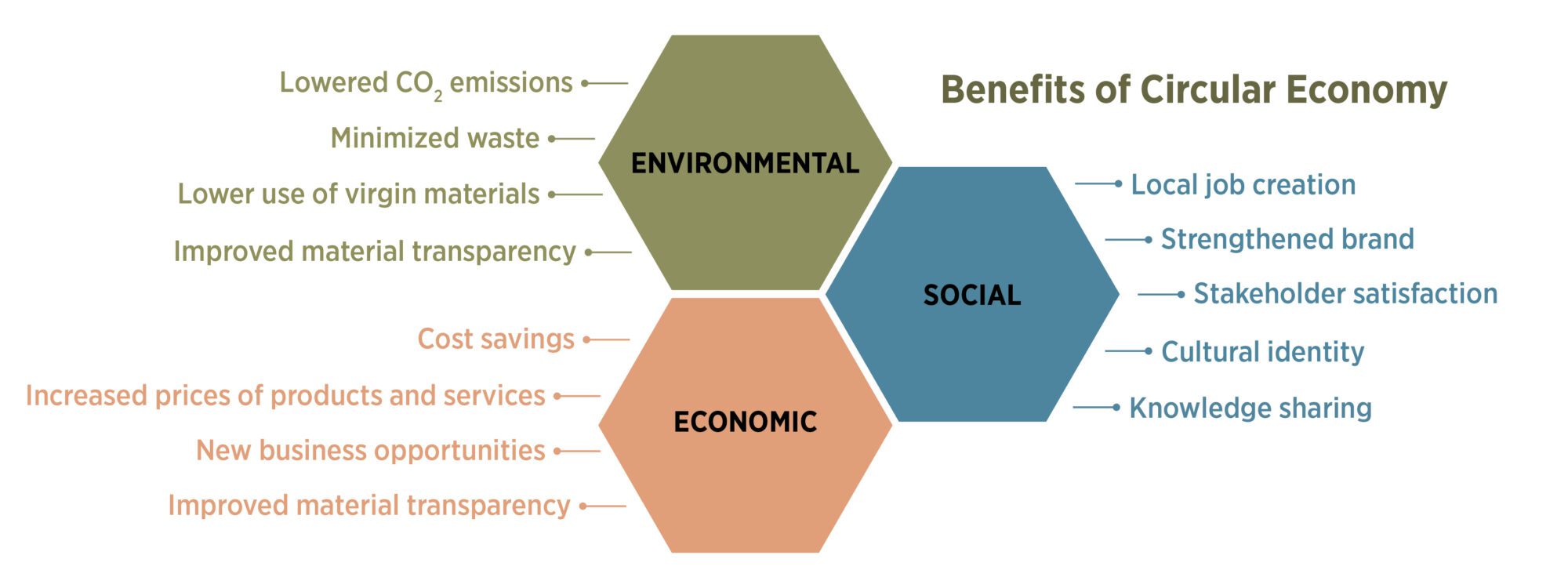
The circular economy includes many benefits. Scaling it is an important part of climate action.
Circular Economy Challenges
Initiating the transition to a more circular business model requires a comprehensive strategy within an industry or jurisdictional policies that have a similar effect. An industry – be it doors, floors, cabinetry, or windows – needs to have product recovered during deconstruction, brought back to saleable condition, stored until purchased, and demanded by design firms. For this to occur the product needs to be designed to enable this cycle and demanded by design firms. Any disruption or bottleneck along the chain dampens the economics.
Other challenges:
- Costs for virgin materials (that exclude externalities like pollution) are still often lower than that of recycled or recovered materials
- Upfront cost in product innovation and setting up new systems and workflows to support circularity
- Lack of consistent industry regulation and certification for material reuse
- Who fixes it when it breaks? Some products are not repairable, or local repair options don’t exist
- Warranty policies are rarely extended by the original manufacturer to a new owner
- Secondary materials and products are perceived to have a lower value compared to new primary materials and products
- Manufacturers are familiar with selling new products; while refurbishing can be economically viable it is not a familiar business model
- Inertia – design teams, manufacturers, contractors are not as familiar with the economics and availability of circular economy products
- It’s sometimes unclear how revenue is shared among owner, contractor, and demolition contractor for materials salvaged from a site
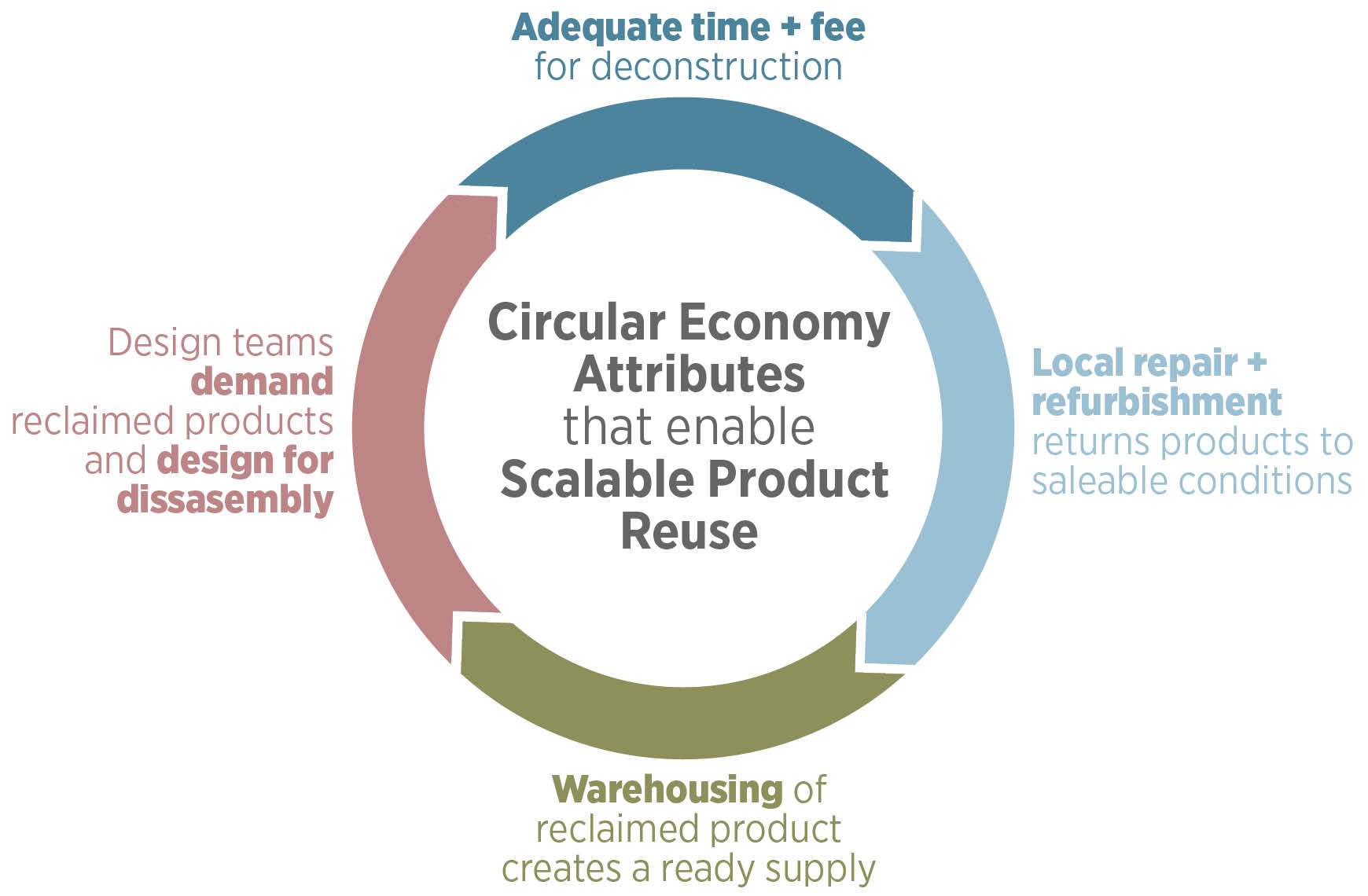
All parts of the circular economy need to function in order to work at scale. In most places, challenges exist at each step, but many companies and industries are working towards overcoming these challenges. Design and construction teams can design for disassembly and demand salvaged products to prime the market
Lastly, products are not designed for the circular economy. They combine many materials that are difficult to economically capture and reuse at their end of their service life. Carpet, for example, is rarely reused or recycled despite widespread take-back programs. California regulations (opposed by some in the industry) significantly increase carpet recycling rates.
Fortunately, the increasing awareness of the urgency of climate change has spurred innovations in the industry that aims to decrease embodied carbon and emissions and keep building materials from going to the landfill.
Design Starts at Deconstruction
Often, design team envisions a tenant improvement starting with an empty shell space, or a new building starting with a site cleared of existing buildings, parking lots, and other features. This is not carbon smart for two reasons: 1) each design team determines whether they take advantage of the carbon spent to create a site’s existing conditions, and 2) the availability of a reclaimed materials marketplace depends largely on whether materials are salvaged for reuse.
As soon as demolition is being considered, a pre-demolition survey of the existing assets should note any materials that could either remain in the project or be repurposed. Salvage subcontractors can be invited to tour the facility or review existing materials virtually (360-degree walk-throughs have been used for this). Carbon smart designs incorporate or work around existing assets that still have usefulness.
Designing with reclaimed materials can significantly reduce emissions but presents a different method of procurement. Contractors are familiar with lead times and occasional supply chain issues with new materials, while reclaimed materials require other strategies: 1) procurement is coordinated so that deconstruction of another space coincides with planned construction, or 2) a warehouse is available with sufficient products in stock. The design team likely needs to work directly with a contractor to discover solutions.
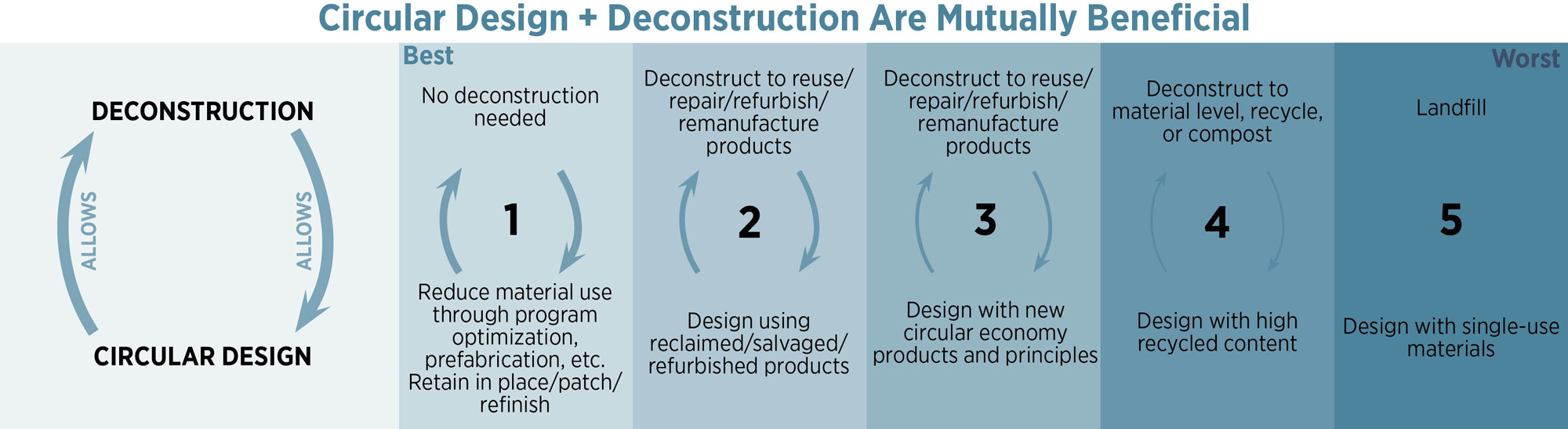
The ready supply of reclaimed materials (option 2 above) only happens when deconstruction teams have the appropriate scope and time to take apart building materials, and local resources exist to repair or refurbish them into salable condition. Some cities, like San Francisco, require salvaging of materials and are setting up physical or virtual warehousing for common materials.
Taking apart materials with minimal damage requires more labor and coordination than demolition. Deconstructed materials need to be sorted, palleted, and wrapped with protection for transportation. Since this has additional cost, design and construction teams need to put as much thought into how materials come apart as we put into the details of how materials come together.
Some deconstruction friendly design strategies include using universal fasteners and screws instead of glues and adhesives. Not only do full adhesives make materials more difficult to separate from their substrates, but they can also pollute the recycling processes, resulting in downcycling or landfilling as the material is degraded. Wood finish materials can only be reused or salvaged under certain conditions: painted or stained wood can be reused or sent to a recycler, but creosote soaked wood has to be landfilled. Many reuse stores show which products are likely to retain value and be resold, while local repair centers (example) are starting to become common.
In an ideal situation, when a finished project is turned over to the owner or tenant, there is a bill of materials and guidance on how they can be repurposed or reused, giving the owner an understanding of deconstruction opportunities and the value remaining in the materials when replacement occurs.
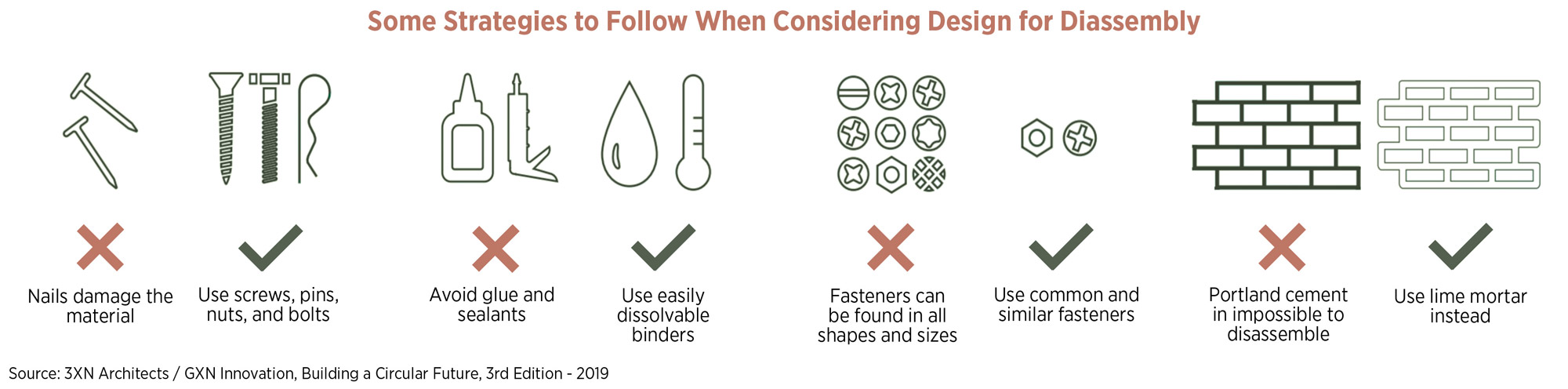
Some basic principles in designing for deconstruction. Courtesy GXN Innovation
Accounting for Circular Economy Carbon
Buildings, products, and materials should not be a single use. Many construction products that are in good working order, especially unused attic stock, can be economically salvaged. How do we account for the substantial carbon benefits of salvaging by avoiding end of life carbon emissions? Current accounting excludes the end of life of existing materials. This may show that, for example, landfilling an old wood door and buying a new one has a carbon benefit. (This happens because the new door sequesters and stores carbon during its lifetime while a typical LCA ignores the decomposition of the discarded door in the landfill)
The primary carbon benefit of building and product reuse is in displacing embodied carbon from future construction; while some C-stage carbon is saved by not landfilling, the A-stage carbon from a subsequent remodel is the important contribution. RICS v2.0 ‘Whole Life Carbon Assessment for the Built Environment’ v2.0 has a method, described in Post 07, for incorporating B-stage reductions. However, making materials available to displace A-stage carbon from other buildings is excluded from LCA practice.
Currently LCA practice does not include the disposal, salvage, or reuse of products and materials that are part of demo, even though the design team has some control over their fate. These are considered part of the original design’s LCA. However, LMN believes that we need to include these in LCA when we prepare drawings or specs. As our client’s trusted advisors, we have more control over the demolition of existing components now than have over demolition of our design 60 years from now (a 60 year analysis is common in current LCA accounting). We propose a ‘Transactional LCA’ (Post 03) that adds limited portions of the end of life (module C and optional module D) stages of existing materials based on tracking the actual end of life scenario of each product.
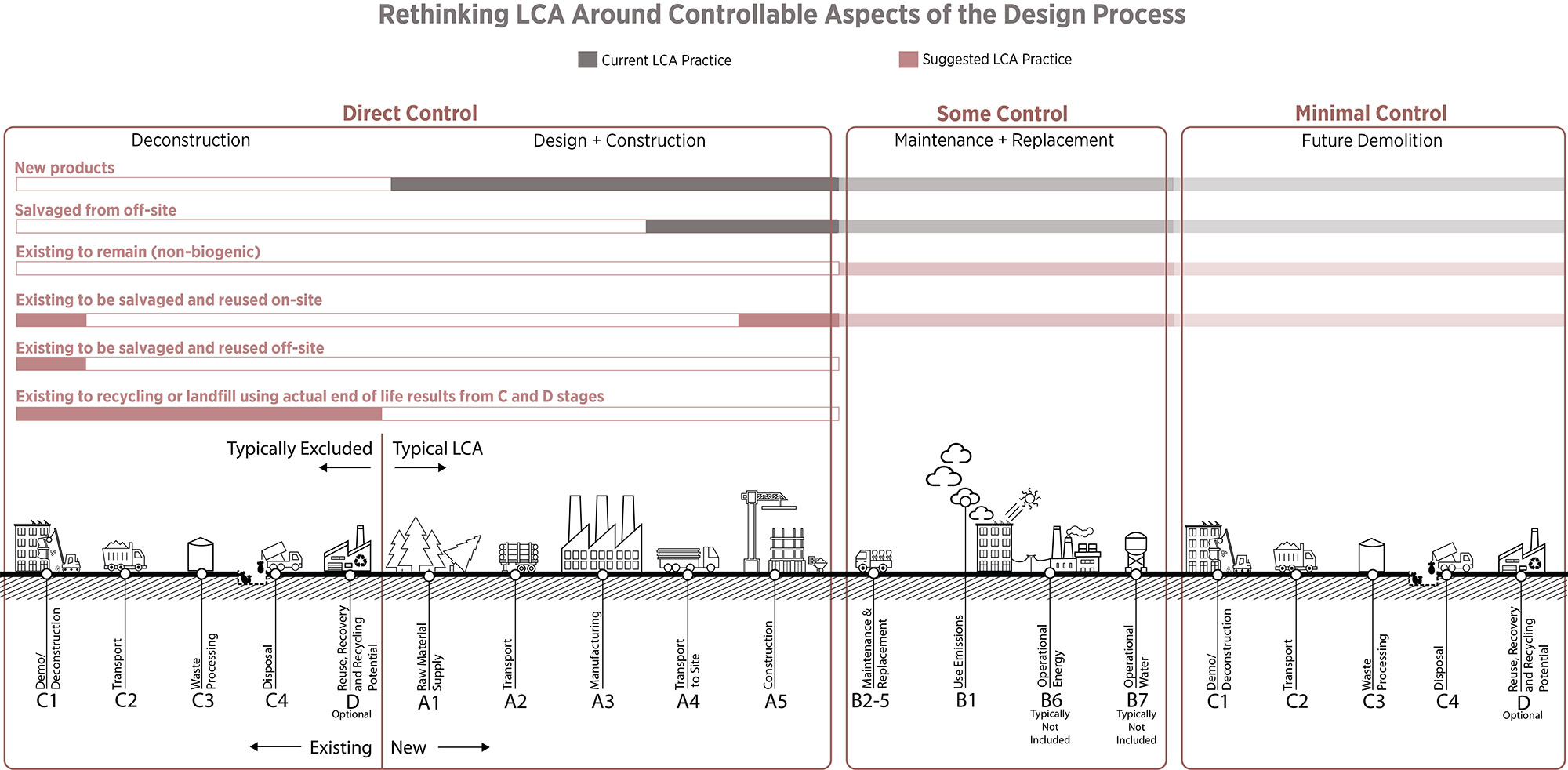
Building owners (advised by design and construction teams) control the fate of materials retained or removed from a site. While this is typically excluded from Life Cycle Analysis (LCA), LMN believes this should be included because it is more directly controlled by the owner than many parts of LCA that occur in the distant future. The diagram above shows how we believe materials should be considered from a carbon accounting perspective.
Conclusions and Recommendations
The phrase, “it uglies out before it wears out” points to the fact that due to social and cultural trends, end users often renovate a space before the materials within have lived out its functional life. With the built environment sector consuming almost half the world’s extracted resources every year, we need to rethink our designs to reduce the need for new materials. Design for deconstruction and circular economy concepts create market for reuse that offers a sustainable path to reduce the burdens that the built environment places on our planet.
Carbon estimation challenges remain. For example, most carbon analyses do not consider whether a chair is durable and repairable – in fact, an EPD may suggest that it is not preferable because it has a higher initial embodied carbon. Our industry needs to coalesce around these challenges to make our calculations reflect the realities of carbon emissions.
Recommendations
- Design begins at deconstruction – designers need to survey and take ownership of the existing materials with remaining life on site, finding use in the new designs or finding reuse potential off site.
- Designers should include a good demolition specification section to encourage end of life reuse for existing materials, including adequate time and fee for deconstruction.
- Design using salvaged materials and circular economy products. Demanding reused and refurbished products creates a market for deconstruction and warehousing necessary for the circular economy to thrive.
Please email any questions or comments to Kjell Anderson, kanderson@lmnarchitects.com
Thanks to our external collaborators and peer reviewers
Laura Soma, GLY; Kristen Fritsch, Elkus Manfredi Architects; Erica Weeks, Hastings Architecture; Dave Walsh, Dave Walsh Consulting LLC; Barbra Batshalom, Sustainable Performance Institute; Valentina Rappa, Rheaply; Thomas Fecarotta, Rheaply; Daniel Kietzer, Rheaply
LMN Architects Team
Huma Timurbanga, Justin Schwartzhoff, Jenn Chen, Chris Savage, Kjell Anderson
Posted: 12/08/2022
Edited: 03/25/2025
The text, images and graphics published here should be credited to LMN Architects unless stated otherwise. Permission to distribute, remix, adapt, and build upon the material in any medium or format for noncommercial purposes is granted as long as attribution is given to LMN Architects.