#pathtozerocarbon, #sustainability
15 – Interiors, Cyclical Renovations + Carbon
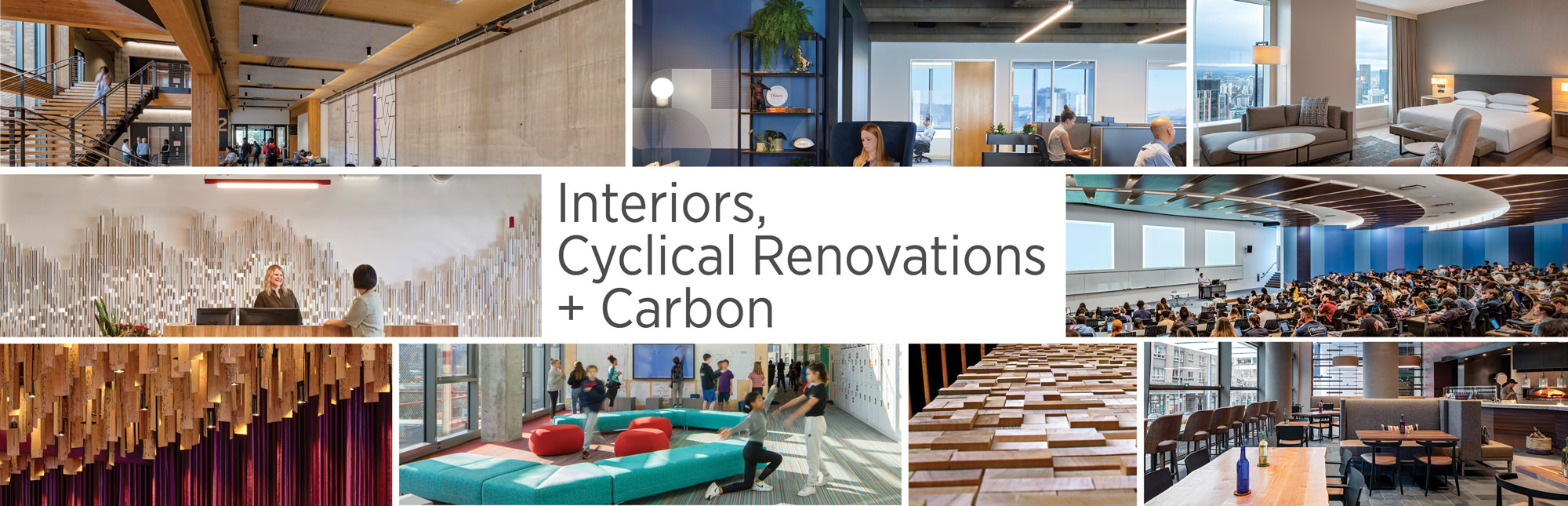
Roughly 80% of the buildings projected to exist in developed nations in 2050 have already been built, meaning carbon pollution from structure, envelope, and in many cases major services such as MEP systems have already entered the atmosphere. Multiple interior renovations within these existing buildings, however, are likely to occur before 2050, with scopes ranging from updating FF&E and finish materials, to major revisions to space planning, MEP systems and deep energy retrofits, lighting, and other building major system elements. Due to the frequency of recurrences, interior renovations have significant carbon impact, but they are also where the opportunities lie for decarbonation after a building has been built. The building industry must pivot quickly to develop marketplaces, material selection criteria, and design strategies to be able to create beautiful, healthy environments with minimized carbon impacts.
This post builds on Post 09 – Circular Economy and Post 10 – Existing Buildings
The Real Embodied Carbon Impact of Interior Projects
A 2019 Cyclical Tenant Improvement study estimated that cyclical tenant improvements within a building had accumulated more embodied carbon over 60 years than the structure and envelope combined. While embodied carbon investments in envelope and structure are high, they are also long-lived. Renovation cycles are as frequent as 5 years in hospitality, retail, and office spaces. Tenant contracts often include a ‘restoration’ clause that requires their space to be returned to its original state, meaning walls, ceilings, lighting, furnishing and fixtures to be removed (often landfilled) when they move out. Given time and cost constraints, this results in many materials with a decade or more of remaining useful life to be discarded prematurely. This revelation of the cumulative impact of interiors embodied carbon inspired a Climate Toolkit for Interior Design, inviting a scope of work previously left out of the embodied carbon conversation.
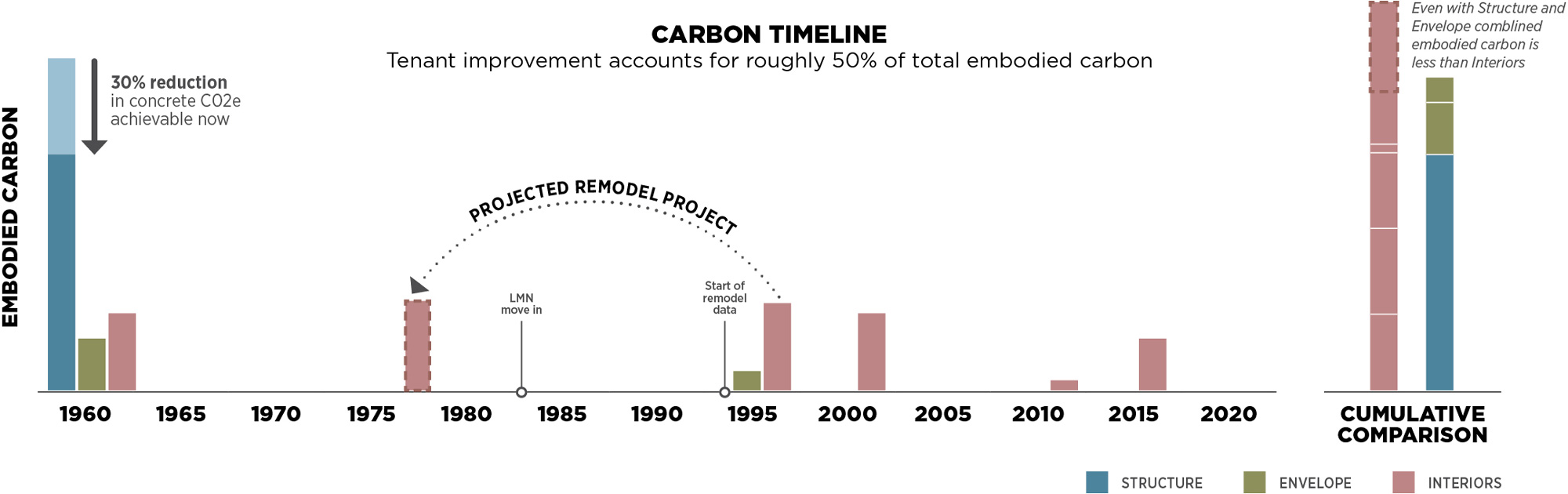
Figure 1: Studying the interior material renovations between 1995 and 2020, and projecting one additional remodel during a data gap, showed that the total carbon impact of interiors renovations may have been larger over this time period than structure and enclosure. Some furniture was included, while MEP systems were excluded, structure is shown with and without a 30% embodied carbon reduction based on current practice.
Transparency labels, such as Environmental Product Declarations (EPDs), which show finish material products’ Global Warming Potential (GWP, expressed in kg-CO2e), provide important quantifiable carbon data, making it possible to compare carbon impact as part of low carbon design decision-making process. These are readily available for some material categories, such as carpet tiles and acoustic ceiling tiles. However, capturing the whole scope of the interiors impact is difficult due to the large number of unique material types spanning many specification sections, and the number of manufacturers competing in each material type category. In addition, the complexity of each product’s composition, supply chain, demand for a wide variety of new products and performance attributes make it difficult for manufacturers to provide third party verified carbon data in a consistent format. The industry is already aware of this when looking for transparency on health and toxicity: larger manufacturers and popular product lines are more likely to provide EPDs and other transparency labels, while the cost of compiling and publishing this data often challenge smaller manufacturers.
The complexity and lack of data means that many additional material categories, including Furniture, Fixtures, and Equipment (FF&E), casework, and lighting, are often omitted from carbon calculations despite having a surprisingly large emissions impact.
Capturing the full picture of the interiors scope is more effort than structure and envelope, and project teams likely do not have the fee and time to address each material. However, there are easy strategies to make big impacts. In this post, we will explore some of the hidden carbon impacts related to the interior scope and strategies we can deploy to counteract these impacts.
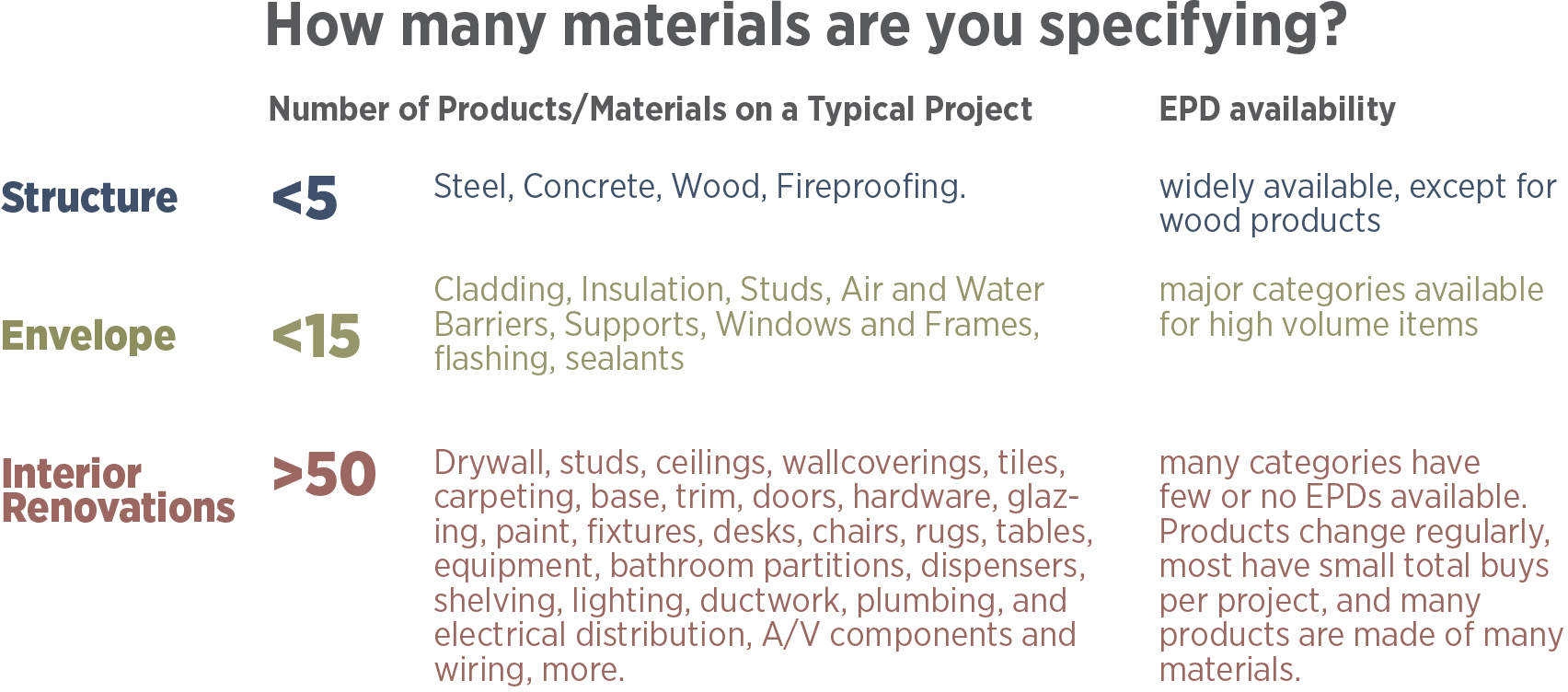
Interior materials are often excluded from so-called Whole Building Life Cycle Analyses because they include a wide variety of materials with less EPD data available. Getting EPD data for these products is a cost challenge for manufacturers due to the wide variety of products and lower purchase volumes for each product type.
Furniture: The Hidden Waste Stream and Carbon Polluter
The rise of “fast furniture,” a term referring to furniture and similar home goods made in many styles quickly and cheaply, much like the term “fast fashion” in the fashion industry, led furniture to be one of the fastest growing landfill categories. In 2018, the US generated 12.1 million tons of Furniture waste, which is an increase of 450% since the 1960s. As a result, most of the furniture currently in landfill was made within the last 10 to 15 years. One study suggests that FF&E can be responsible for 25% of greenhouse gas emissions and non-renewable energy consumption and 15% of primary energy consumption compared to the overall impacts of the building.
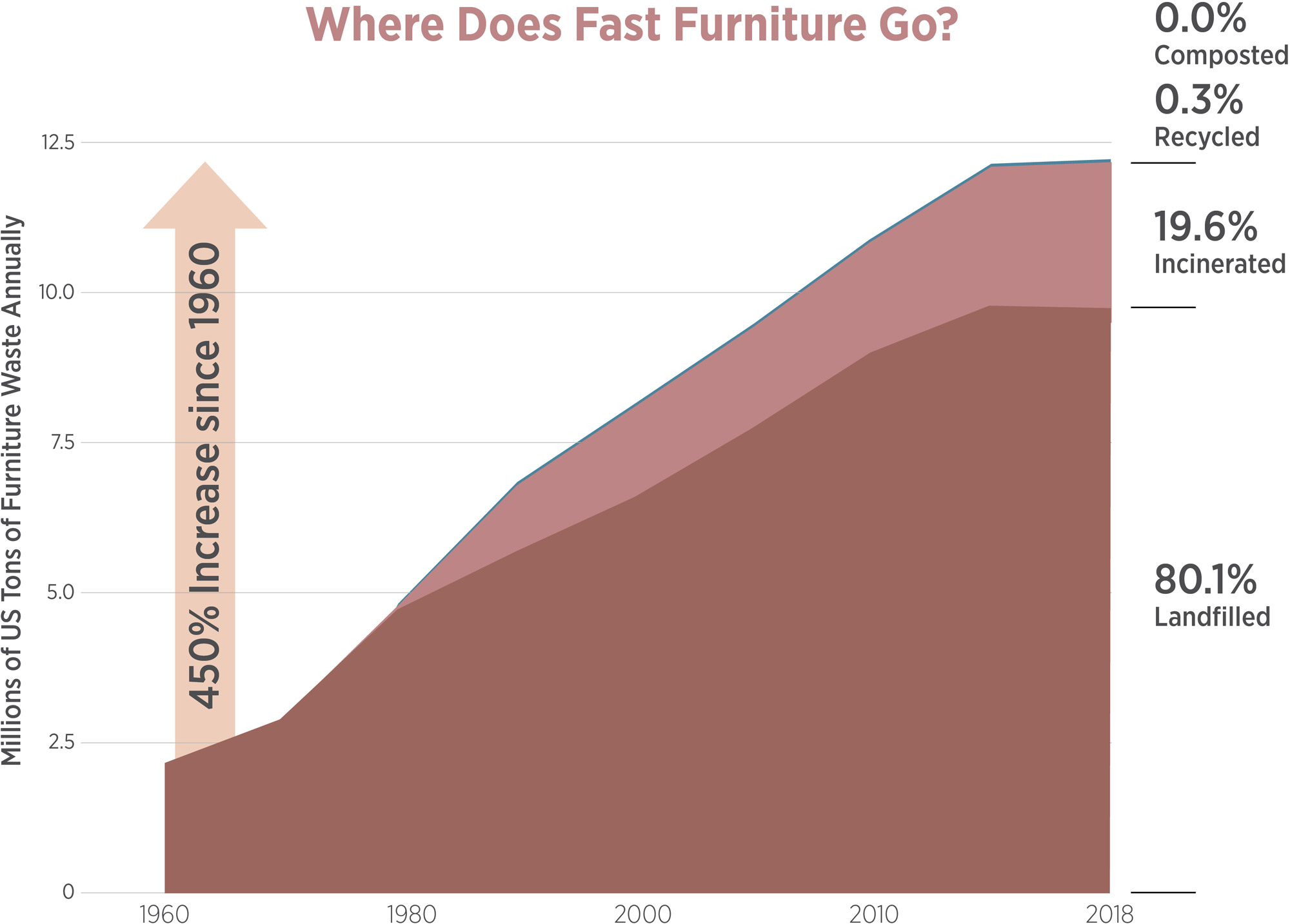
Furniture waste in the US has increased 450% since 1960, with only negligible amounts recycled or composted.
“Fast furniture” and much other contemporary furniture is not built to last or easy to repair, making it often cheaper to buy new than to fix or refinish existing furniture. Furniture recycling is also difficult, especially furniture types that are made up of multiple layers of different materials and those using adhesives, such as upholstered chairs or mattresses. The result of this poor furniture design is that 80% of the furniture is landfilled and nearly all the rest is incinerated.
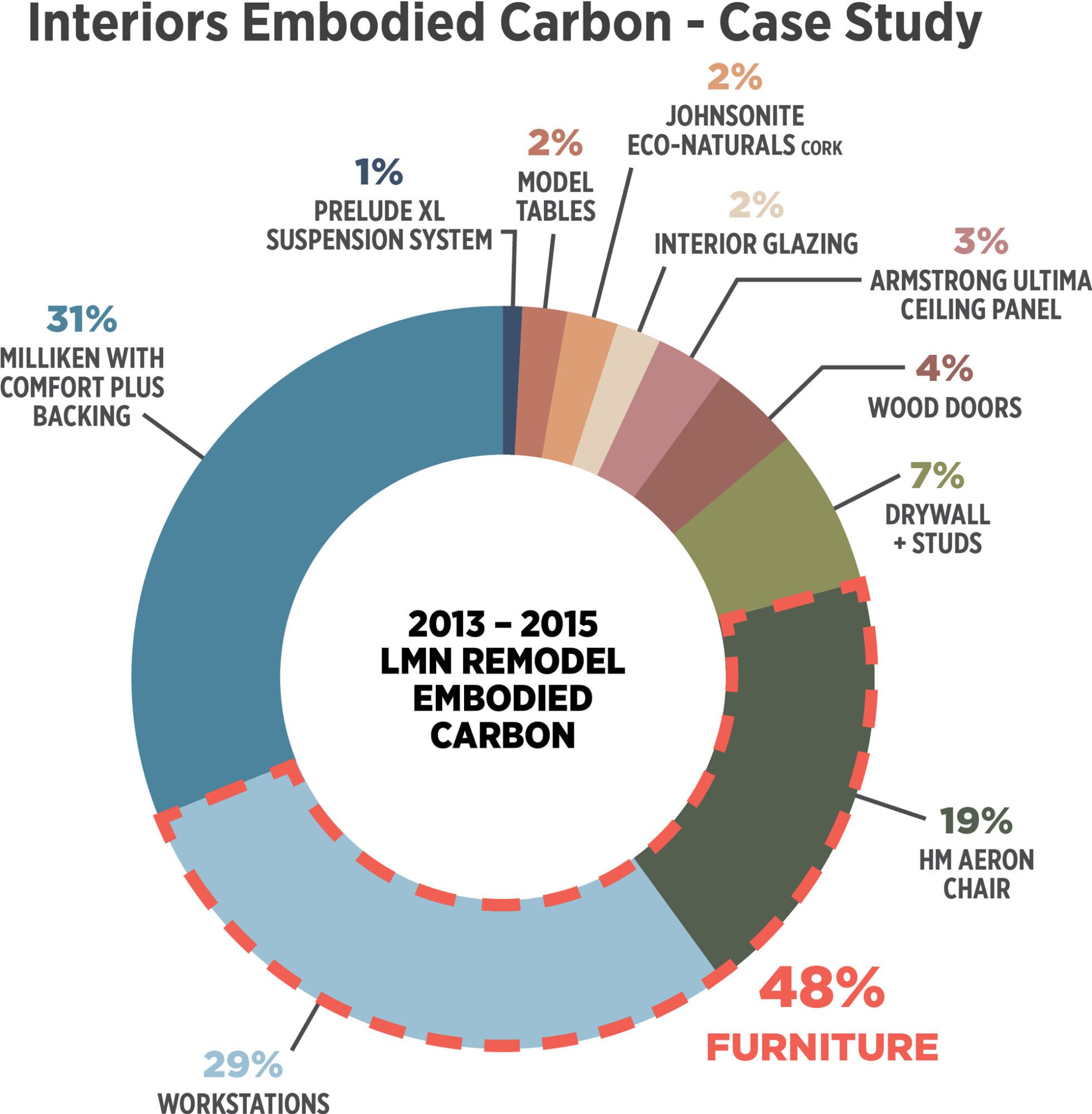
A remodel’s total embodied carbon was roughly 50% attributed to furniture.
Office furniture is the primary source of furniture waste, accounting for an estimated 8.5 million tons per year. Most office furniture is meant to last 10 to 15 years or longer, but the average leases are now 7 years or lower, and tenants don’t typically transfer existing furniture to new office locations or reuse furniture when a refresh occurs. Busy office managers don’t always have the time or expertise to ensure recycling or reuse of FF&E during decommissioning of an office space. Without a plan in place, furniture can easily end up in the landfill. With offices downsizing to accommodate the shift to hybrid work, this volume of furniture waste will likely increase over the next few years.
In another study done by MSR Design in 2022, the carbon footprint of commercial furniture was equal to the entire rest of the renovation. This demonstrates the huge embodied carbon impact of furniture, yet carbon reporting frameworks do not require furniture to be accounted for in LCA calculations. Product specific data and information on the embodied carbon of furniture is scarce compared to other building materials, often due to difficulty in capturing data related to all the complex components and diverse materials. Few furniture products have EPDs readily available to capture the impact or to make meaningful comparisons.
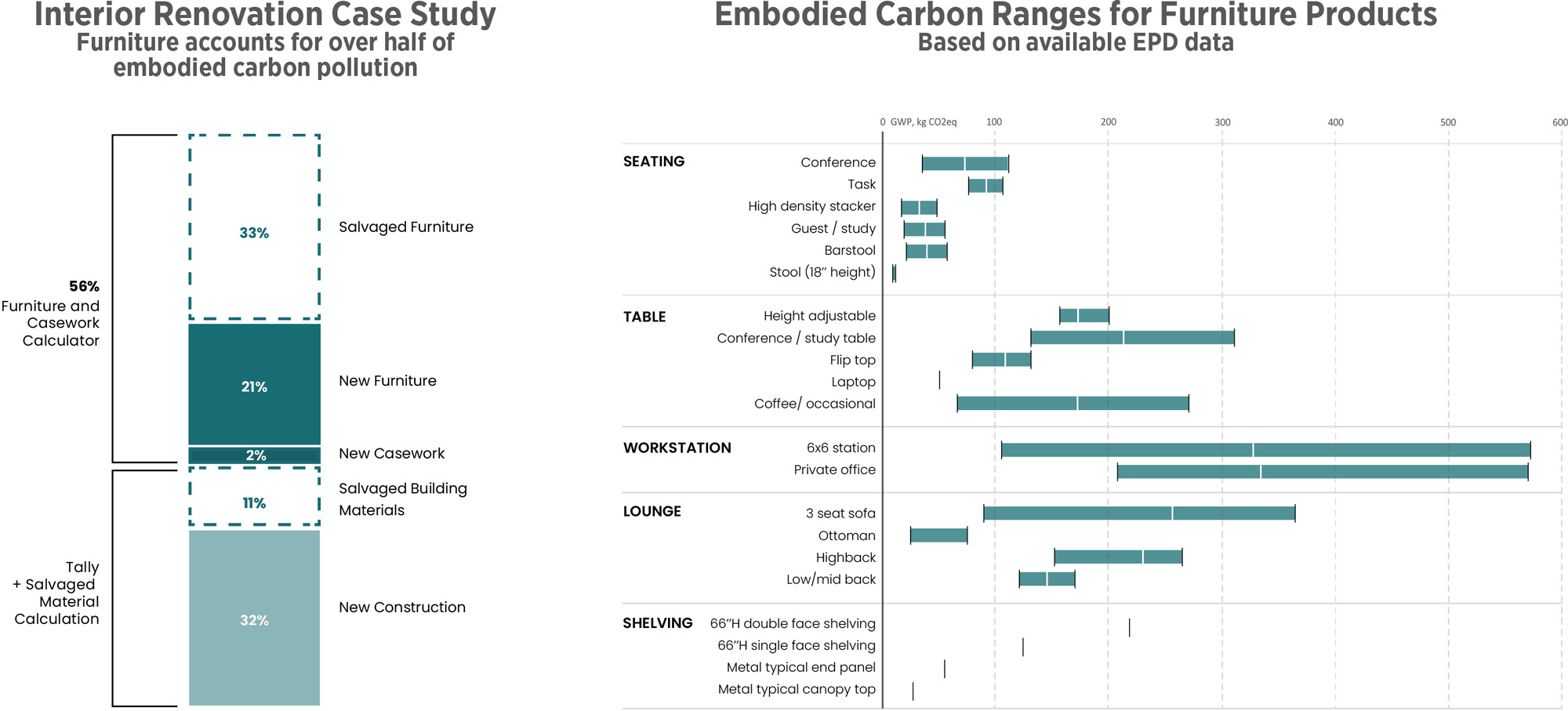
A study and report by MSR Design shows (left) that furniture accounted for over half of their renovation’s embodied carbon. The right graph shows furniture embodied carbon ranges, based on available EPD data.
FIRA (Furniture Industry Research Association) conducted a study in 2011 that provides general kg-CO2e numbers for various furniture types. Since then, many manufacturers have brought to market products claiming zero carbon or carbon neutral, primarily through carbon emission off-setting. Others are taking the difficult but more important steps that include innovations in raw material sourcing, updated design to reduce raw material needs, using renewable energy in manufacturing, and/or designing for reconfigurability or disassembly so that each material component can be more easily reused, repaired, or recycled. As designers and specifiers, we should give preference to manufacturers that are actively changing their business practices to lower the embodied carbon of their products, in addition to focusing on extending the useful service life of furniture and having proper systems in place to recapture as much materials as possible from the landfill.
Below are some general guidelines when it comes to lowering the carbon impact of FFE scope:
- Prioritize second use or remanufactured furniture through companies like Reseat or Davies, or seek out general reuse marketplaces such as Rheaply and those found on All for Reuse.
- Wood-based products generally have less embodied carbon than similar metal-based products. According to the FIRA study, wood pedestal comes to be around 28 kg-CO2e, whereas a steel pedestal is around 44 kg-CO2e.
- Solid wood materials are more easily sanded, refinished, or salvaged. Plywood is next best, followed by particle board and MDF. Materials that require veneer or plastic laminates are less maintainable and may not be able to be recycled.
- Consider how long something will last and what can be done at its end of life. Ask whether or not it is reconfigurable, can be disassembled with replaceable / repairable parts, or can easily be updated for aesthetic reasons (i.e. exchangeable slip covers or detachable cushions for a sofa). Items with these qualities have a higher chance of being reused in the future.
- Provide end users strategies for reuse, repair, and landfill diversion resources for furniture — sometimes called a material passport.
- When inheriting furniture as part of a space, include time to assess remaining furniture value and allow appropriate time to refurbish or salvage furniture.
- If your organization has design guidelines for FF&E, review and update your requirements to ensure they are not preventing the reuse of furniture.
Casework
Casework is another product category often excluded in interior LCAs, but studies have shown that it can have a significant embodied carbon impact. Different construction methods, substrates, finishes, and countertop materials can vary the embodied carbon impact of a casework unit greatly. Some project types, such as labs and multi-family housing, have significant needs for casework, leading to this material category being amongst the highest carbon intensity in the interior LCA overall.
Cabinetry is often style-specific, and combining multiple casework styles to create a consistent design without remanufacturing is difficult. Additionally, typical construction methods make disassembly for reuse challenging. Permanently adhered finishes such as plastic laminate make updating the finished look and matching up corresponding hardware an unlikely scenario. Labor time and cost also makes remanufacturing prohibitive. All these lead to casework being discarded in many renovations. A tool can help estimate the initial impact of casework embodied carbon; however, looking for ways to reuse raw materials and reuse existing casework remain the priorities.
Lighting
LED lighting’s energy efficiency and long lifespan are a great solution to lower operational energy used with the added potential benefit of lowering embodied carbon for replacement fixtures. LED requires more carbon and energy to manufacture than older technologies such as halogen, incandescent, and fluorescents. While operational energy savings mean that we should continue to prefer LED fixtures, lighting has significant embodied carbon impact overall; replacing LED fixtures before their (longer) lifespan is over has a large impact on waste and total carbon pollution.
Most light fixtures are made with metal housing, which is a high embodied carbon material, and about half of the weight of a linear fixture may be the housing. Designing to limit the total number of light fixtures in an interior project, especially in situations where layers of lighting functions are required within multi-scene spaces, and their associated embodied carbon, is an embodied carbon reduction strategy. In a study done by CLF, interior lighting is the fifth highest carbon impact categories for a commercial Tenant Improvement overall.
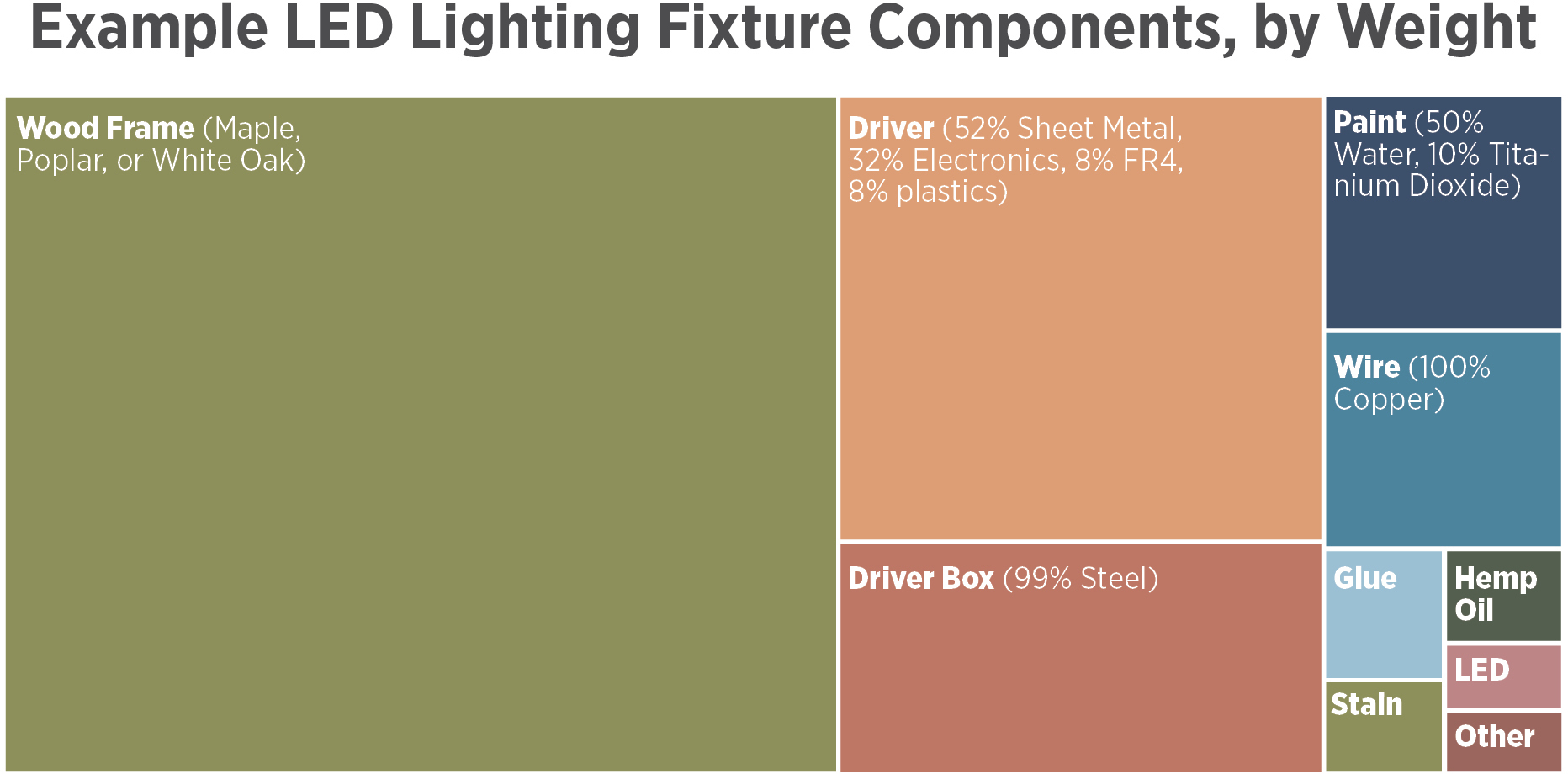
A lighting fixture EPD suggests that the frame is about half the weight. This product uses wood, which can be a carbon-neutral material. Another light fixture EPD suggests that the metal housing is also a significant carbon source, so simply reducing or replacing the metal frame with a low-carbon material can be beneficial. The driver and driver box are also significant sources of emissions since they are primarily made of metals.
In the past, burnt out bulbs could be easily maintained and replaced by facility maintenance crew, tenants or homeowners. Today, integrated LED light fixture components are often permanently affixed together, making it more difficult to maintain and repair on-site, resulting in the whole fixture being disposed of upon failure. The design of cyclical renovations often results in all light fixtures often becoming waste, stripped to make way for new lighting ideas. In addition, while some components of LED lamps and luminaires are recyclable, they are difficult to disassemble for parts to be salvaged or recycled.
The lighting industry is beginning to shift focus towards the embodied carbon of lighting with the formation of organizations like the Green Light Alliance and lighting embodied carbon studies such as Light on Waste. We are also starting to see material use and construction innovations on the market to lower typical light fixture embodied carbon. One example: Lightly fixtures use wood and wool felt as their primary housing materials instead of metal. Their design also eliminates the need for an acrylic lens diffusor, which degrades over time, affecting lighting quality and limiting reuse. A project requiring lighting retrofit as a way to minimize embodied carbon shows considerable promise in reusing and retrofitting existing light fixtures.
Strategies to consider when selecting lighting fixtures are similar to other building materials.
- Reuse, if possible, then find low embodied carbon products (in turn awarding manufacturers that have documented their environmental impact through an EPD).
- Consider the longevity of the fixtures. Cheaply made products have a high failure rate, requiring more fixtures due to lessened efficacy, and may require more conduits and wiring leading to more embodied carbon.
- Consider the ease of disassembly at end of life.
Modular luminaires allow for components to deconstructed and repaired or recycled, minimizing the embodied carbon and extending the life of the fixture.
Minimizing Excess and Accessing Surplus
The built environment uses almost half of the world’s extracted materials and generates as much as 2.2 billion tons of Construction and Demolition (C&D) waste globally each year by 2025. The amount of C&D waste generation is also accelerating: US C&D waste increased by 342% from 1990 to 2018. Not only does the demolition of buildings generate waste, but surplus building materials and products that are purchased but not installed also contribute to the waste stream. There are several reasons why surplus occur:
- Over-ordering in anticipation for mistakes or breakages during installation (Ceramic tile breakages are common during installation and are often ordered with 12-15% overage).
- Over-ordering to meet minimal product cost break requirements.
- Attic stock requirements for future maintenance or replacement needs.
- Modifications made during construction prompting change orders.
- Desires for aesthetic consistency to minimize unwanted variations in product finishes (For example, wood flooring is typically ordered with 10% overage to ensure aesthetic consistency).
Up to 30% of all building materials delivered to a typical construction site can end up as waste, not even used once. Interior finishes make up a large portion of these surplus items for several reasons. Their ownership is often transferred to the client, but clients don’t always have the desire or capacity to store these products. Their project-specific aesthetics and timing make them difficult to transfer to a different project as warrantees often don’t transfer, and rarely will manufacturers take back products already produced for a project. Some are landfilled immediately as part of C&D waste, while a large majority are stored either by the material installer/distributor or owner until they run out of room or relevancy, at which point they likely end up in the landfill as well.
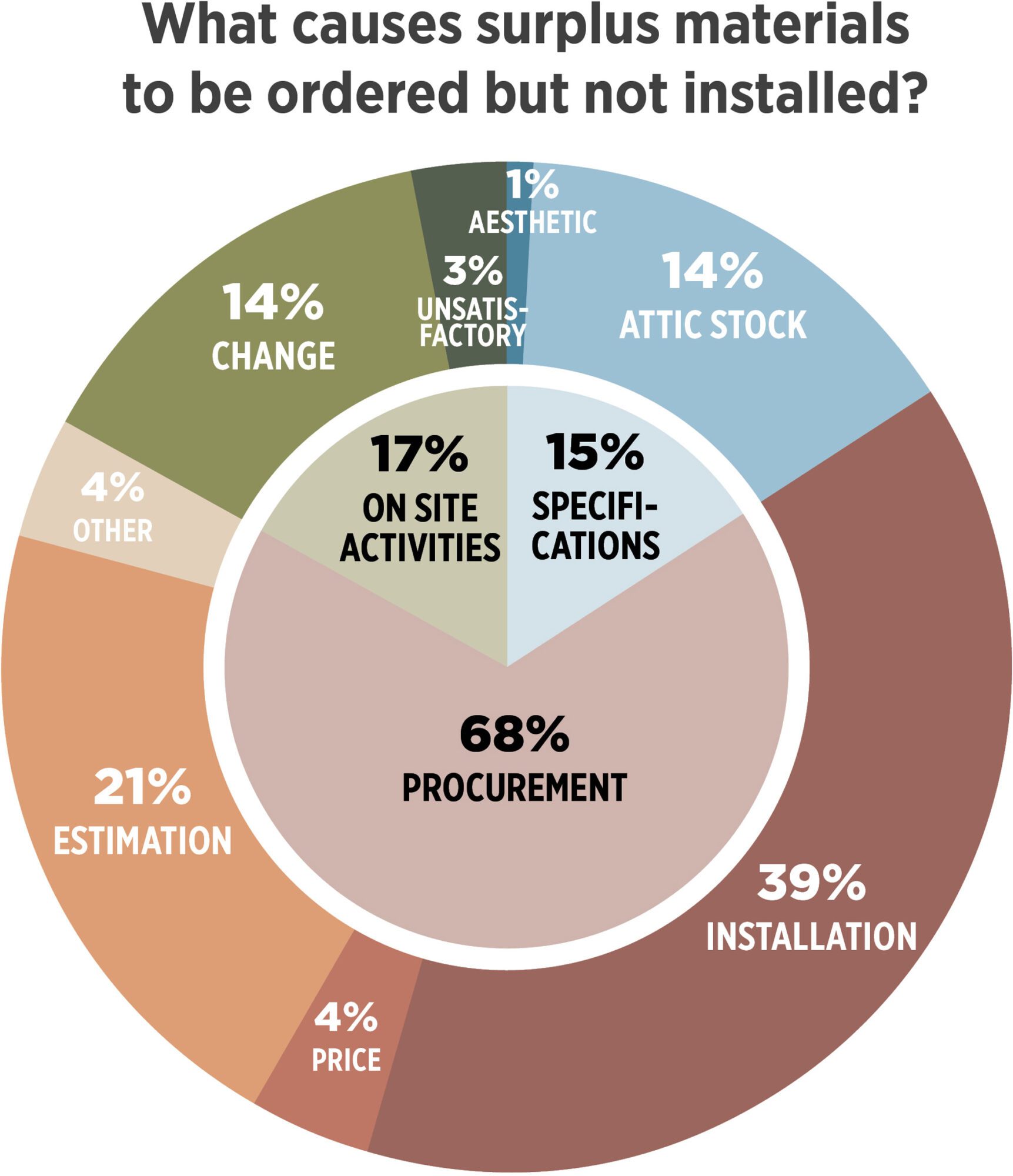
Typical reasons for surplus materials based on a study by the San Francisco Depart of the Environment.
In anticipation of maintenance needs, specification language often includes “attic stock” requirements, sometimes even when there isn’t storage space identified. To minimize surplus, designers and owners are encouraged to be more deliberate about the necessary attic stock quantities and their storage solutions. In addition, creating a surplus material plan can ensure items are not to be stored or discarded on job sites but diverted to previously established reuse resources or returned to the manufacturer.
Designers can also seek out local surplus stock when working on a new project. Consider connecting with local reuse/salvage resources to seek out surplus materials to incorporate into your new project. LMN recently inquired with a local flooring distributor about their available attic stocks to meet a project’s flooring needs and was astounded that there is a warehouse full of brand new, never installed materials mostly destined for the landfill. As discussed in Post 09 – Circular Economy + Products, discarded materials that still have remaining service life are wasted carbon emissions. Our responsibility to lower carbon impacts starts with materials already extracted and manufactured into products. Minimizing and rescuing surplus materials from being sent to landfill is one method that is easy to implement.
A note about takeback programs
Manufacturers often tout a takeback program associated with their products, but designers need to immediately ask about the documented success rate of these programs. Success rates generally remain low as there are often rules and restrictions before manufacturers are willing to make the financial investment. For example, materials like ceiling tile and carpet often require a large enough quantity to be palletized before the manufacturer will take back. Even with the intention to have concerted, localized efforts to collect materials, the responsibility of collecting, storing, palletizing, and coordinating with the manufacturer becomes overhead risks for any one entity to take on. As few as 5% of carpet tiles make their way back to the manufacturers, and a small percentage of that is actually turned into new carpet. However, even if the remaining 95% returned to manufacturers, current infrastructure is not set up to handle the quantity. For these reasons, minimizing the initial surplus is a surer way to reduce unnecessary waste and its associated carbon emissions.
The Problem with Carbon Neutral Interiors Claims
Many interior projects do not have significant scope in updating energy systems of the building they occur within, but they often have an extraordinary amount of engagement over existing space plan, materials, and FF&E that are inherited from a prior interior design. This means the focus on embodied carbon is paramount to low-carbon interiors; a unique design opportunity exists to reach near zero carbon interiors by retaining-in-place, salvaging, and involving surgical renovation and salvaged materials that is much less possible with new buildings.
Many carbon neutral interiors claims rely on carbon offsets. Covered extensively in Post 08, nearly all carbon offsets do not support rigorous net zero carbon or carbon neutrality claims. Offsets are often used to avoid the difficult work and design rigor required to value existing materials and pair this with updated ways of manufacturing products to be part of a circular economy. Together design and manufacturing can result in a low-carbon and salvaged material palette that nears zero-carbon and contributes to a circular economy.
Carbon sequestration and storage are often promoted as a way for individual products, and thus overall projects, to reach carbon neutrality. While this is accurate in the short term, these carbon benefits primarily last while the product is in use. Wood and other bio-based products sequester carbon as they grow and can store it in construction products. Forests would have continued growing and sequestering carbon, so the baseline condition needs to address this continued sequestration and storage as well as forest management carbon balancing. Products made from agricultural wastes, which otherwise would have decomposed and released carbon into the atmosphere, have a different carbon baseline.
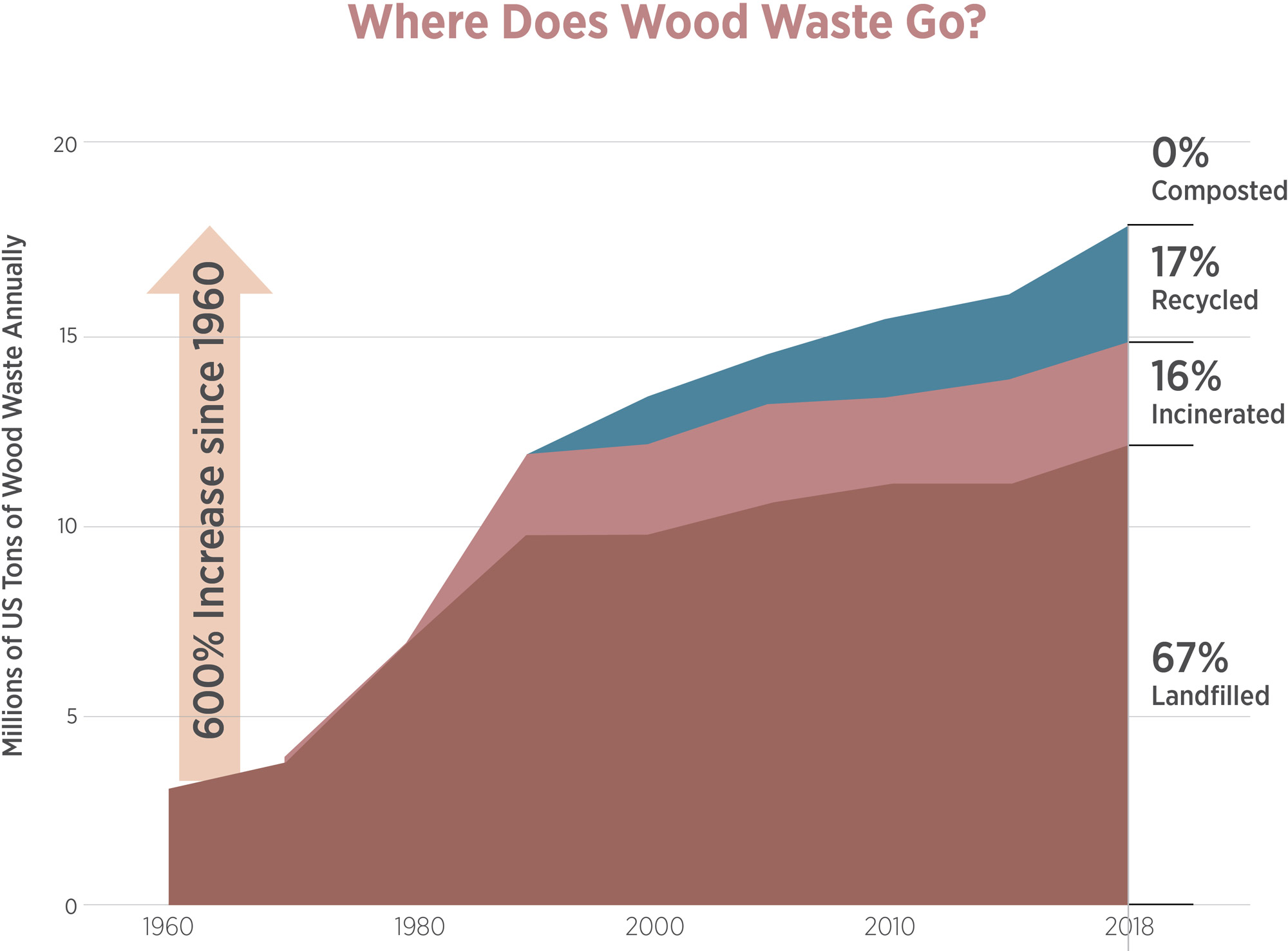
While wood waste stores biogenic carbon, roughly 67% ends up in a landfill while another 16% is incinerated. Paints and stains make most wood products unable to be recycled or composted, but painted or stained wood can be refurbished and reused which is much more likely if solid wood is used.
In short-lived interiors products, the benefits for carbon sequestration and storage are significantly diminished when they are sent to landfill or incinerated, releasing that carbon back into the atmosphere. While biogenic materials can continue to store carbon even if they are landfilled under anaerobic conditions, a new material is needed in its place. Worse, if the material is incinerated, the carbon gets released back into the atmosphere, spoiling claims of carbon neutrality. Post 10 suggests ways to account for existing materials during renovations, assigning values to existing materials, including biogenic carbon.
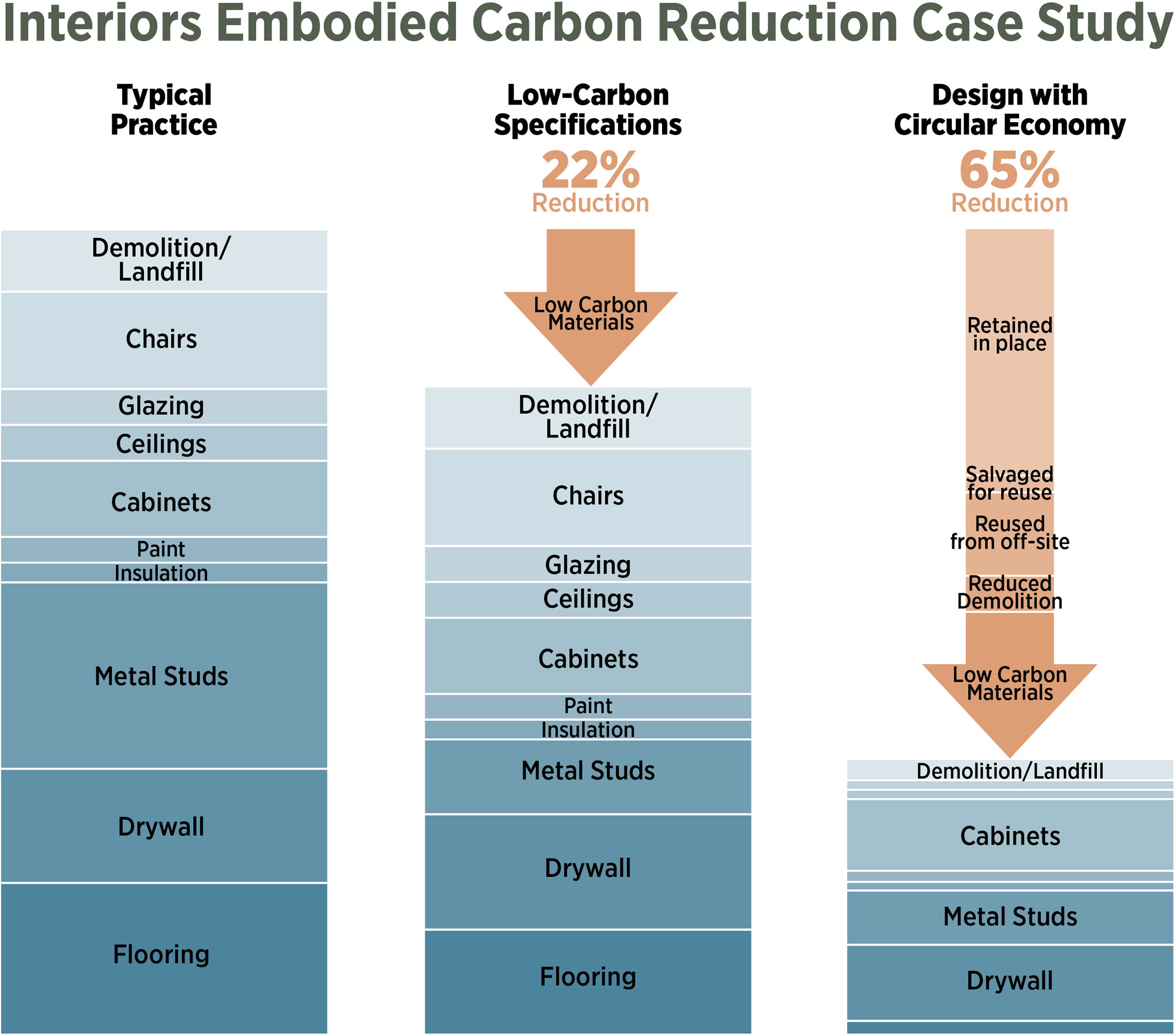
A circular economy case study focused on material reuse to lower embodied carbon. The results for one project showed that purchasing new low-carbon products could reduce embodied carbon by 22% while re-imagining and surgically inserting new materials while saving existing materials could reduce embodied carbon by 65%.
The Path to Zero Carbon Interiors
Currently, design for typical commercial and retail renovations start with a cleared, shelled space with prior renovations demolished, sending valuable materials that still have service life remaining to the landfill. Every time this happens, carbon pollution emitted from the prior design is wasted. To reach carbon neutrality, we must first be willing to recognize and address the whole scope of our carbon footprint, which would include taking responsibility for the existing conditions a renovation is to replace. At the same time, the industry needs to focus on changing the way we practice to minimize upfront carbon emissions by:
- First, maximize contributions to the circular economy via deconstruction, plus procurement or refurbished products from the circular economy.
- Second, when new products are necessary, use low-carbon products and carbon-sequestering products, designing with reusable, deconstructable materials.
- Carbon offsets should not be used to claim carbon neutrality.
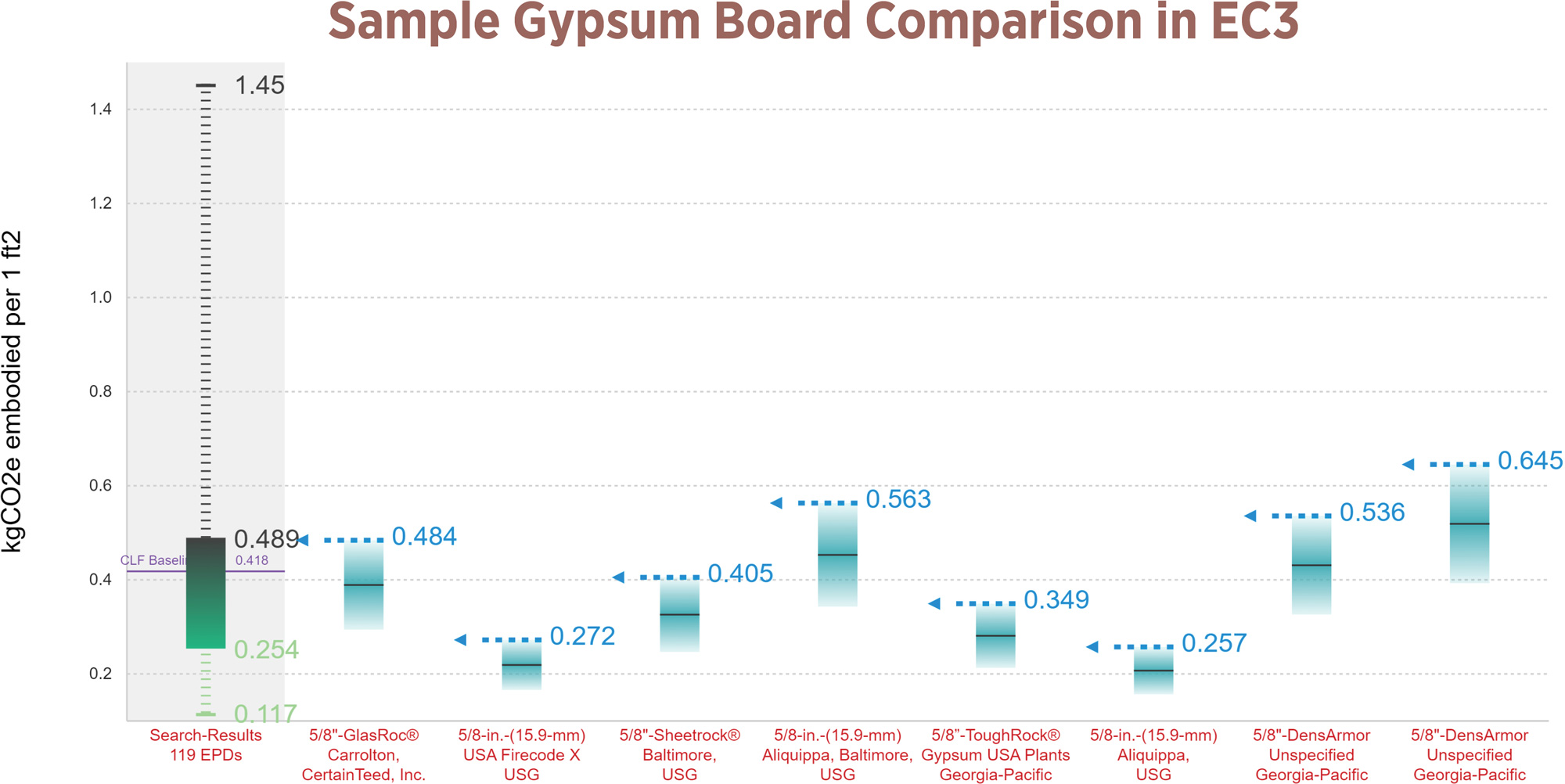
An EC3 materials search allows products to be compared for Global Warming Potential in stages A1-A3. Note that many interior products are not functionally equivalent, so it is up to the user to set the class of products compared. This is a sample of various 5/8” gypsum boards produced at plants in North America. The error bands are generated by EC3 based on the data confidence of the Environmental Product Declaration itself.
Below are the steps to take, questions to ask, and things to consider each step of the way as we design our way to zero carbon:
- Track a project’s overall embodied carbon and include as much of the interior scope as possible. Focus on the top worst offending material categories, including scopes mentioned in this post not typically included in LCA frameworks. Currently there are free tools like the CLF’s Tenant Improvement Calculator or EC3 (Embodied Carbon in Construction Calculator) that can help. CLF’s TI calculator uses average product data, while EC3 has a database of product-specific EPDs to track progress and compare against industry-average EPD data. There are likely specific materials to each project that requires a bit more digging. When EPDs are not available, estimates are possible using available data. For example, for systems furniture, multiply the volume of the composite panel material in question by industry average EPDs for the panel material, or use the 2011 FIRA publication.
- Identify areas of high impact and find opportunities to lower embodied carbon. Consider the following strategies in rough order of carbon saving potential:
- Minimize unnecessary new carbon emissions
- Right size the project; how much actually needs to be built?
- Maximize existing material reclamation for new uses on site. Do a reclaim walk-though prior to demolition and work existing conditions into the new design where possible.
- Streamline palettes; are all the materials necessary for the success of the space?
- Aim for necessity, longevity, flexibility, and adaptability; will it stand the test of time in terms of performance, function, and aesthetic?
- Pay attention to material modules and sizes; will the design create unusable leftover material and therefore create unnecessary waste?
- Reuse, Reclaim, and salvage
- Can the existing materials and conditions remain in place, be repurposed, or relocated on-site?
- For new materials that are needed, can materials with remaining service life be found offsite? More and more, there are businesses offering second life products, such as Davies for remanufactured systems furniture, Reseat for second use furniture, and Doors Unhinged for salvage doors. There are also efforts in providing resources to connect building professionals and reuse resources, such as Rheaply and All For Reuse. It is worthwhile to seek out local salvage and reclaim specialists as well, such as ReUse Consulting in Seattle.
- Seek out local surpluses through material distributors and installers. Likely they have new materials never installed stored in a warehouse.
- This video provides visual explanation of the process of achieving circularity in commercial construction.
- Optimize (if new material is needed, what is the lowest impact option?)
- Does the product have an EPD? Prioritizing materials that provide environmental impact transparency.
- Prioritize low carbon or carbon neutral materials from manufacturers who work to reformulate their product design and retool their manufacturing process to lower the energy and carbon pollution that goes into their products. Look out for manufacturers that claim carbon neutrality based on offsets, without improving the manufacturing practices or ingredients.
- Prioritize materials with high recycled content that are easily recyclable.
- For product categories with easily accessible EPDs, consider adding a Carbon Cap in Specifications to the lowest third GWP of available products. Building Transparency has published template specification language to make this easy as part of the ownersCAN Embodied Carbon Action Plan.
- Waste diversion (how can I keep it from going to the landfill when it’s no longer useful)
- After preserving as much as possible from the existing conditions as mentioned in Strategy B, provide a plan for materials that need to be removed from project site that diverts it from the landfill. Engage and salvage specialist early in the project and make sure to allot additional design and deconstruction time.
- Design for disassembly. Examine design details to create ease of un-installation and preserve the integrity of the original material to maximize potential for re-use later.
- Right size attic stock. Make sure the client has intention and space to use and store attic stock.
- Create a bill of materials and an end-of-life plan outlining how each material can be reused and diverted from the landfill. The industry has not coalesced around the best format for this yet.
- Offsets
- The last resort. When the project has eliminated as much of the upfront embodied carbon, offset the rest with a trusted source.
Conclusions
Interiors, including furniture, can be over half of the embodied carbon of a building over time, and once the structural and envelope carbon investments have been made, nearly all embodied carbon pollution will be from interiors scope. Low-carbon and net-zero carbon interiors requires rethinking design: instead of starting with a clean floor plate (a restoration clause in some tenant leases), it means working with the existing layout and materials to make surgical and complimentary modifications, salvaging any removed materials. It also means increasingly engaging with a circular economy: salvaging materials during demolition, designing with salvaged materials, and procuring salvaged materials.
Thanks to those who helped!
Please email any questions or comments to Kjell Anderson, kanderson@lmnarchitects.com
Thanks to our external collaborators and peer reviewers
Sean Darras, Lightly; Simona Fischer, MSR Design; Meghan Lewis, Carbon Leadership Forum; Leela Shanker, Flint Collective NYC; Kristen Fritsch, Elkus Manfredi Architects; Dave Bennink, Re-use Consulting
LMN Architects Team
Jenn Chen, Justin Schwartzhoff, Kjell Anderson, Emma Gaulke-JanowskiPosted: 01/16/2024
The text, images and graphics published here should be credited to LMN Architects unless stated otherwise. Permission to distribute, remix, adapt, and build upon the material in any medium or format for noncommercial purposes is granted as long as attribution is given to LMN Architects.
- Minimize unnecessary new carbon emissions