#emergingtechnologies, #fabrication
Façade Design & Digital Fabrication
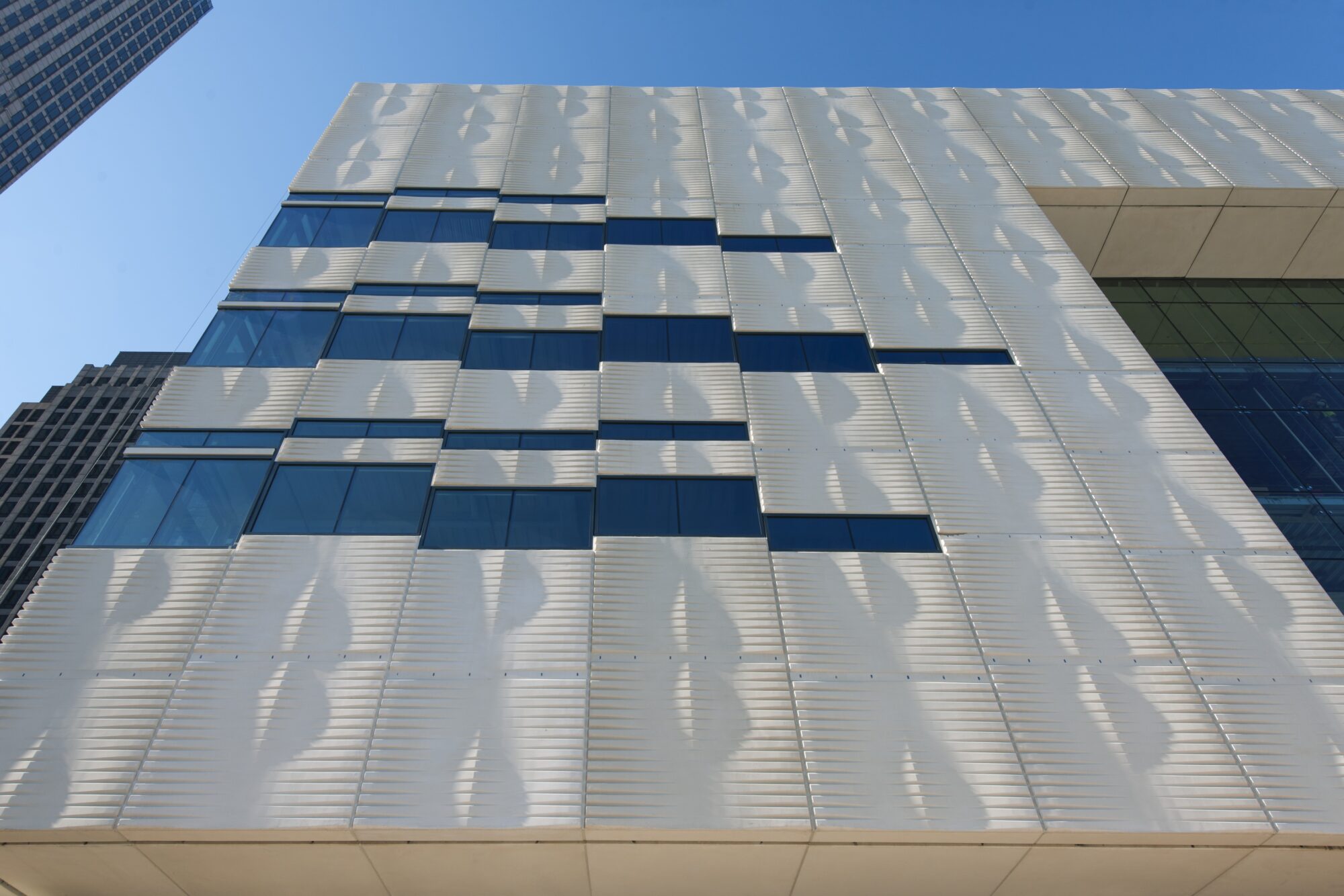
Concept
The Global Center for Health Innovation building is conceived as a monolithic hovering solid, whose main atrium is expressed as a vast carved opening within the east elevation facing the Malls in downtown Cleveland. The hovering solid allows the ground level to connect informally to the life of the public park, while unifying the upper three floors as a block of medical showrooms surrounding a full-height atrium. Our goal was to develop a building whose architectural language would negotiate the vast scalar differences between the large civic expanse of the Malls and the surrounding smaller scaled streets and neighboring buildings. In addition, we wanted to develop an envelope system that both reinforced the building’s sense of permanence, but also revealed increasing levels of textural detail at various proximities.
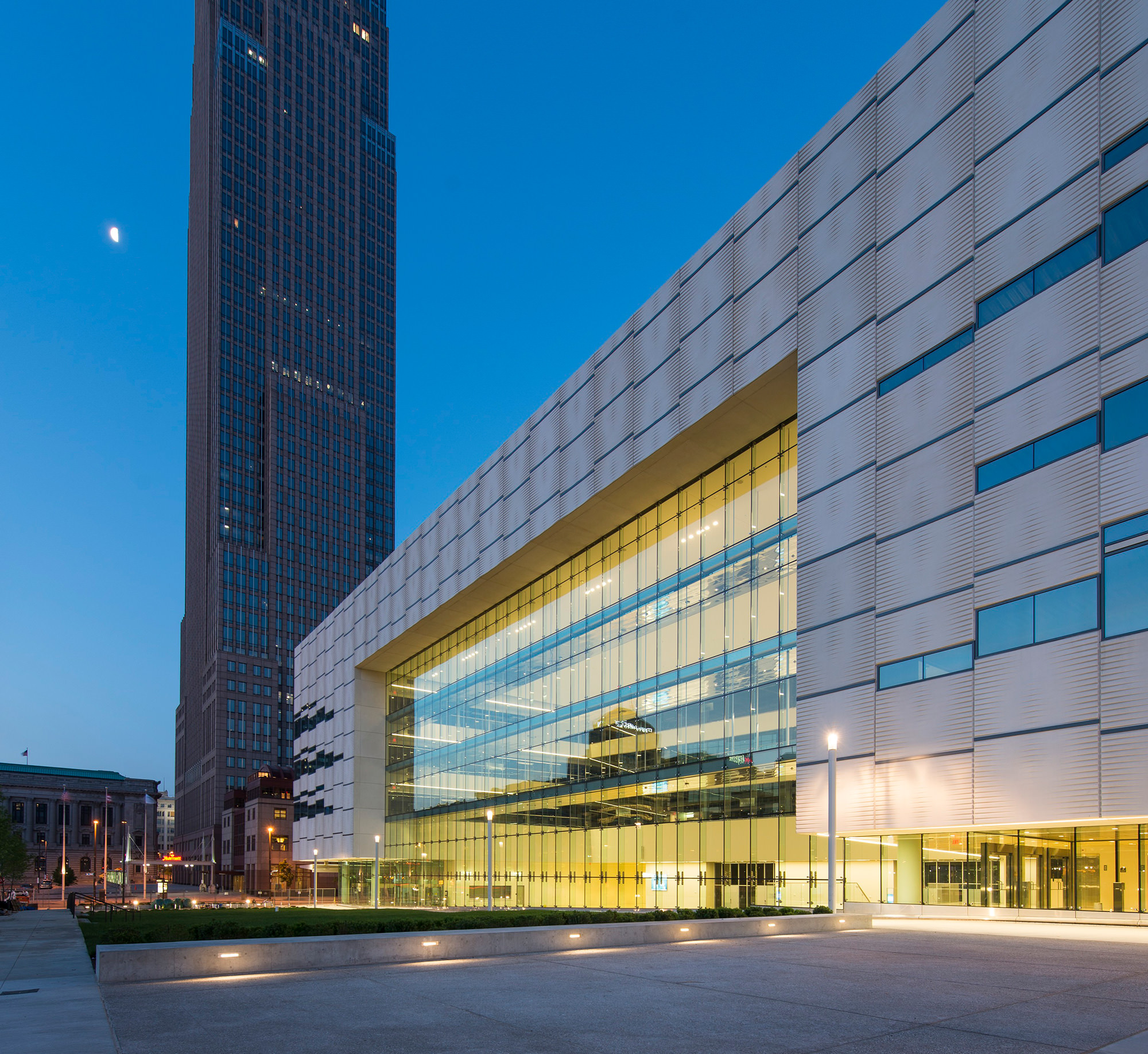
The building is conceived as a monolithic hovering solid, negotiating between public and program space.
Tectonics
Our interest in digital design and fabrication immediately led us to embracing the use of precast concrete. A panelized, precast concrete wall system is a cost-effective way of enclosing a building, and it complements the building’s historic context with its monolithic, permanent quality. The ability to form concrete using computer numerically controlled (CNC) tools and formwork affords unique opportunities for our digital models to directly control the production of building components. Most of all, we were inspired by the limitless formal capabilities of concrete, and eager to develop a unique, sculptural facade system that would easily adapt to multiple contextual and programmatic requirements.
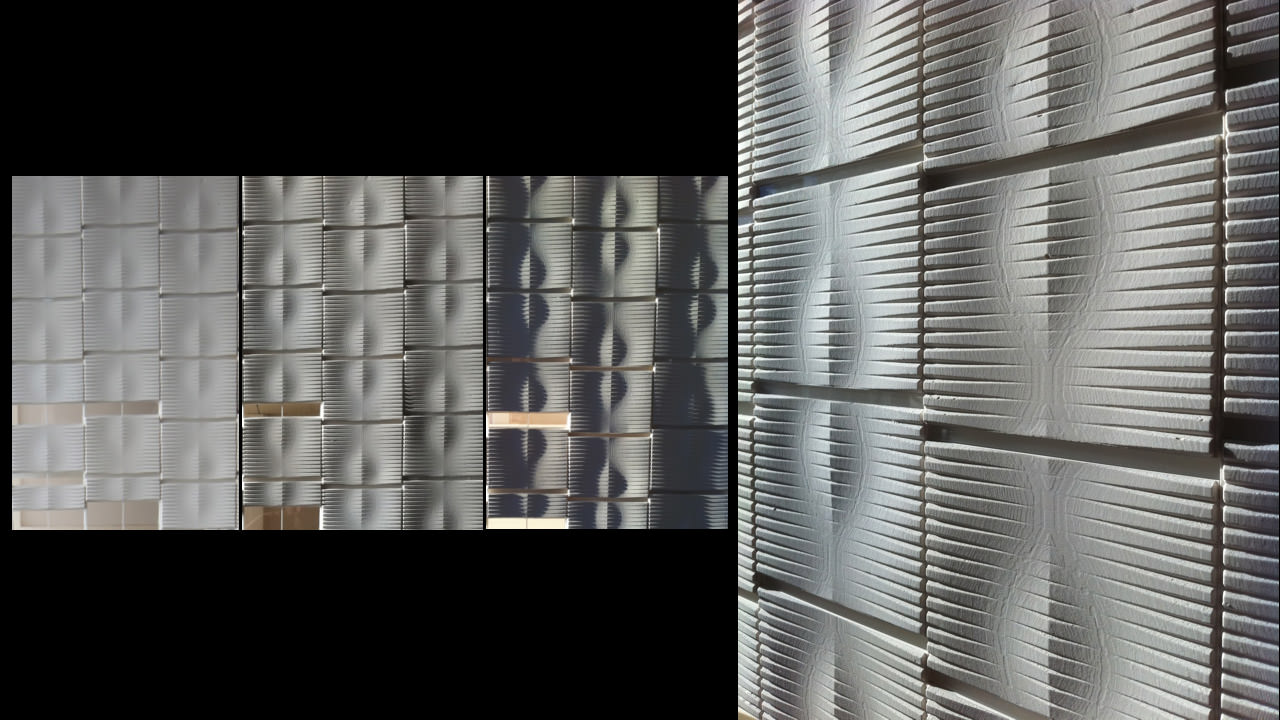
The precast concrete envelope system both reinforces the building’s sense of permanence, while also revealing increasing levels of textural detail.
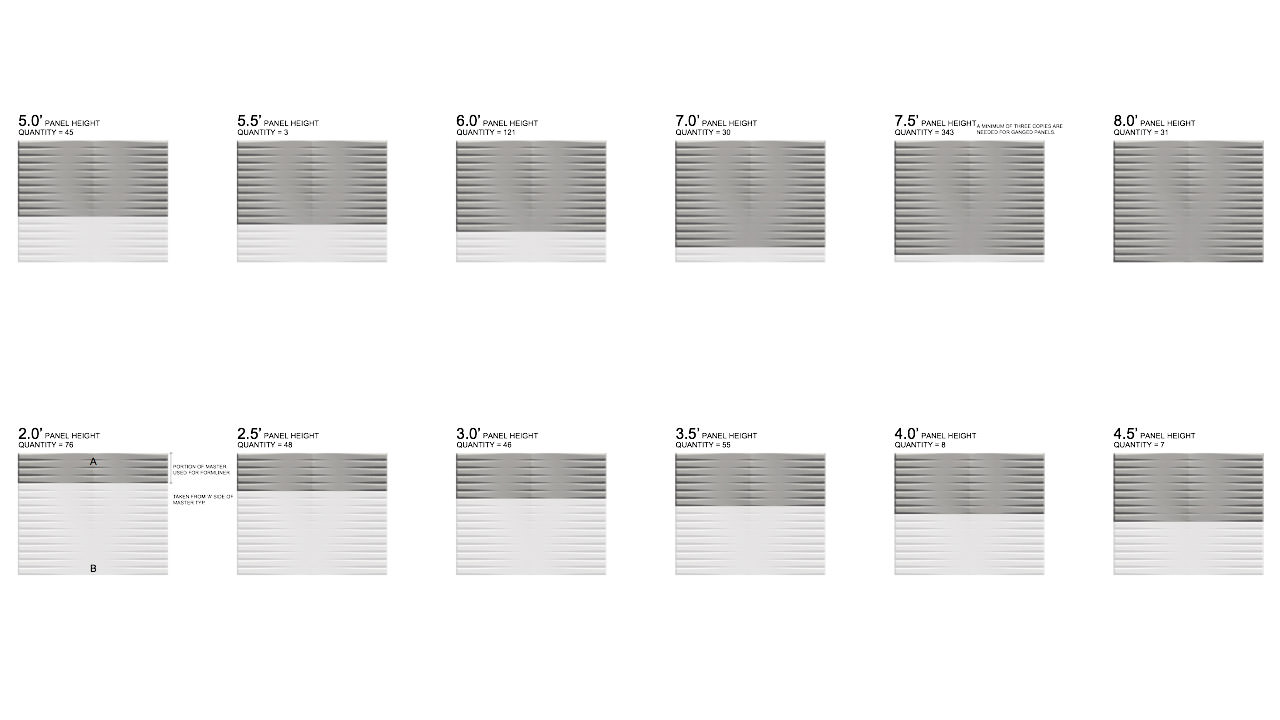
Concrete’s ready applicability to digital fabrication systems means panel variations are easily rationalized, allows a direct interface between the architectural model and the production shop.
Generative Modeling in Grasshopper
We developed a system of controlling the basic components–glass and concrete—using a greyscale image, allowing us to control the location of windows and concrete by simply ‘painting’ the desired array on a canvas. By using this generative approach to drive the configuration of the new system, we were able to study and evaluate new iterations almost instantaneously. With each digital model generated we were further able to run day-lighting and energy simulations, giving the design team critical performance data used to optimize the system. One of the major advances that LMN made in this project was the ability to use the generative design model to develop and control a variety of design and documentation requirements of the façade system. To facilitate this we built our own software plug-in to allow our generative design tool to directly control our parametric Building Information Model (BIM). This link enabled us to completely regenerate an entirely new façade configuration–and its requisite construction, component, and quantity information—in a matter of minutes, drastically increasing the feedback loop with our design assist team. The use of this integrated approach gave the whole team confidence that as changes were made, each and every component would be accounted for, enabling real-time performance and cost review.
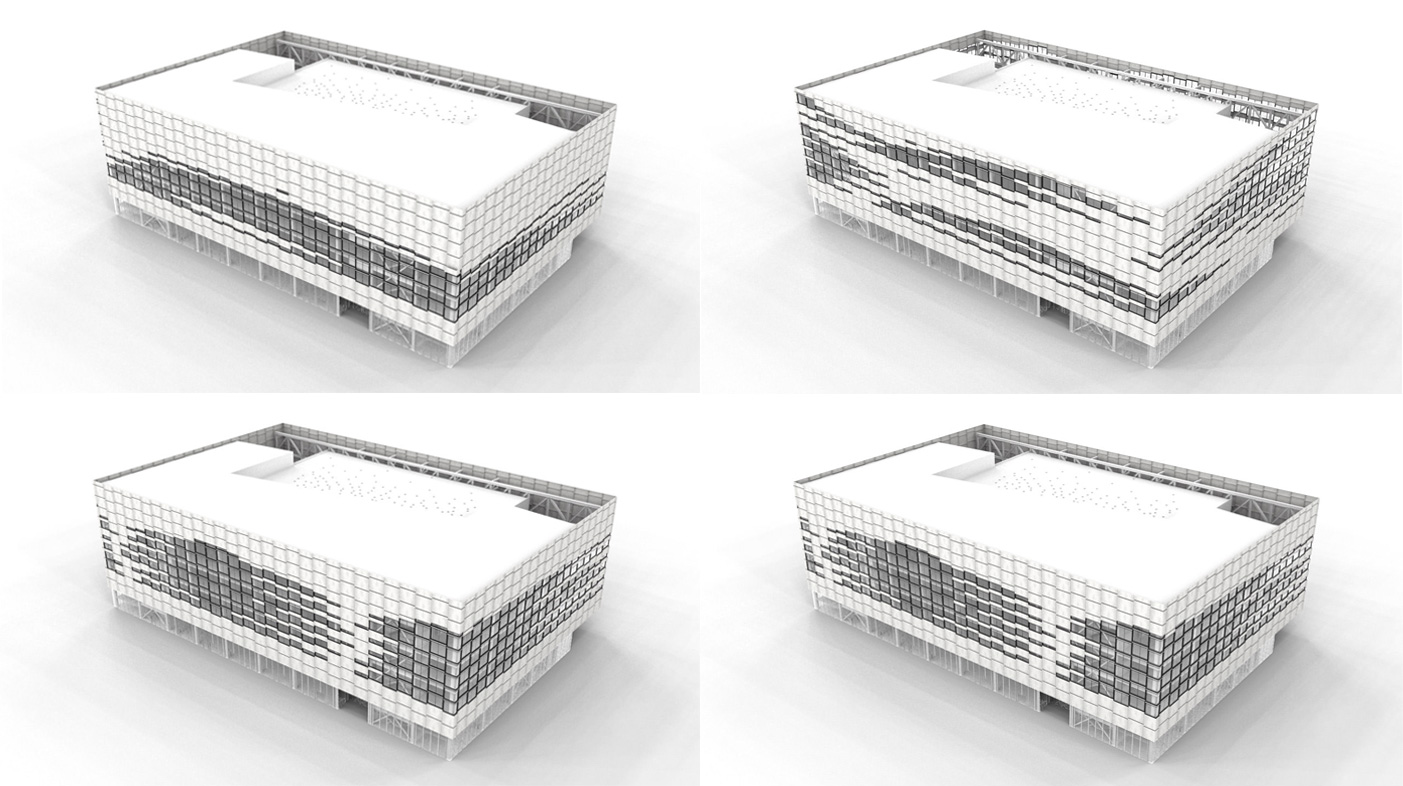
‘Painting’ the window pattern, and early design iterations.
Rapid Prototyping and Digital Fabrication
LMN worked very closely with the precast concrete fabricators in developing the CNC machine built form-liners from which the façade panels are cast. Our in-house digital fabrication tools, including a high resolution 3D printer and laser cutter, served as the basis for all in-house testing. The use of rapid prototyping technology in the office has allowed us to study new concepts both digitally and physically, and has enabled us to quickly evaluate design iterations for constructability, performance in natural lighting conditions. Rapid prototyping is a fundamental tool for us at LMN in developing new approaches to project design and delivery. The instantaneous feedback loop encourages substantially more design exploration than ever before, leading to more ideas being tested more rigorously and ultimately yielding powerful, innovative design solutions. Moreover, this direct-to-fabrication process provides an expedited and more accurate submittal process for the actual built components; the digital 3D files LMN develops in-house are the same files the fabricator uses for final production.
Process Makes Progress
Perhaps the most significant gain to come from these advances in our working process was the immediate establishment of a high level of trust between architects, consultants, and fabricators. We were able to connect our generative work to multiple documentation methods and file formats, each tailored to the needs of our collaborators. Any change made to the system or configuration was immediately documented, greatly easing the work required to track quantities and costs.
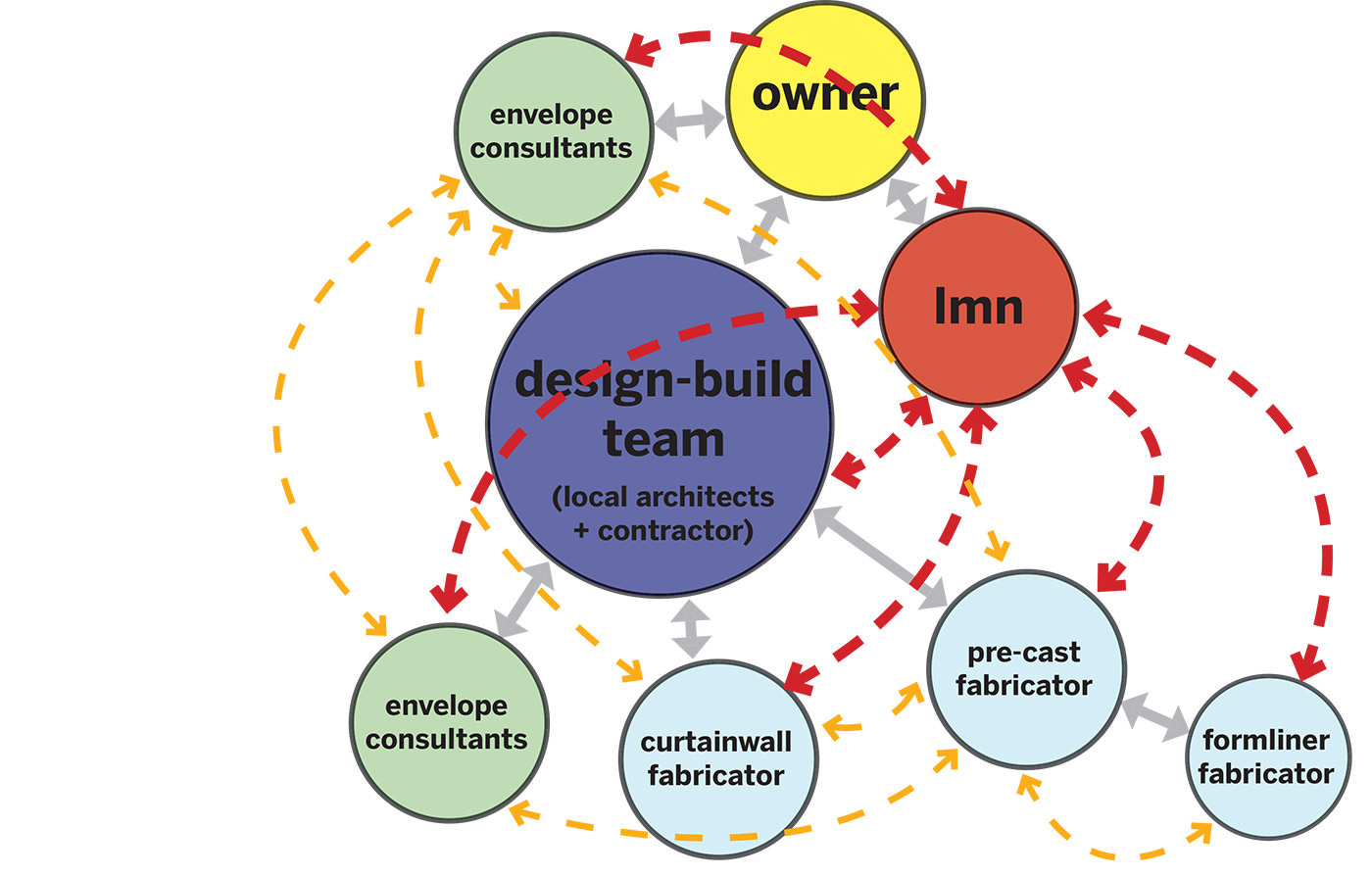
Collaborative connections between design and delivery team members, enabled by custom technology built by the LMN Tech Studio, allows disciplines to work iteratively in parallel.
Technological agility is the key component in delivering highly customized and complex projects within achievable budgets and schedules. At LMN, we are finding that design collaboration and project delivery can be increasingly more productive and efficient when paired with the nimble use of state-of-the-art digital design and analysis tools.
Schedule Compression
The Global Center for Health Innovation design process explored new territory in the utilization of technology to gain a schedule advantage, resulting in a more direct and time-effective manner to coordinate information between the design team and contractor. LMN undertook this process in the context of a 950,000 SF combined medical mart and convention center facility in the downtown core of Cleveland. As the owner’s architect, LMN also coordinated the design with the design/build delivery team on the owner’s behalf.
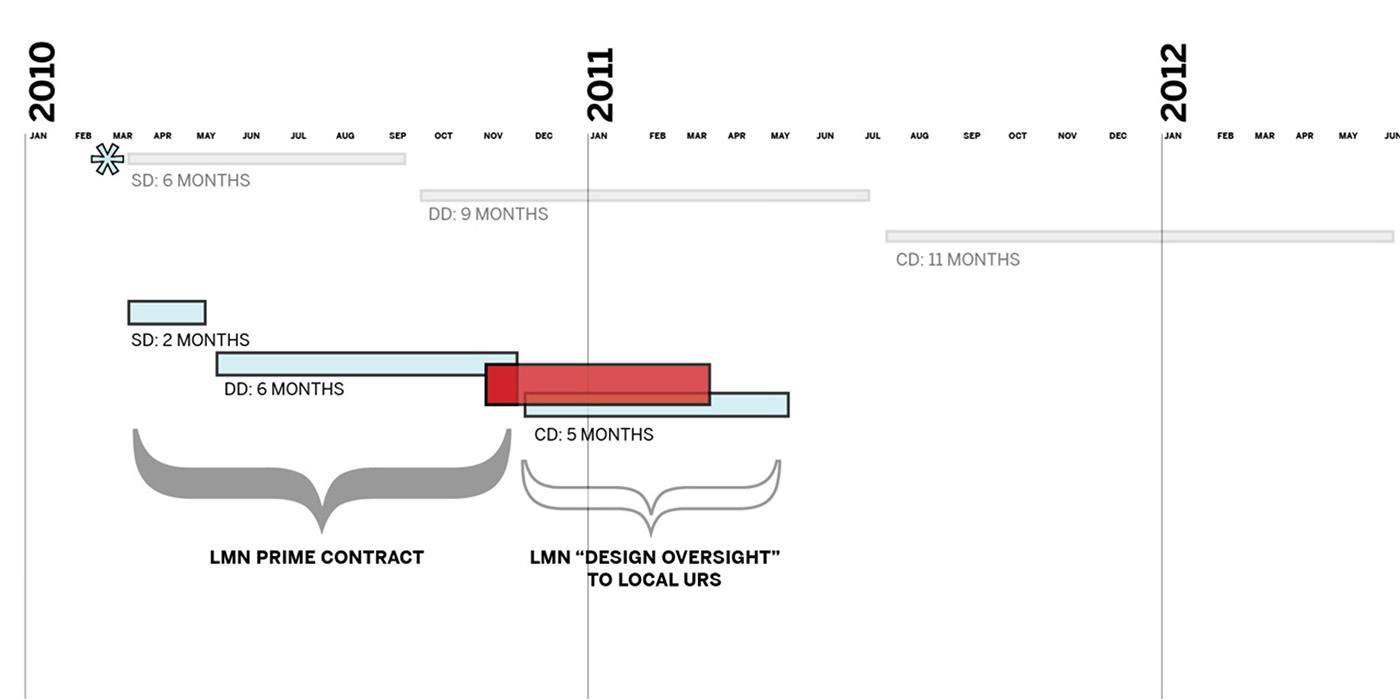
Time from Concept to Shop Drawings: 3.5 Months
From the beginning of our work for the new Cleveland Medical Mart and Convention Center, a very aggressive schedule was the project’s biggest challenge. Due to county public funding requirements, the schedule was established with thirteen months for pre-design through final construction documents, half the time normally spent on a project of this scale and complexity. In our role as design architect, we delivered our design development package to a local design-build team giving us only 8 months to complete a set of bridging documents from which the work would be built. Our final challenge was given to us very late in that 8 month process; the client requested us to develop a new façade design. This forced us to create faster ways of designing and working with our consultants, design-assist partners, and fabricators in order to resolve many design challenges and bring the façade package from concept through shop drawings in fewer than 4 months.
With a diverse array of digital design and coordination tools, we were able to simultaneously develop our global façade geometry while fine-tuning the details of the system. To facilitate this we built our own software plug-in to allow our generative design tool to directly control our parametric Building Information Model (BIM). This link enabled us to completely regenerate a new façade configuration in a matter of a few minutes, drastically increasing the feedback loop with our design assist team. This integrated technological approach gave the whole team confidence that, as changes were made, each and every component would be accounted for, enabling real-time performance and cost review.
We also worked very closely with our precast concrete fabricators in developing Computer Numerically Controlled (CNC) built form-liners from which the façade panels will be cast. Our inhouse 3D printer and laser cutter served as the basis for all in-house testing, allowing us to study new concepts both digitally and physically.
Rapid prototyping is a fundamental tool for us at LMN in developing new approaches to project design and delivery. The instantaneous feedback loop encourages substantially more design exploration than ever before, leading to more ideas being tested more rigorously and ultimately yielding powerful, innovative design solutions. Moreover, the direct-to-fabrication process provides an expedited and more accurate submittal process for the actual built components; the digital 3D files LMN developed in-house are the same files the fabricator will use for final production.